31 December
Top 3 videos: The 3 most-watched of my videos this year are
- the
compilation
of the annual German fischertechnik convention 2015, this year in
Dreieich,
- the first
video I made about my TXT Discovery
controller,
- the
compilation
of the annual Dutch fischertechnik convention 2015 in Schoonhoven.
Discovery: Without a Python-version compiled for the new
firmware, it's not much use to do those experiments.
However, since ROBOPro was updated along with the firmware
(although they're separate entities), another test I can do is
running the colour recognition test again, for the 6th time. See
this short
video.
RPi: Last time, 1 LED kept burning and in an attempt to
solve it...nothing works. Then with replugging (so: not
replacing!) a few wires, all works (?!) Then, running the C++
version. LED 2 continues to burn, so there must be a bug in the
C++ code. And there is a wrong LED setting: 4 - 5 - 3, where 3 =
110
2 instead of 4 - 5 - 6 where 6 = 011
2. [
2
means binary. For completeness I should write 3
10 or 3
D
to indicate it's a decimal digit, but this is usually left out
because we use decimal in daily life.] Then it shows that the
control is the reverse from what is intended: the control by RPi2
stops the counter on RPi instead of starting it. Oops. Sigh. See
the
video.
Other problems are either with the RPi2 or with the operating
system (Raspbian):
- during the experiments, ssh and vncserver were restarted.
Usually, I can reconnect after a short time.
- at times, the restart doesn't happen.
When the restart doesn't happen, I need the HDMI video + keyboard
+ mouse to either kill processes or restart the RPi2. This means
unplugging the those from the BB, which is a nuisance.
So I will try a different solution: buying another Serial Pi Plus
and a null-modem cable and see if I can do without HDMI etc.
Hand: Continuing with the arm, I have to relocated the
controller and the compression engine. But before I can do that, I
will have to extend the tubes since they are at least 50 cm too
short for after the relocation. However, I worry about the quality
of the new silicon tubes:
shabby doesn't sound promising
as side note with the qualification. And the old quality tubes are
too short. Also the upper part of the arm-base bends through
because of the weight of the hand. To solve this, I place
stabilizers. After some thinking, the extension solution may be
the use of t-pieces and stoppers. See the
video.
Mirft: Last time ended with the conclusion that a redesign
of the gears was the only way to go on. However, the construction
of the body is such that this is not possible. Another option is
to add a supporting rod under the body that would prevent to body
to leave its height. With a distance of 10 cm between the lower
rig and the floor shouldn't be too difficult, but the question is
what the rod should be made from. For now I take 2 iron rods and
put one up front and one in the back.
1
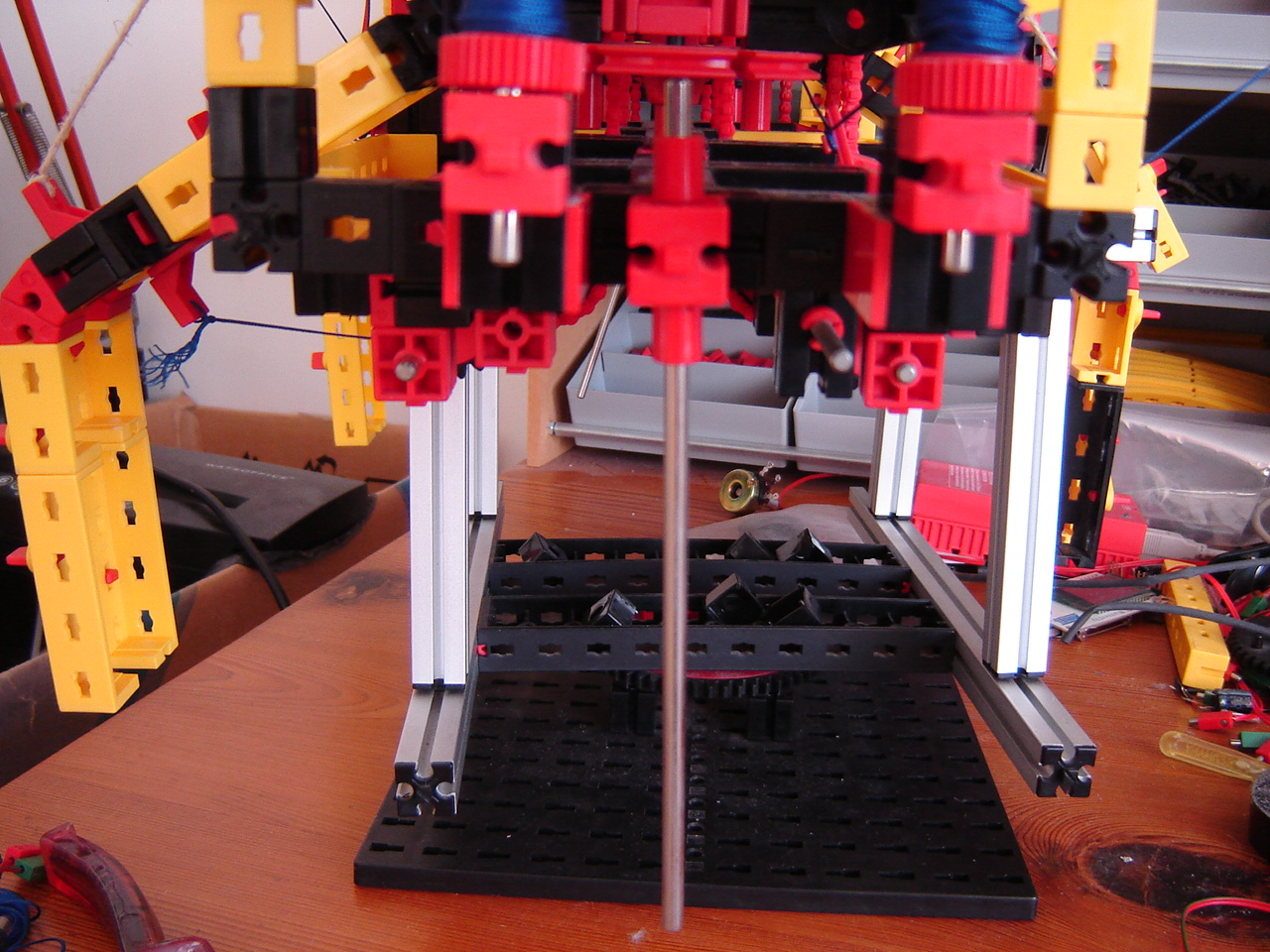
2
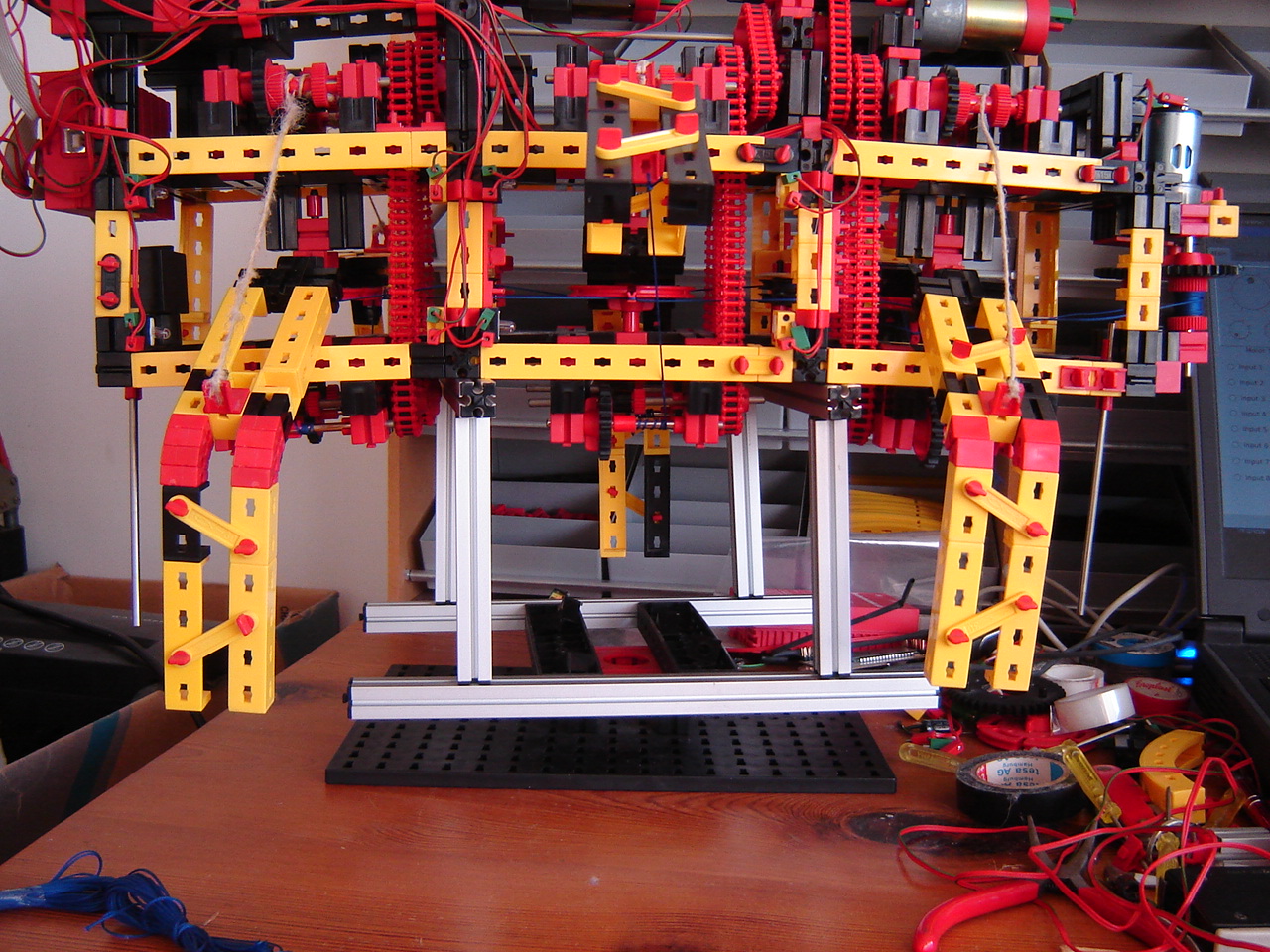
The floortest reveals that they're not connected very stable so I
have to modify the horizontal motor setup to fix the back-rod.
3
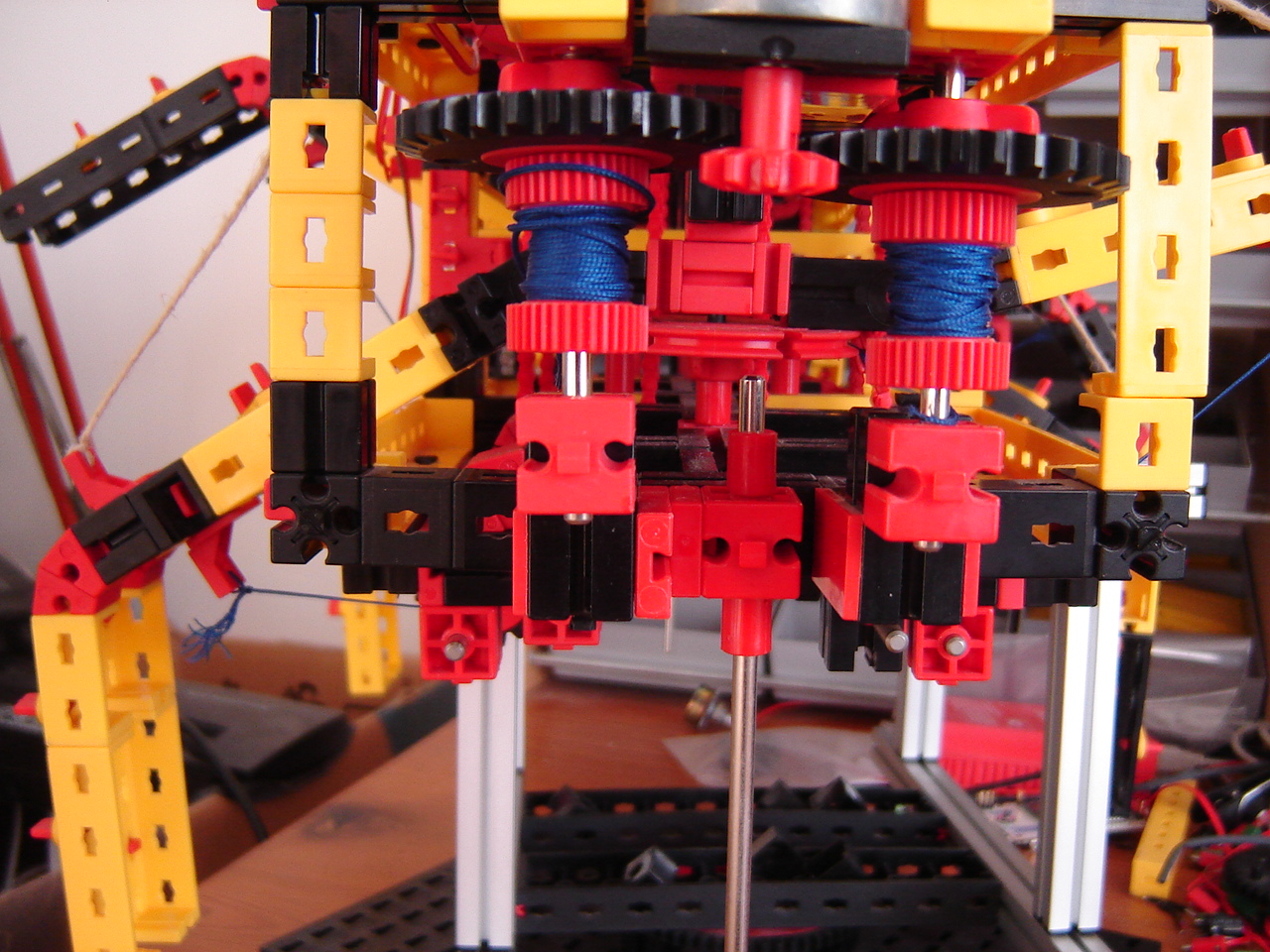
4
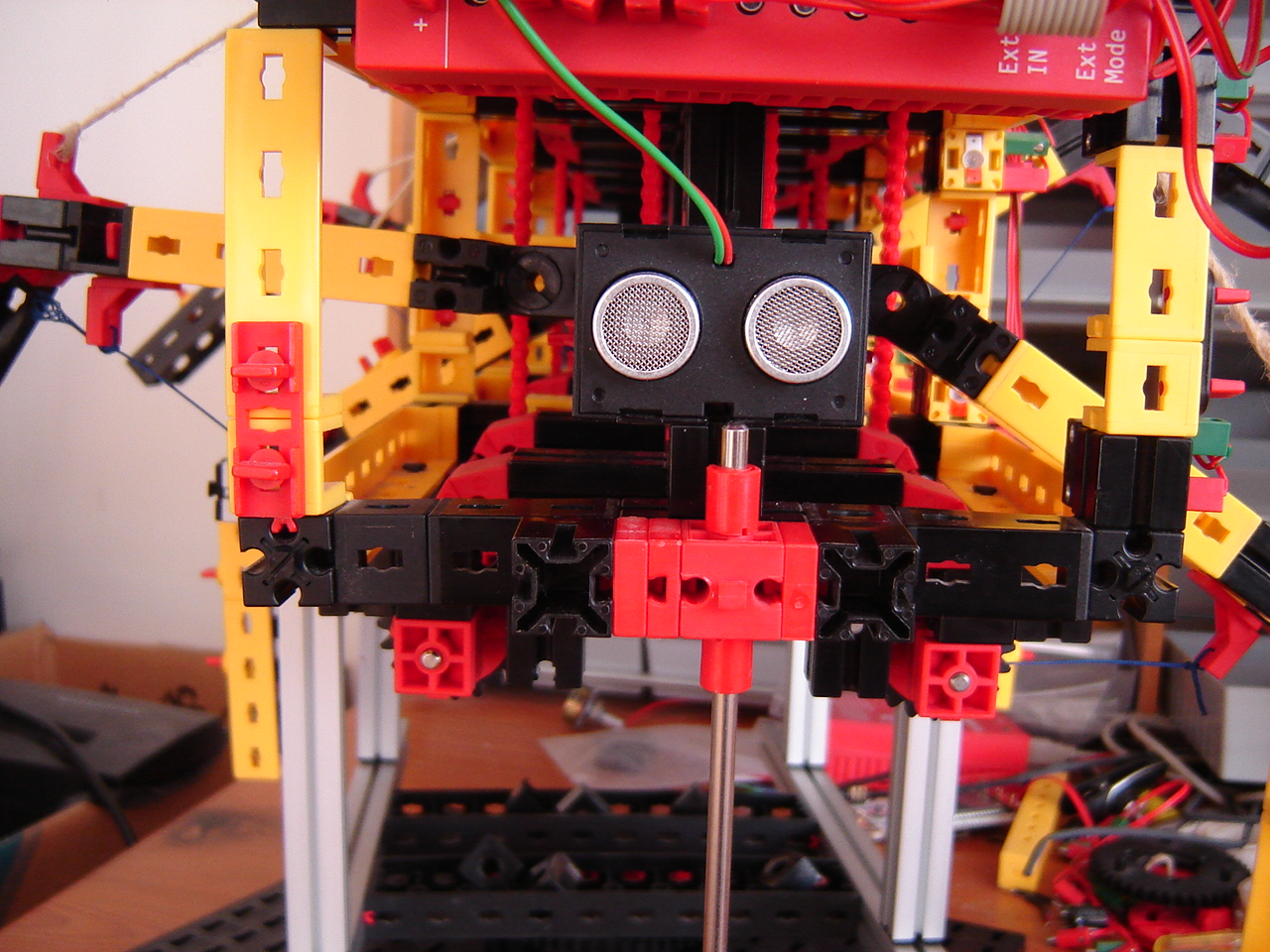
After this, the floortest goes fine: it stands on the rods
and the legs prevent falling sidewards. See also this
video.
25 December
Mirft: The failure of the last floor test is once again due
to chain gears that are not fixed enough on the axes. When putting
the legs completely horizontal it becomes obvious that the gearing
has to change completely.
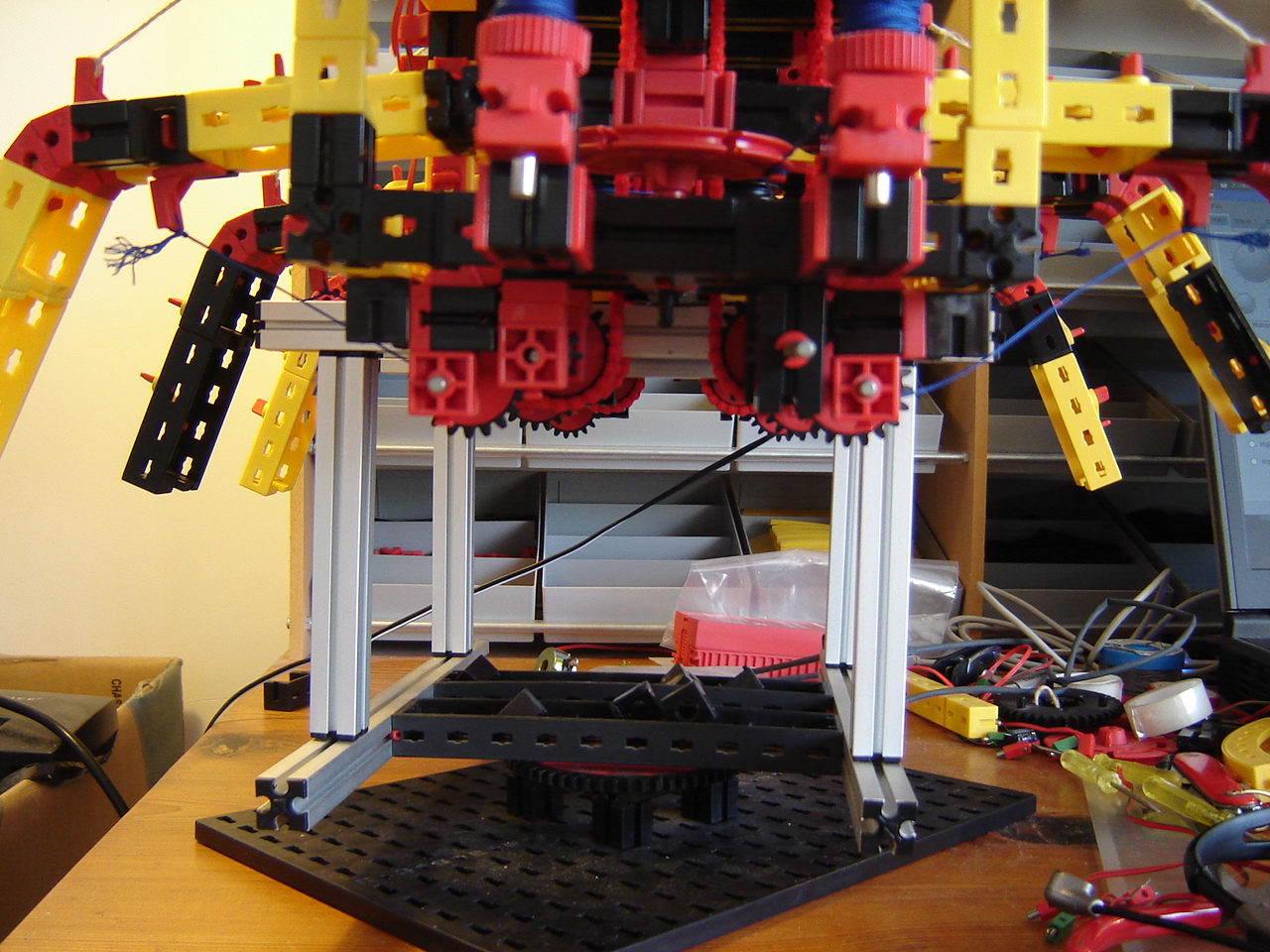
For the best result, the body obviously should keep its vertical
position, while the legs go up and down. This can only be achieved
with a decoupling of the vertical chains belonging to the same hip
wheel. Ideally, 3 more motors should be added but since I lack the
correct motors, I have to find a way to decouple the set of legs
and change gears. Making things even more complicated than they
already are. See the
video.
RPi: Since controlling RPi by
RPi2 works in Python, it should work in C++ as well. So I port the
RPi2 Python code to C++, which implies copying GPIOClass.cpp and
GPIOClass.h from RPi and hardly ever goes without typos and other
small errors. But after it compiles fine...there's a pin error
from RPi: it seems like pin 12 is always high. However, running
./gpiotest
on the RPi reveals that the pull-up resistor for pin 13 fails. See
this
video.
Another test shows that pin 18 goes wrong. To be certain, I remove
the flatcable from the GPIO and test again: only 15 fails. So I
test again with the flatcable in place: wrong again. Some testing
on the breadboard points in the way of the resistor between the
LED and ground being not secured. Replacing the resistor by 2
resistors with longer wires (see 2nd picture) doesn't show effect,
so more testing is needed.
Hand:With the algorithm so far complete, it's time to mount
the hand to the arm. That brings new challenges: do I leave the
fingers attached to the platform (for now: yes), how do I mount it
on the arm: flexibly or rigid, are the tubes long enough (eh, no),
etc, etc. See this
video.
BB: Continuing with OpenCV, I still have an issue with bits
and channels of images.
watershed needs an 8-bits
3-channel image, while
findContours gives a vector of
points and no image. By which my conclusion is that this won't
work. Conversion from vector to image won't work either: most
attention on forums (with answers) goes from image to vectors. See
this
video.
18 December
Mirft: With focus on the upper gears, I manually adjust
them: both the chain wheel and the cog wheel need to be fastened
on the axis.
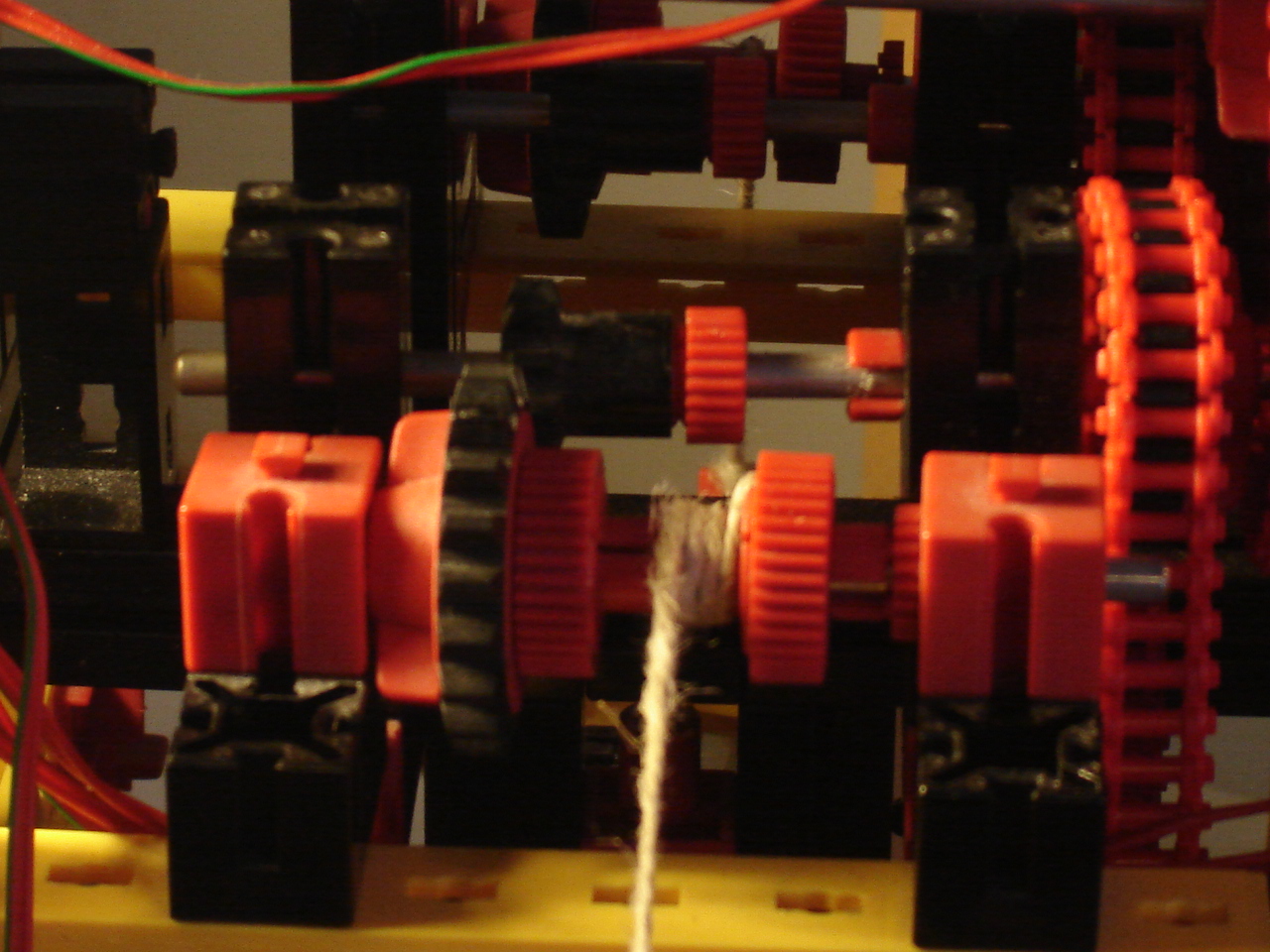
After that I have to manually adjust the vertical position of the
legs again. And when all legs have been set, it's time for yet
another test...or 2 and that doesn't go entirely as expected. See
the
video.
Discovery: As a funny, I added the fan from the TXT set to
the robot. There's 1 motor output free, and the small motor
exactly fits the fan. Unfortunately, the maximum speed in Python
is only 512, so there's hardly any propulsion from it.
Recently, both a new firmware and new ROBOPro version came
available and oddly, the main laptop doesn't recognize the TXT
anymore. Hence there is no firmware update possible. However, the
old laptop that I use for the TXT and Mydfir, does recognize the
TXT. So after updating ROBOPro on there, the TXT firmware is
nicely updated and should be capable for I2C and other fun stuff.
When adding the fan control to the code, there's no problem at
first. But then the shit hits the fan, sort of. See the
video.
RPi: After the first controlling
test, the connection problems with the RPi2 aren't over yet. While
the desktop via HDMI keeps running, the sshd and vncserver are far
from reliable. For now I can do "service ssh restart", wait a bit
and go on. A catch is that I have to do this via the desktop. I
want to know if I can do this via serial as well but to do so I
need another Serial Pi Plus and null-modem cable.
Back to the RPi2 controlling the RPi: it would be nice if I can
have 2 controls: 1 letting the binary counter run (pin 12), and 1
to reverse it (RPi2 pin 16 -> RPi pin 37). See the picture.
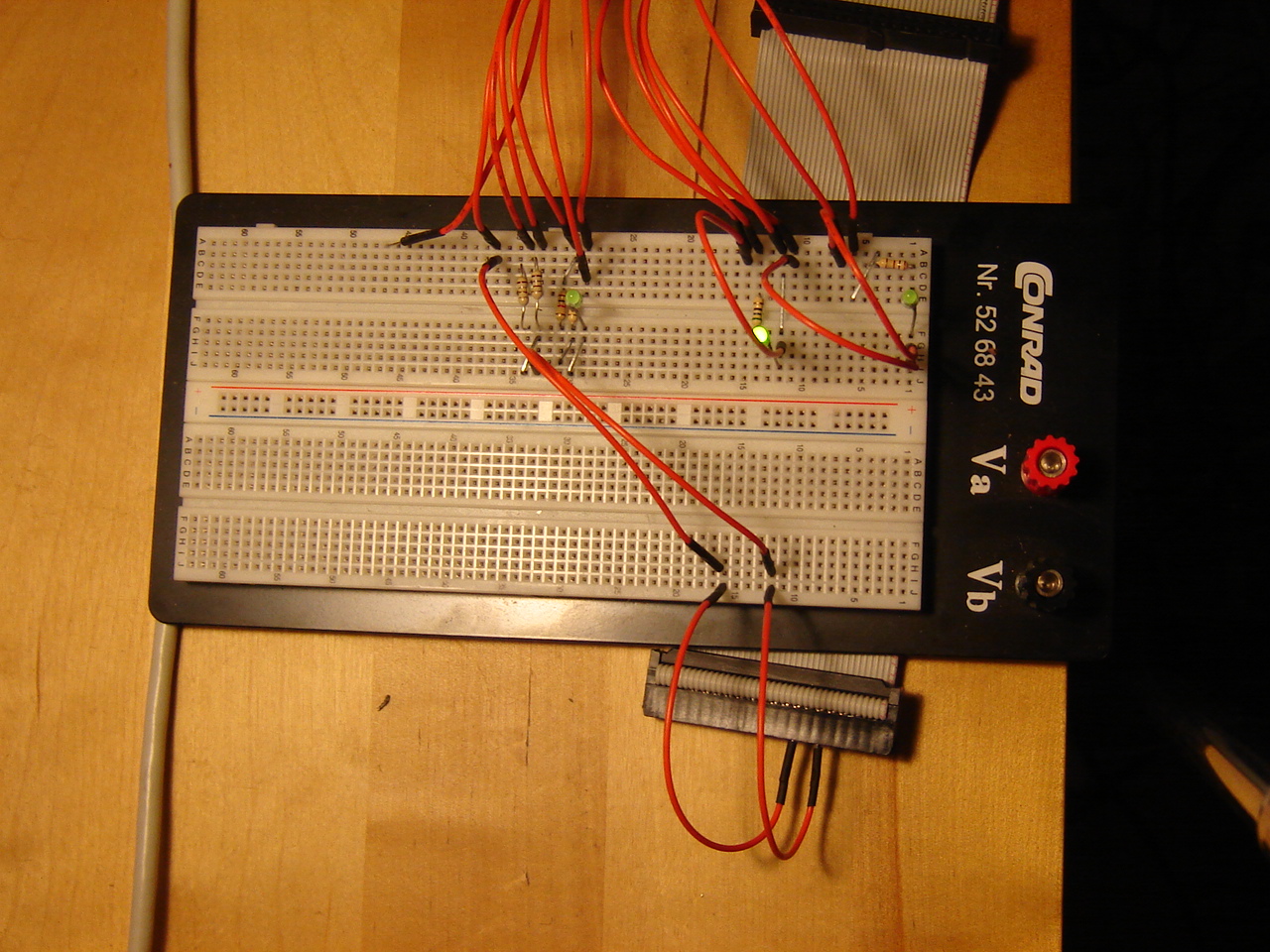
For this to work, I have to extend the counter code for reverse
counting and read/detect the "reverse counting" signal. Although
the code looks good, the result isn't as expected. See the
video.
BB: Continuing with OpenCV: since the recorded image is 8
bits, I have to convert it into 32 bits. However, this turns out
to be more complicated than I first thought: changing instructions
and limitations of instructions cause problems.
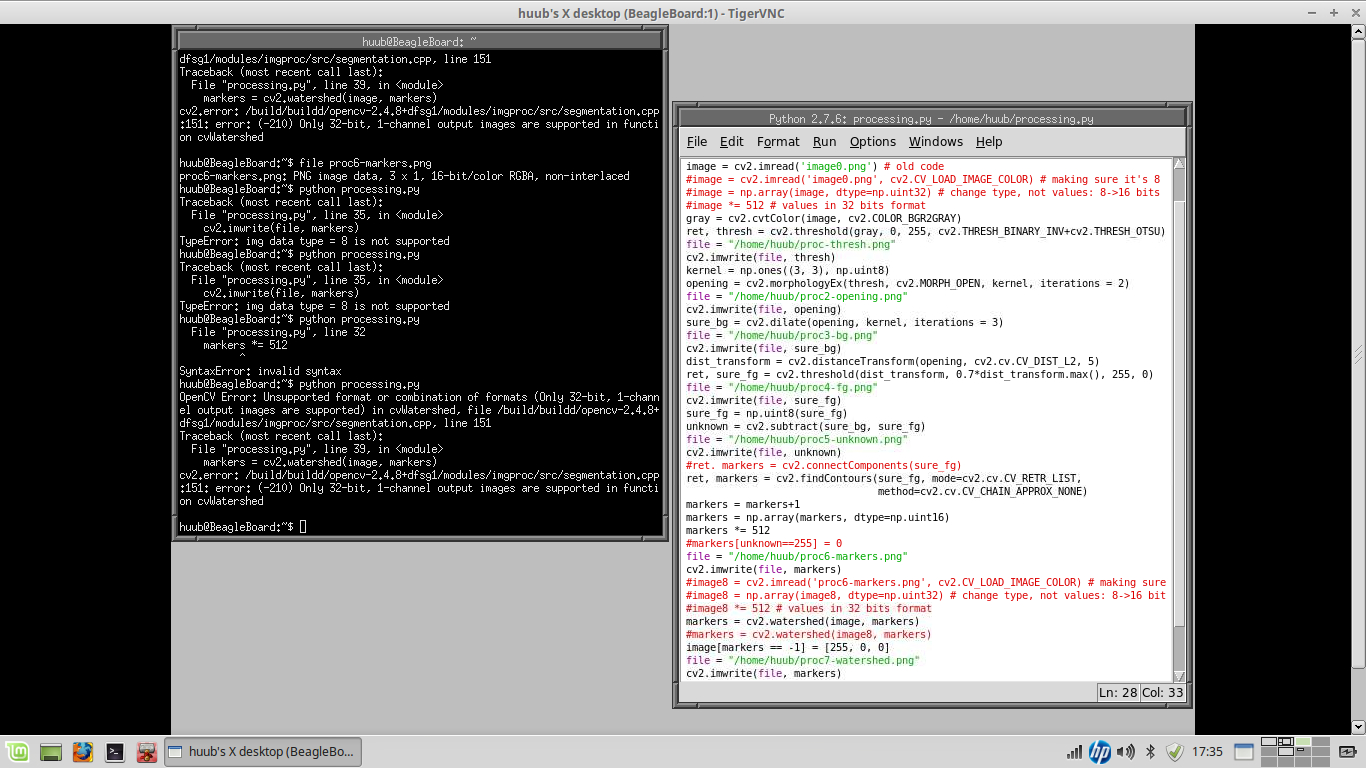
See this screencast
video.
11 December
Discovery: After finding that the code doesn't exactly do
what I want (stopping at meeting an object), I find another
instruction: read out the number of pulses from the motor. With
this, I can have the motor stop prior to reaching the maximum set
distance. See this
video with screencast and a few experiments.
RPi: Continuing with the video
tests, I find that
raspivid -t0 makes that the RPi cam
keeps recording until
ctl-c is pressed. To make things
easier, I put the
raspivid command into a 1-line
executable script using
chmod +x.
On the RPi2 side, it seems to hang again. So I have to find out
why. Simplest solution is cycle power, but obviously that's not
meant to be. But after the power cycle, it hangs again. Time for
more rigorous measures: download a newer image and reinstall. Then
it turns out I have to do an extra action to make use of the full
16 GB: expanding the filesystem. Although that gives me a 24% use,
it unfortunately doesn't stop the "hanging". Which isn't a total
hanging, because the HDMI video obviously doesn't hang at all.
Despite all this, the next step is using the RPi2 to replace the
switch of the 3-bits binary counter and see what happens. See this
video
and this RPi camera
video.
Hand: It's time to extend the software so it can move more
multiple fingers at the same time. Then it's also nice if the
fingers switches are at the same position. So with a slight shift
of the tube connection, the switches look like being in line.
Which doesn't make it much easier to touch 2 at the same time
though. See this
video.
BB: Continuing with OpenCV, I find that OpenCV v3 won't do
the job yet without cross-compiling from source. Since this always
has a chance for dependency-hell, I find that
findContours
can do the job as well, although it needs more parameters: a
mode
and a
method. After some old-fashioned trial-and-error the
correct value for
mode is found:
RETR_LIST becomes
cv2.cv.CV_RETR_LIST and for method.
method is found
in a similar way. With this solved, another problem shows up using
watershed: the number of bits in a picture. See this
video.
Mirft: Time for a chain check: are the 6 vertical chains
equally long? Well, no...see the pictures. It's not hard to
imagine that the legs don't move equally with unequal chains.
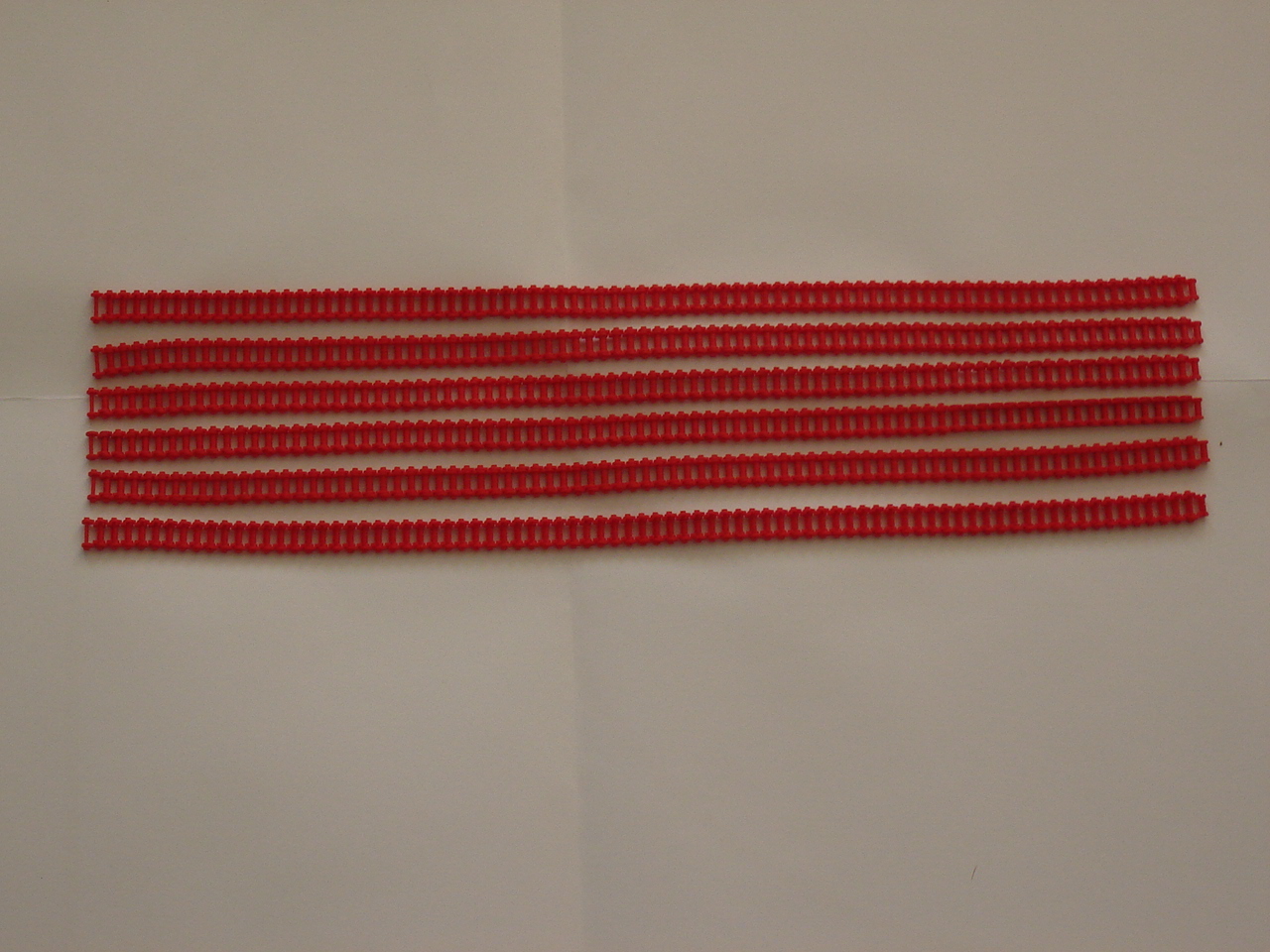
Then looking at the top chains, it reveals that those aren't
equally long either. But aafter equalizing the top chains...there
are some remarkable results:
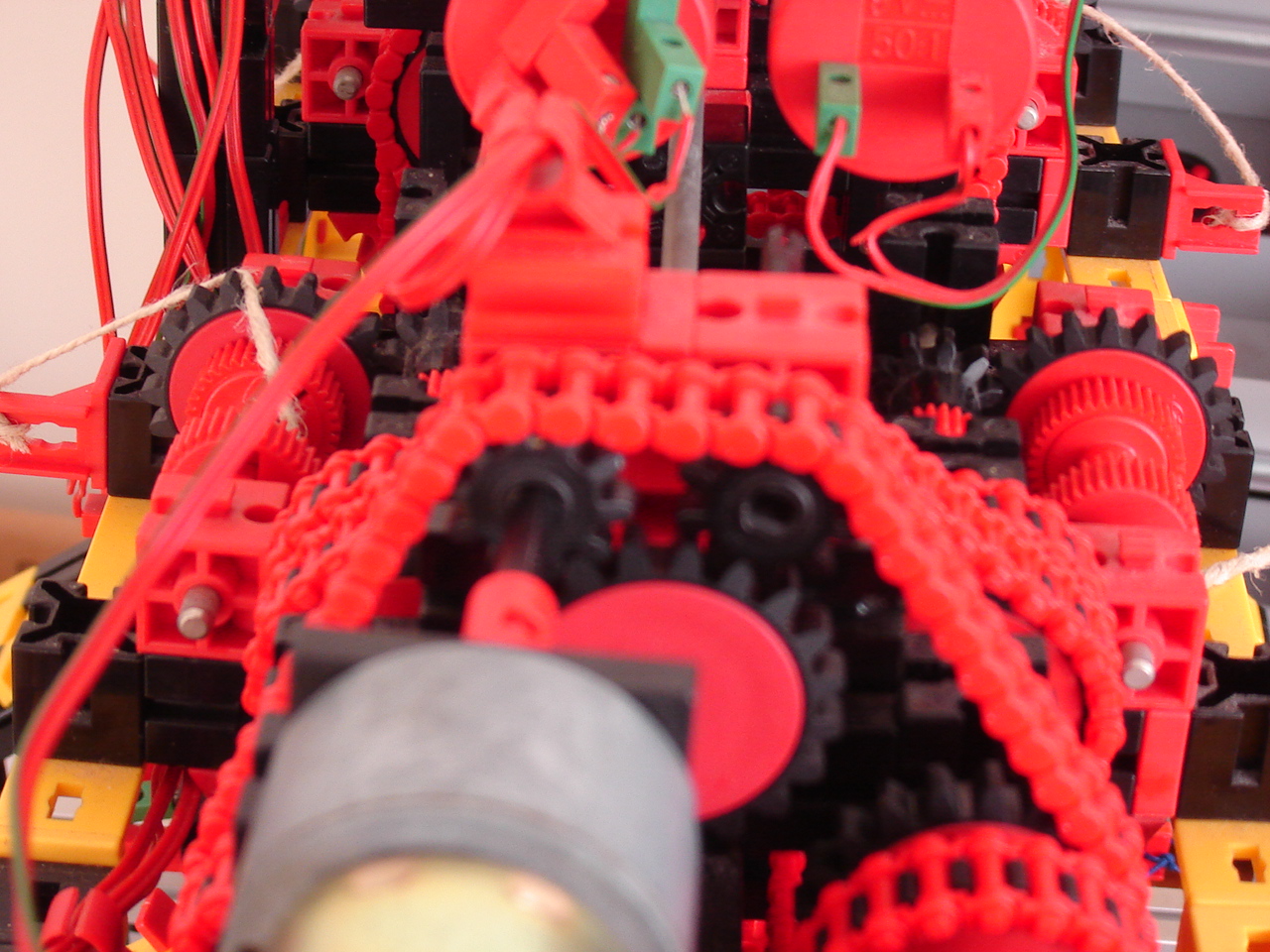
See this
video.
So the end result is that with the chains fixed...the top gears
seem to need some fixing.
4 December
RPi: Continuing with the RPi2, something is strange. Using
the
df -k command to check the used disk space, it shows
89% used with barely anything on it. The RPi only shows 66% used
with quite a few user files on it. And the SD card for the RPi2 is
twice as large. So something is very odd.
To do another "split-screen" camera test, I connect the webcam to
the RPi2, install
guvcview and find that it works fine,
with a catch. After this, it's time for a first test with the
RPi2, the webcam for "splitscreen" and controlling the breadboard.
A combination being more complicated than I thought. See this
video.
Mirft: After the last floor test, it showed that the wide
position of the legs is not a good idea considering the weight of
Mirft. However, a closer look at the angles between upper- and
lower leg shows that there's a flaw in 2 legs: not 2x30 degrees
but 2x15+1x7.5. Ouch. By lack of 30 degree parts, I do with 15
degree parts, making the legs in the same angle, although a bit
longer. Then I try the floor-test again, see this
video. After using the
openshot
editor, the audio turned out to be bad and further attempts didn't
improve it. So in the end, for this video I went back to the
Youtube editor, where I found I can add transitions between
sections as well.
BB: As previously shown, the core of this board can't be
used anymore. Still it's worth to see how OpenCV can deal with
images using Python. But it doesn't go as smooth as expected. As
an experiment, I also try to use
tightvncserver so I can
make screencasts. This turns out to work quite well.
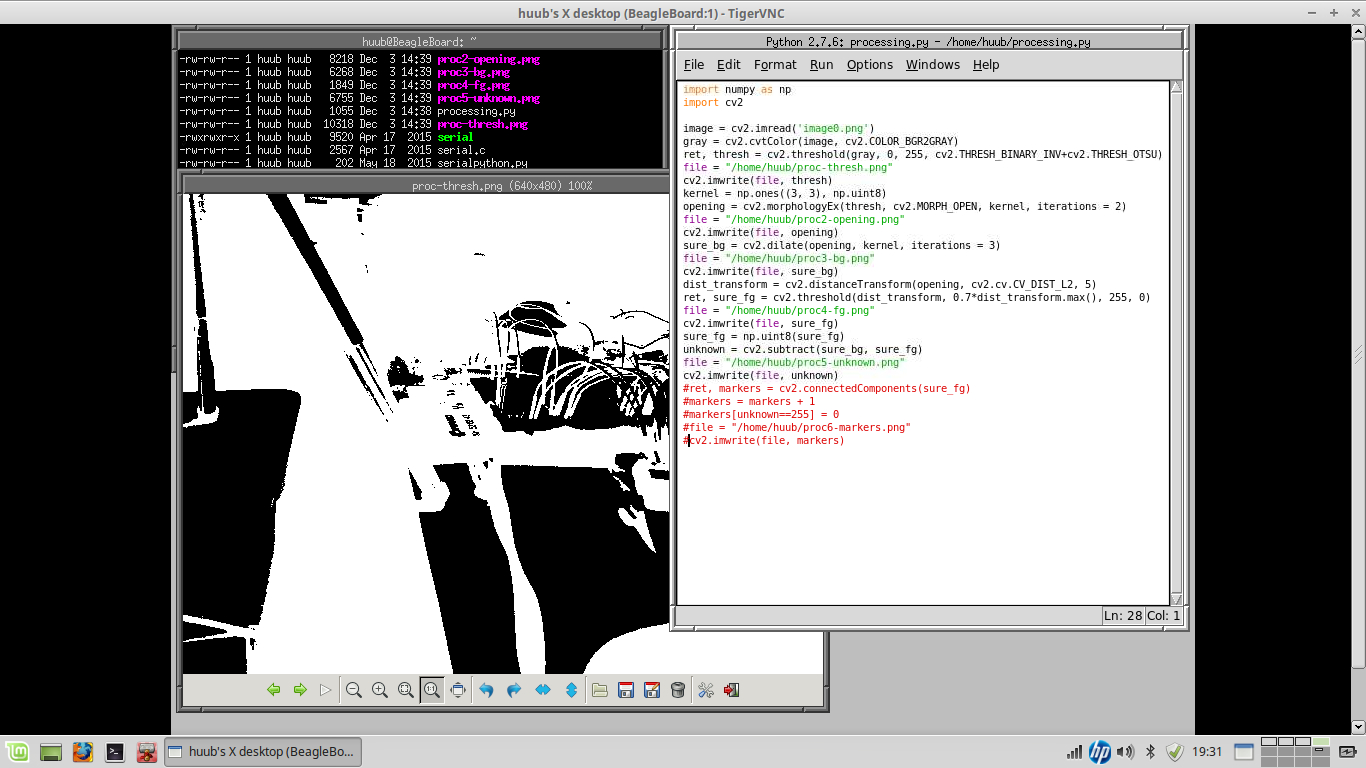
Since this works via the network instead of the HDMI video, I can
use a larger resolution than 800x600. See this
video.
Hand: With the hand having 4 fingers and a thumb, it would
be only logical if it would be possible to activate more fingers
at the same time. For this the code has to be extended, which is
easy enough. What turns out to be not as easy is pressing more
than 1 switch at the exact same time. See this
video.
27 November
RPi:Continuing with the kind-of
split screen, I try the fischertechnik USB camera. See picture.
Again using a resolution of 800x600 and discover 2 facts: 1) the
image frame is much larger 2) there's a delay of at least 1 second
between action and the actual display of the image. This delay
wasn't there with the webcam and smaller image frame. Another test
using 640x480 shows the same frame and delay. So apparently it's
the camera that matters. See this
video.
With the arrival of the RPi2, it's time for another series of
experiments: RPi+RPi2.
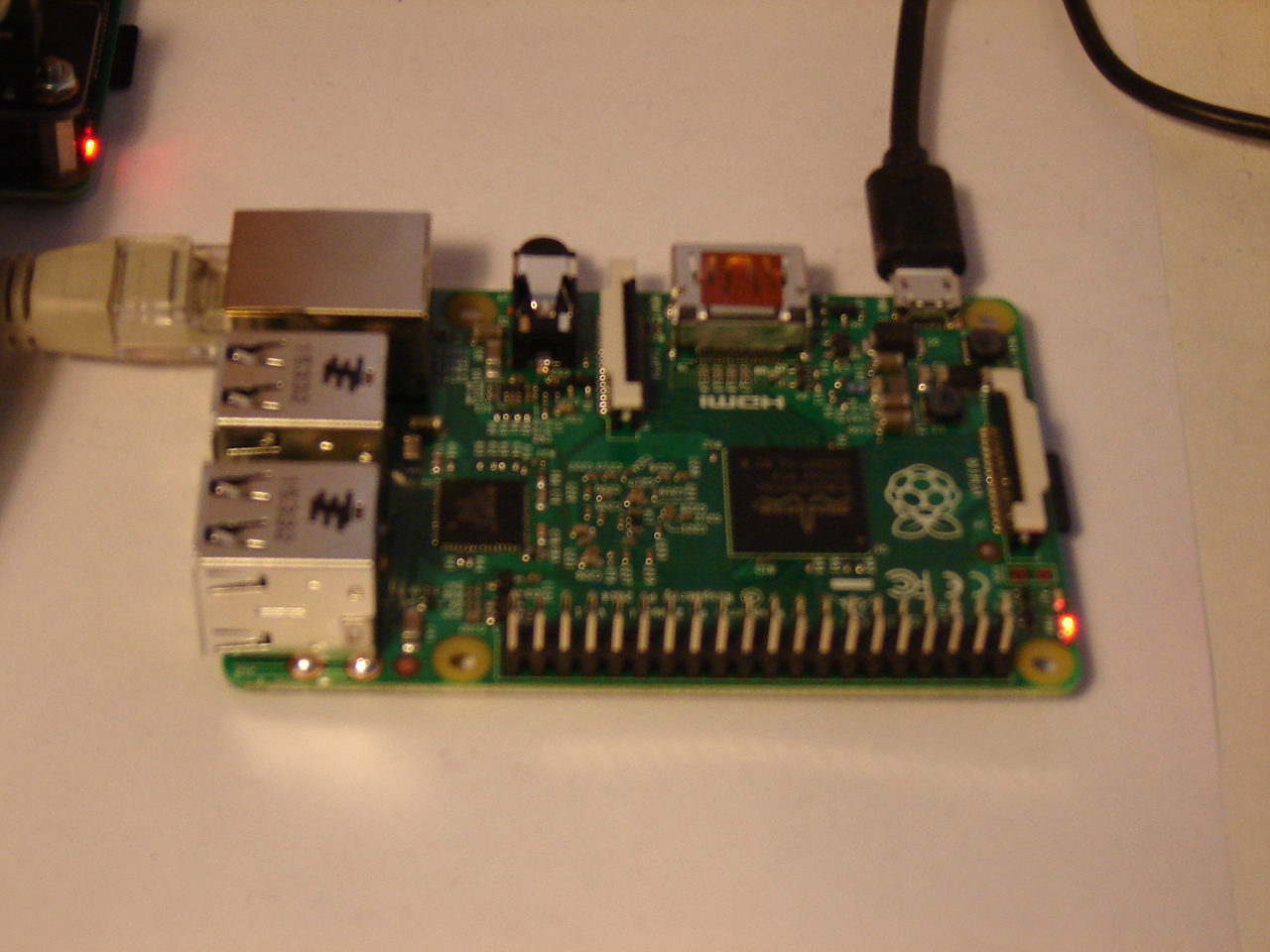
To set it up, I have to completely disconnect the BB, because I
need the HDMI video cable, the mouse and the keyboard. After
installing Raspbian for ARMv7, VNC needs to be installed. After
this, the setup will be more or less the same as with the RPi. For
now it will lack the SerialPi board and RPi camera.
Setting up the RPi2 gave a nice quick experience although not
everything was the way I expected. See this
video.
Then another nasty surprise: after reboot, I fail to login via
keyboard. After using the router to determine the RPi2 IP address,
I decide to use ssh and find I can login. So the password does
work after all. Then starting
vncserver again, and I can
do whatever I like, until
vncserver quits. Having the
ssh
terminal open, I can easily restart it but it's obvious that this
isn't the way it's supposed to go. Another effect I notice, is
that
vncserver starts again.
After all this, I disconnect the complete USB keyboard/mouse/WLAN
stuff and HDMI cable: they go back to the BB.
Mirft: It's time to modify the last 2 legs into stable ones
and test again. What it turns out that some of the gears on the
chain axis are a bit loose and the gears that hold 1 of the chains
are moving freely. Oops. After fixing this, the chains and gears
problems seems to be solved, but the floor-test reveals yet
another problem. See this
video or this
video (an offline
created "director's cut" version).
Hand:After repositioning the fingers into 4 fingers and 1
thumb as in a real hand, I need to reposition the 3 existing
valves as well so I can add the 2 new ones. This brings a spatial
problem which is solved by elevating the compression chamber. See
the pictures and this
video.
BB: So far, I've used the BB for some image and video
capture experiments in combination with Python. This delivers
avi
videos that look like 6x speed up.
There are several disadvantages of this BB version (Classic
Revision C4). The maximum display resolution over the HDMI port is
800x600. Also the 250MB RAM is a serious limitation, as well as
the 16 GB SDHC memorycard as "harddisk". To save memory, I use the
fvwm2 desktop which
works fine. However, it looks like it's current use is coming to
an end as there are signature verification errors during updating
the operating system: Ubuntu 14.04 LTS
armhf.
The only other use of this board would be for the
Digital Signal Processor to process images.
But that requires the seriously outdated 2.6 Linux kernel and an
equally seriously obsolete DSP driver set. Hence, out of the
question.
Software: I've started to publish my source code, not on
Github but here on my website. Because of the quantity of my
projects Github is too much work.
20 November
Mirft: Focussing on chains, I corrected 1 chain by taking 2 links
out of it (see picture) and found that another suspected chain is
actually of the correct length.
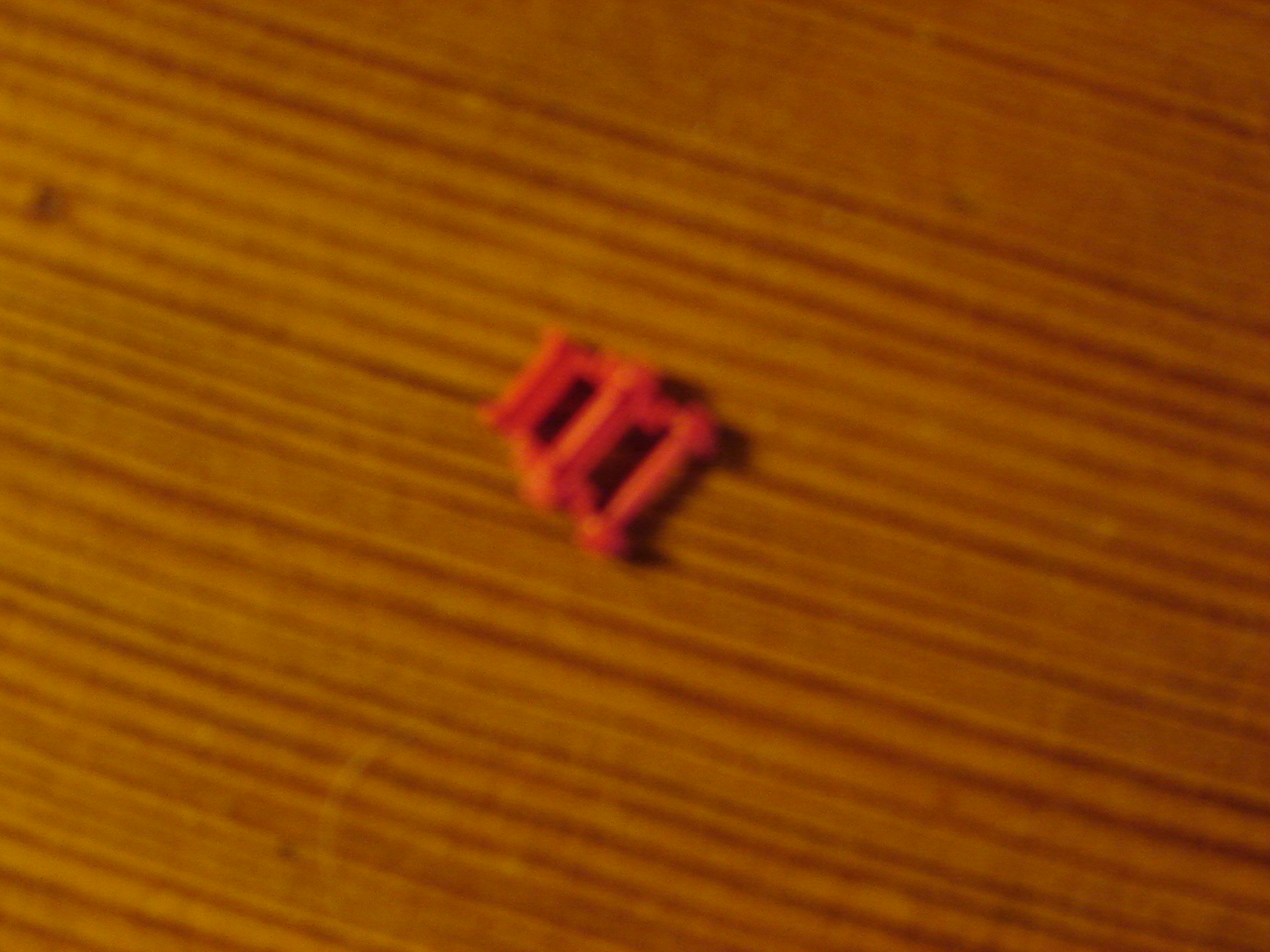
First it shows that the support of the gearing is pressed down,
but after correcting this slipping still happens. So more to be
investigated. See this
video.
Discovery: To test if the touch and sonar works better via
RoboPro, I wrote a similar program, see the screenshot/picture.
Running this, didn't completely go as expected. See the
video.
However, it leaves enough to experiment with further. See also the
picture with "Online" display while running Python.
I planned to see if this works better with C, but the power-off
problem (again!) as shown in the video as well as the sudden
disappearance of a loaded program from RAM (again!) has led to
contacting and sending it to fischertechnik for diagnosis and
hopefully either repair or replacement. Yuck.
Mydfir: The colour sensor so far has been attached to input
A1. So what would happen if it was attached to input A2 ?
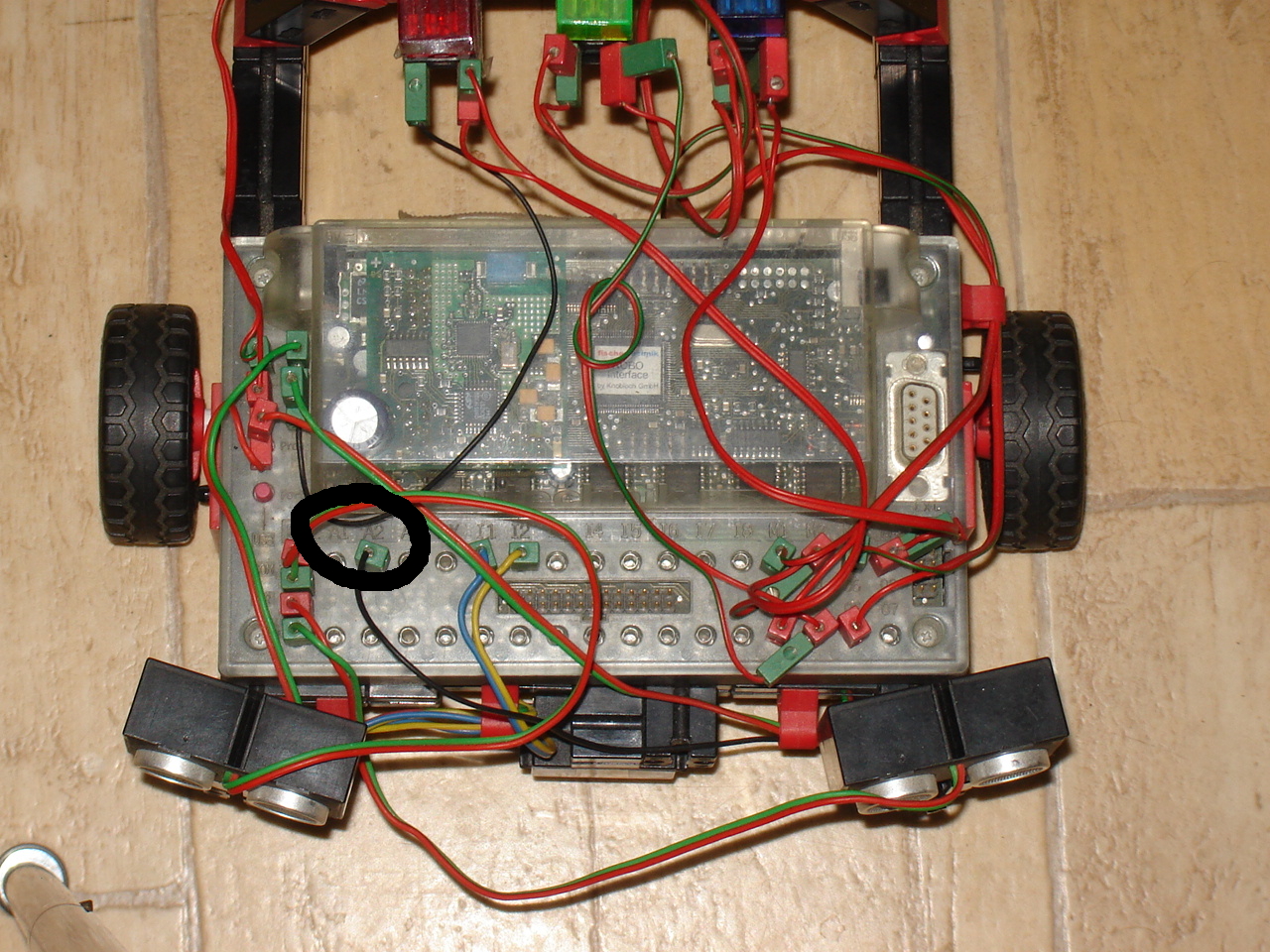
After quite some testing, it looks promising but only for this
setting of light. See this
video.
RPi: It would be nice to make a
kind of split-screen screencast using video via the RPi. In my
setup using VNC, the RPi cam is no option. So I try it by
connecting the webcam to the USB and
guvcview. Although as
the picture shows, the webcam is obviously active (blue ring), the
onscreen image from
guvcview is black. Another solution is
of course using OpenCV as I do on the BB. What I find then, is
that the video window is very small. See the
video.
13 November
Mydfir: The riding robot is always a huge success on
conventions. However, of the 3 sensors (sonar, line tracking and
colour), the colour sensor seems to give wrong output (if any at
all). After some testing, it turns out that the sensor does work,
it just seems to be calibrated totally off. See
this and
this
video for an attempt to calibration. Since these attempts are all
with the same light source and brightness (cloudy daylight) and I
don't have another colour sensor to compare with, there's more
testing needed. So to be continued.
Mirft: Although the replacement of the bottom winches by
clips worked, a problem turns out to be the chains: on some places
they slip because they're apparently too long. Result is that the
robot ends up on the floor after all. See this
video
for the experiments...
Hand: To make more clearly which switch activates which
finger, I relocated the switches to the fingers. This took some
experimenting. See this
video. The compressor has a gear problem,
but not sure how to solve it.
Discovery: More testing on the response from the sensors:
is there are difference between 20 cm from the computer and 2 m
away ? Because earlier tests showed that it didn't respond or very
late to sensor input. As this
screencast shows, it's
still inconclusive. And the frequent returning all-zero response
is also weird. The picture shows the Discovery motionless on the
floor connected by the powercable: it's supported by a batterypack
to keep the wheels off the floor.
RPi: Continuing with the 3-bits
binary counter in C++, I change the inputstate check into 0. After
this, the LEDs do something but it doesn't look like counting.
Also, still nothing happens when I press the switch. But since the
Python code does work, the suspicion comes that I may be playing
with wrong GPIO port: 13 may not be 13. After a thorough check on
the code that switches the LEDs, I find some errors: at some
points the wrong LED is manipulated. I also change the switch time
from 0.5 second to 2 seconds. After these corrections, I decide to
run with inputstate still 0: the counter now works, but is not
interactive. See this
screencast.
BB: I wanted to do a C++ test with OpenCV, to see if I
could get a better webcam result than with Python. However, with
extremely little space left on the SD card, this is no option. So
I may have to go for a 32 GB card, which the largest the BB can
take.
6 November
Videos: Since all videos are available via Youtube, I
removed all individual links and put links to playlists instead.
Discovery: After finding out that the TXT controller needs
a minimum of 6V to run, I decide to test this: at 6.35V it's over.
The next test is to see how long it takes for a full battery pack
of 9.4V to unload: without the 2 motors running, it takes about 10
seconds per 0.01V. With the motors running, it takes some 4
seconds per 0.01V. So with 3000mV to unload and 4 seconds per 10mV
= 4 x 300 = 1200 seconds = 20 minutes.
Next is of course the presence of the touch sensors (switches).
With the sonar up front they're no use there.
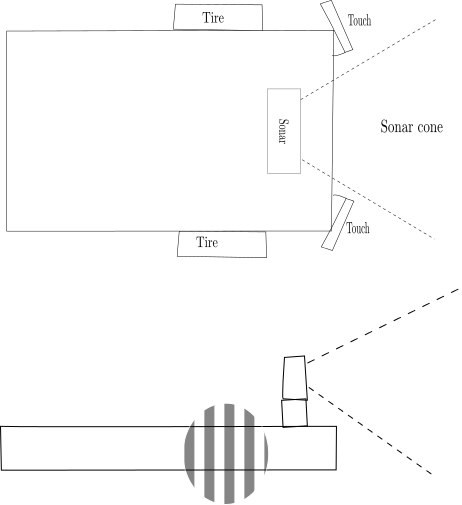
The above sketch shows the 3D sonar cone (of which in the sketch
is assumed it has an outer bound of 30 degrees) with the touch
sensors. However, some testing shows that the outer bound is
merely 20 degrees. With such a smaller cone, the touch sensors can
be used when they're relocated to the corners. So make this
possible, I adapted/extended the frame of the Discovery. See
picture 1. Testing shows that the sonar doesn't recognize any
object placed on the riding surface. Lowering the sonar as shown
in picture 2, shows no improvement on recognizing objects. See
this
video.
1:
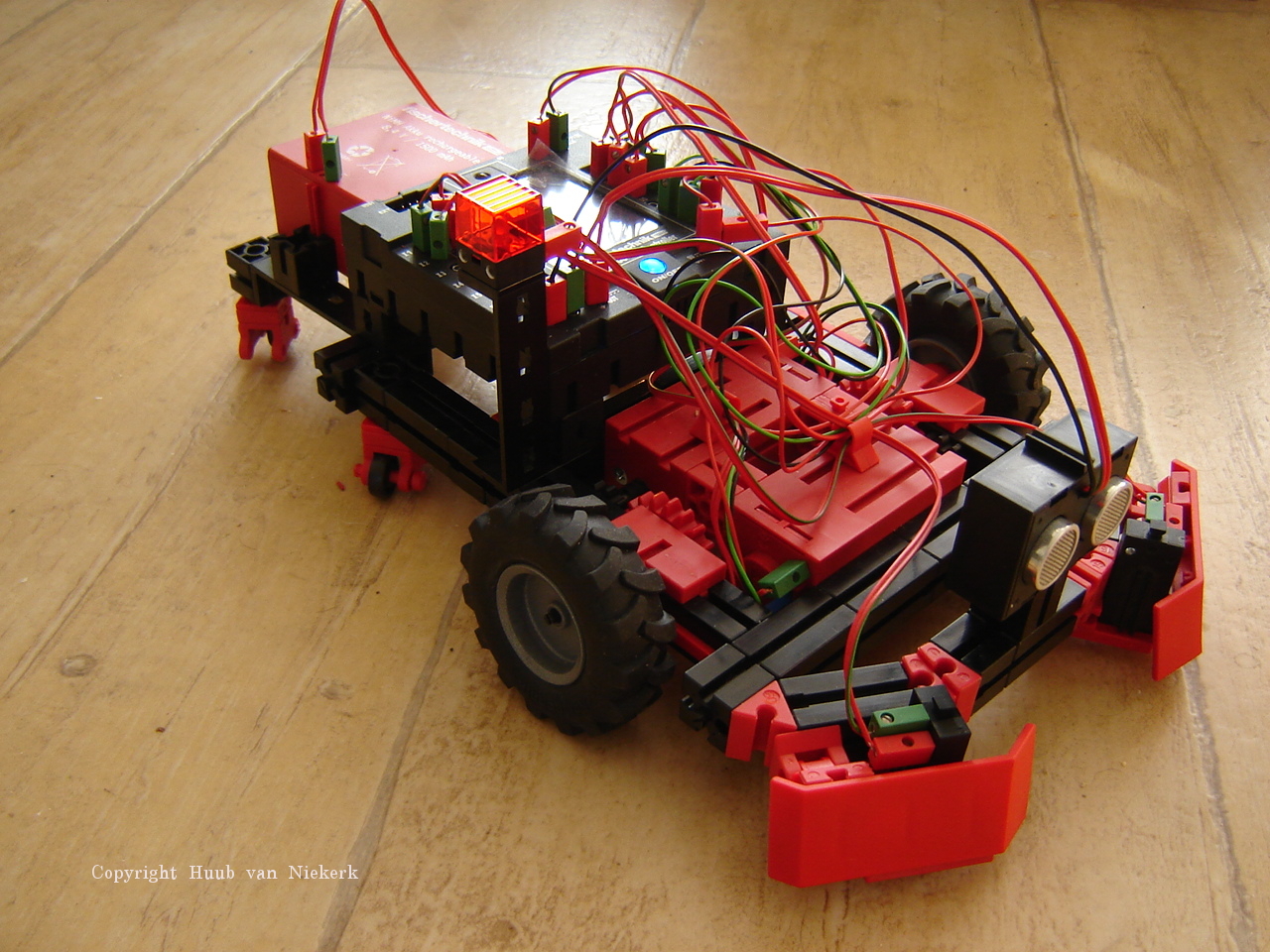
2:
RPi: I continue my C++
experiments. After some minor changes, the code shows no positive
results anymore, so I fall back to giving commands straight in the
terminal. To my surprise
echo "4" > /sys/class/gpio/export
gives the error
echo: write error: Device or resource busy.
This means that my code does not unexport properly. This is proven
when I do
echo "4" > /sys/class/gpio/unexport and again
echo "4" > /sys/class/gpio/export. This time there is no
error, so it's necessary to review the code. It turns out there's
a typo in the function sourcecode. But fixing this, doesn't solve
the lack of positive results. Running the same algorithm in Python
shows again that both the algorithm and the hardware simply work.
See this screencast
video.
Mirft: A continuing problem are the slipping winches and
picture 1 shows a solution. However, with the use of this
solution, the connection with the bottom side of the leg fails
because of the direction. This is solved by reconstructing the
leg, as shown in pictures 2 and 3. This
video
shows that it just might work.
1:
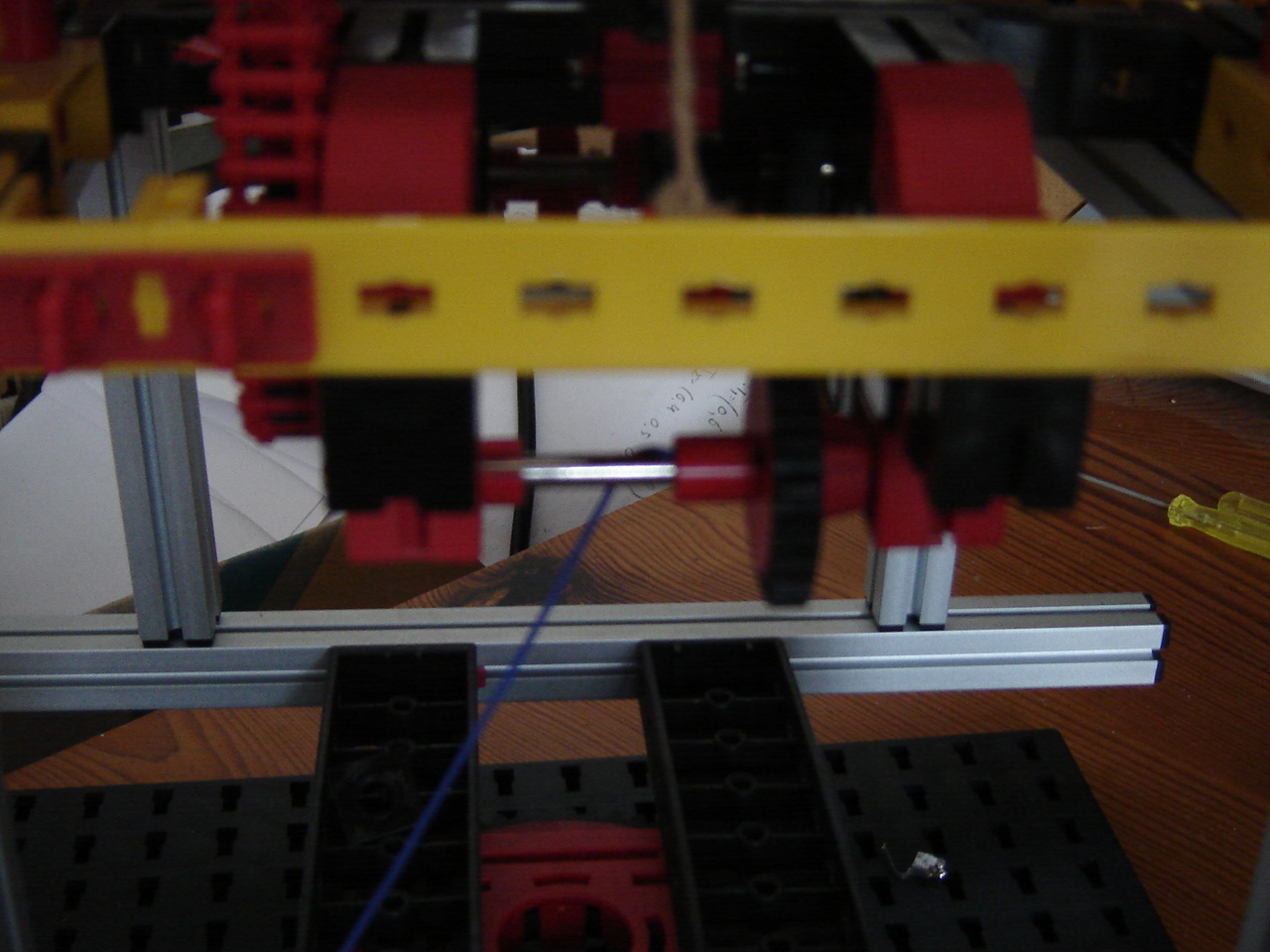
2:
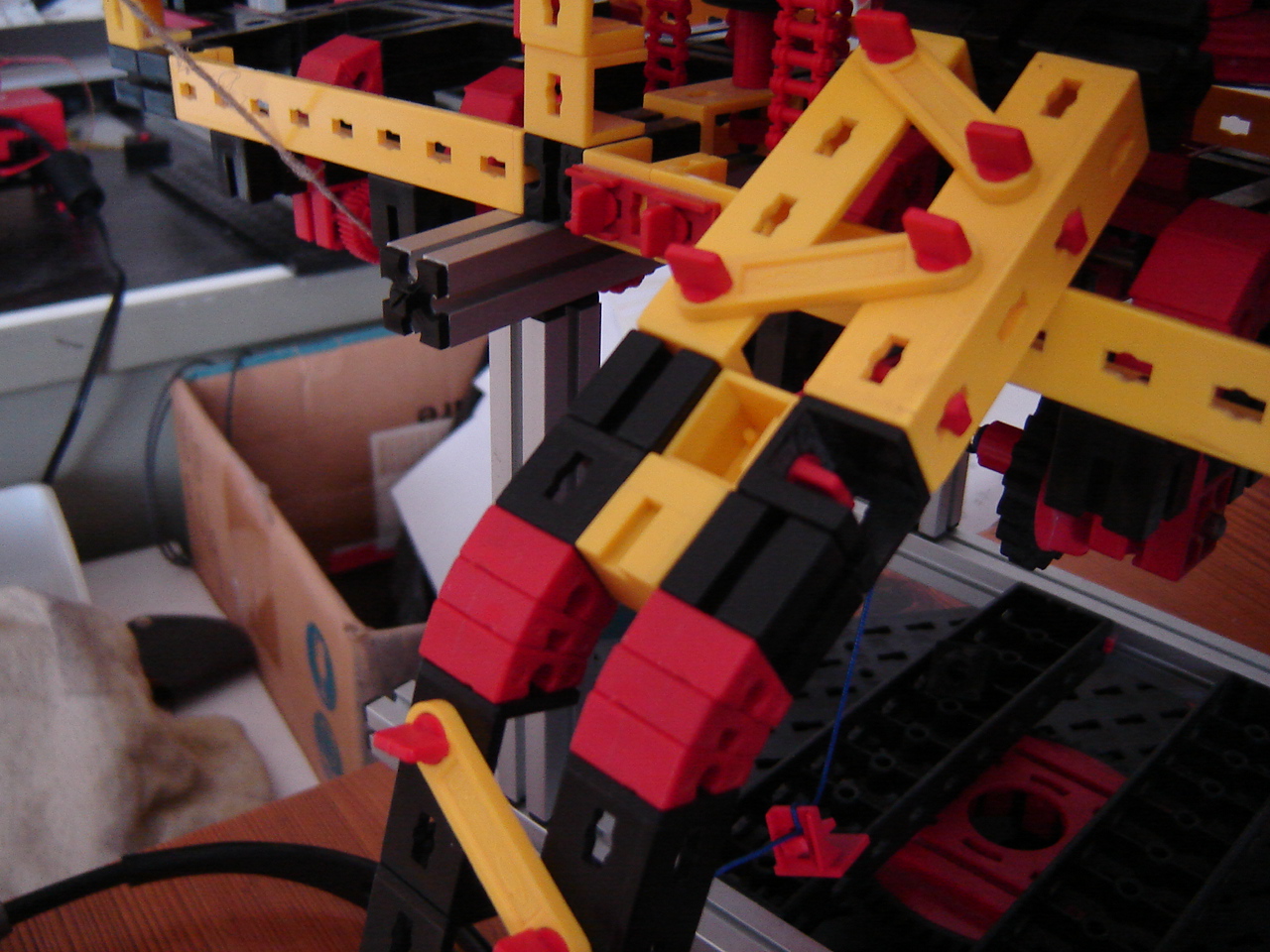
3:
Hand: To make the hand a bit more realistic, I relocated
the last added finger so now it has 3 fingers and a thumb. See the
picture and this
video.
30 October
RPi: As a challenge, I ported (i.e. translated) last week's
interactive binary counter from Python into C++. To do this, I
used
this as an example. It shows a distinct
difference: instead of using the pin numbering, the GPIO numbers
are used: e.g. GPIO pin 7 is GPIO4. So this has to be changed in
the code. Another issue is that in C++ a lot has to be defined
first, so you create a header file and a source code file (or 2 or
more). Compiling at first led to errors about the
main
function not found, but combined compilation
g++ CPIOClass.cpp
CPIOtest.cpp - o CPIOtest makes everything being compiled
fine. Then, when running it, it reads the switch signal fine, then
not, then again, then not. Ugh. So why does the Python code work
fine and why does the C++ code work intermittently? See the
screencast
video.
Discovery: I added a sonar to the TXT controller and
thought I'd add the distance condition to the
while. Since
a logical
OR either true or false, the condition becomes
(left
touch
or right touch or (distance < 5)) == 0. So I'm measuring
the distance up to 5 cm. With this done and working (see the
video), I decided to extend the wheelbase to make changing the
battery pack easier. Also, I added a light as battery pack
indicator just like I have on Mydfir, the other driving robot. See
the pictures.
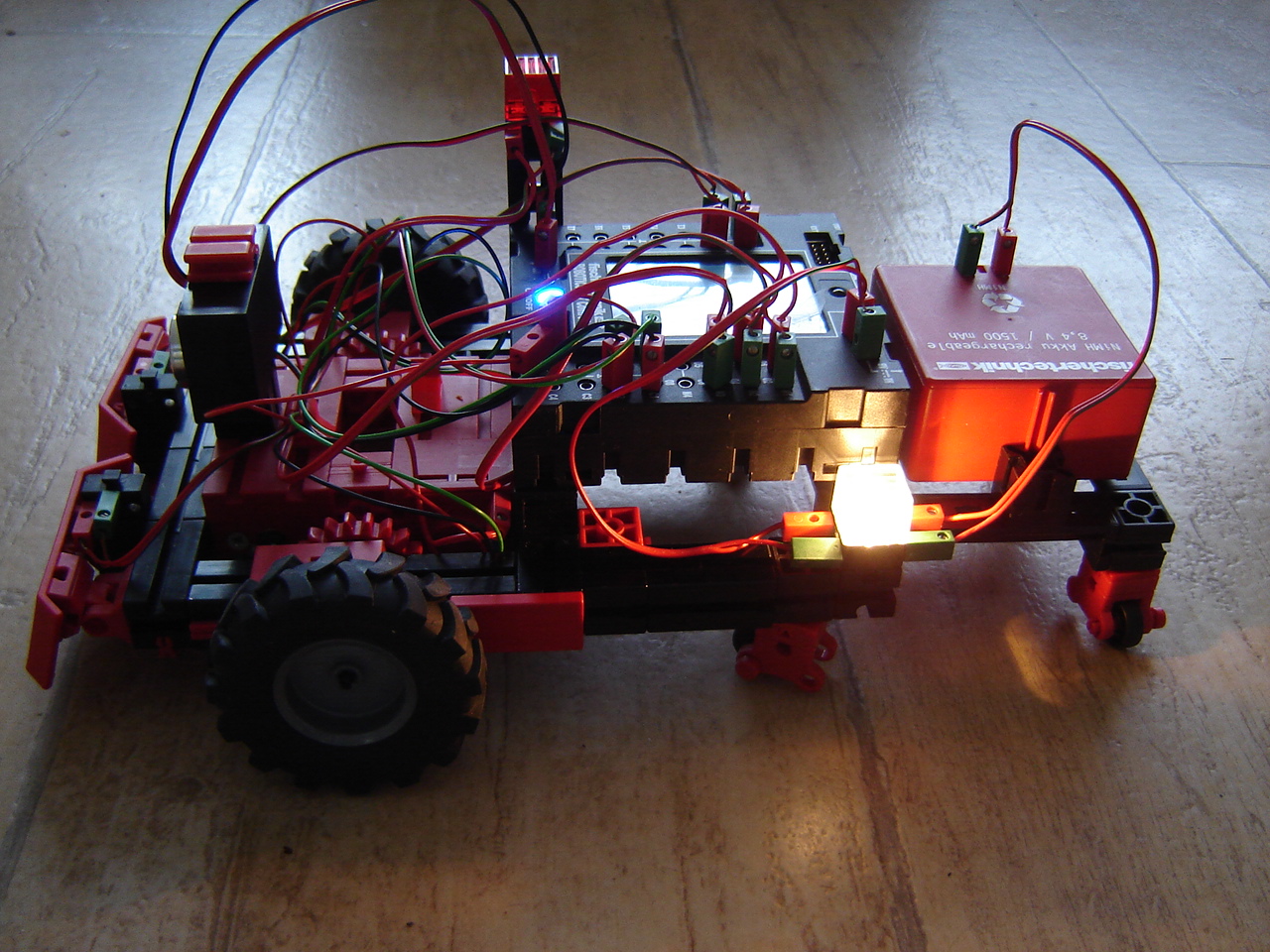
So for now, the Discovery has both tactile and sonar sensors as
can be seen in this
video, which shows that it doesn't always
work as it is supposed to. Some remarks on the video:
- What I don't show in the video is that frequently the program
just returns 0 for some reason. This is why the robot stands still
for a while before it finally starts to run.
- The demo is recorded at 2 different times of day, hence the
difference in lighting.
Hand: Since the hand is not really a hand yet, I built an
arm to which the hand should be attached. This creates also the
possibility to modify the hand so it's more like a biological
hand: 1 finger/thumb across 3 fingers.
Mirft: After replacing 1 pair of hinges, the other 2 pairs
needed replacement too together with broadening as many legs as
possible, given the availability of parts. Along the way I found
an existing construction mistake in the rear hip that had to be
corrected. After switching 2 legs for the repeat of the floor
experiment, it shows that the lower winches are a bottleneck. See
the
video.
23 October
Screencasts: In order to show the source code of my software
better on video, I installed
SimpleScreenRecorder. However, on the main
laptop this couldn't be installed due to the fact that there was
no package for Fedora 21 and I was unable to get it compiled.
After checking out which distibution could replace Fedora
(Fedora 22 and any Ubuntu didn't boot my laptop), the choice was
Linux Mint 17.2 which booted straight away and is a LTS release
based on Ubuntu Trusty. So for some time to come I'm safe.
Discovery: It turns out that the
logical or
(actually:
inclusive or as opposed to
exclusive or) works different in
Python than I earlier understood. To get
inclusive or you
need to put both conditionals between brackets and put the
comparison outside:
(x1 or x2) == 0. See this
video.
Hand: Replacing the duct-tape with a t-piece turns out to
be a good idea. However, it still takes some time to compress
enough air to let fingers 3 and 4 work fine. See the picture and
this
video.
RPi: A 3-bits binary counter is
nicer when it's interactive. So I added a switch according to
schema 2 of this
info using other pins. Important with the
RPi is to use resistors, like I've shown in earlier schemas.
The algorithm in Python results in a continuous binary counter as
shown in this picture and this
video
and HD
video
(with RPi camera).
Arduino: After reinstalling the laptop, I took a new look
at the software for an attempt to get the e-brace working. It
appeared that, for some reason, the main directory had the wrong
name which only was wrong in detail:
Main-program instead
of
Main_program. This problem appears when I try to
compile the program. After changing it, it compiles fine.
However, the movement program doesn't compile because of the
errors
'MOVEMENT_OUT' was not declared in this scope and
the same for
ACC_CS. Then, trying the light program shows
a similar problem:
'LED_x' was not declared in this scope,
where x= R, G, B. Finally, the sound program gives
'SOUND_OUT'
was not declared in this scope and the same for
MIC_IN.
So probably I'm missing something although I didn't change the
software except for 1 correction (Gadget.h -> gadget.h) that
made the main program compile and upload fine.
After downloading the software again from the original
source,
all problems but one are there. So I wonder how this ever worked
in the first place. See this
video.
16 October
Discovery: Using the algorithm from last week, I
added 2 mini-switches with boards to the robot to detect obstacles
and put the code into a
while loop so it stops when some
obstacle is hit. And as you can see in this
video,
the experiment is not going entirely as intended.
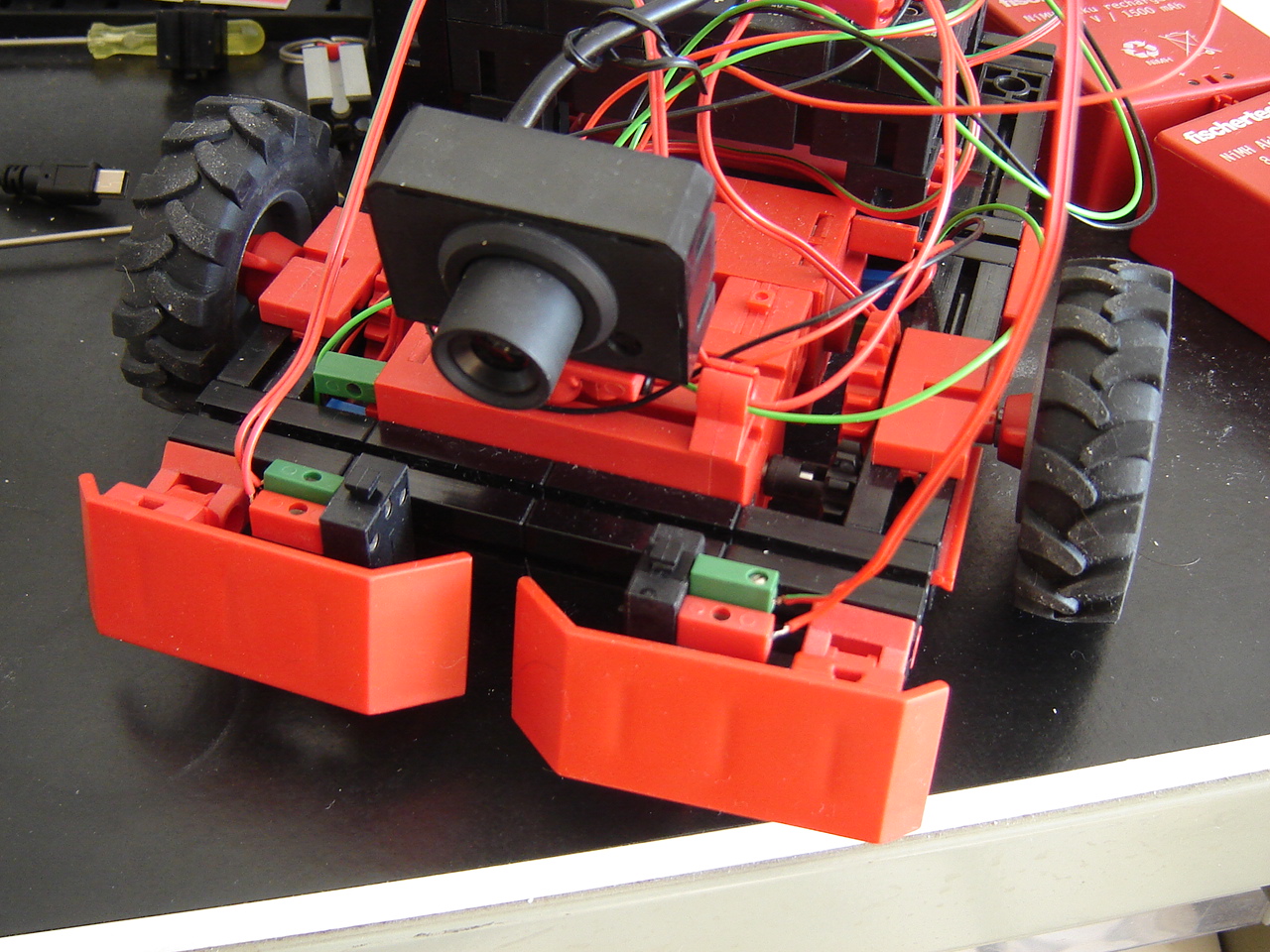
Arduino: Another attempt on programming the
e-brace. After re-reading the manual and information the Arduino
tutorialpage, I find that information on the
e-brace is very scarce. So it is still not certain that the code I
wrote works or not as shown in this
video.
Mirft: A walking robot should be able to stand on
its feet. A simple test shows that there are multiple problems
with this idea when it comes to Mirft.
1: As expected the legs are too week: there is torsion when
pressure is put on them. This can be solved by either replacing
them with aluminum or reinforcing them. Another part of the
solution is to replace the hip hinges as shown in these pictures.
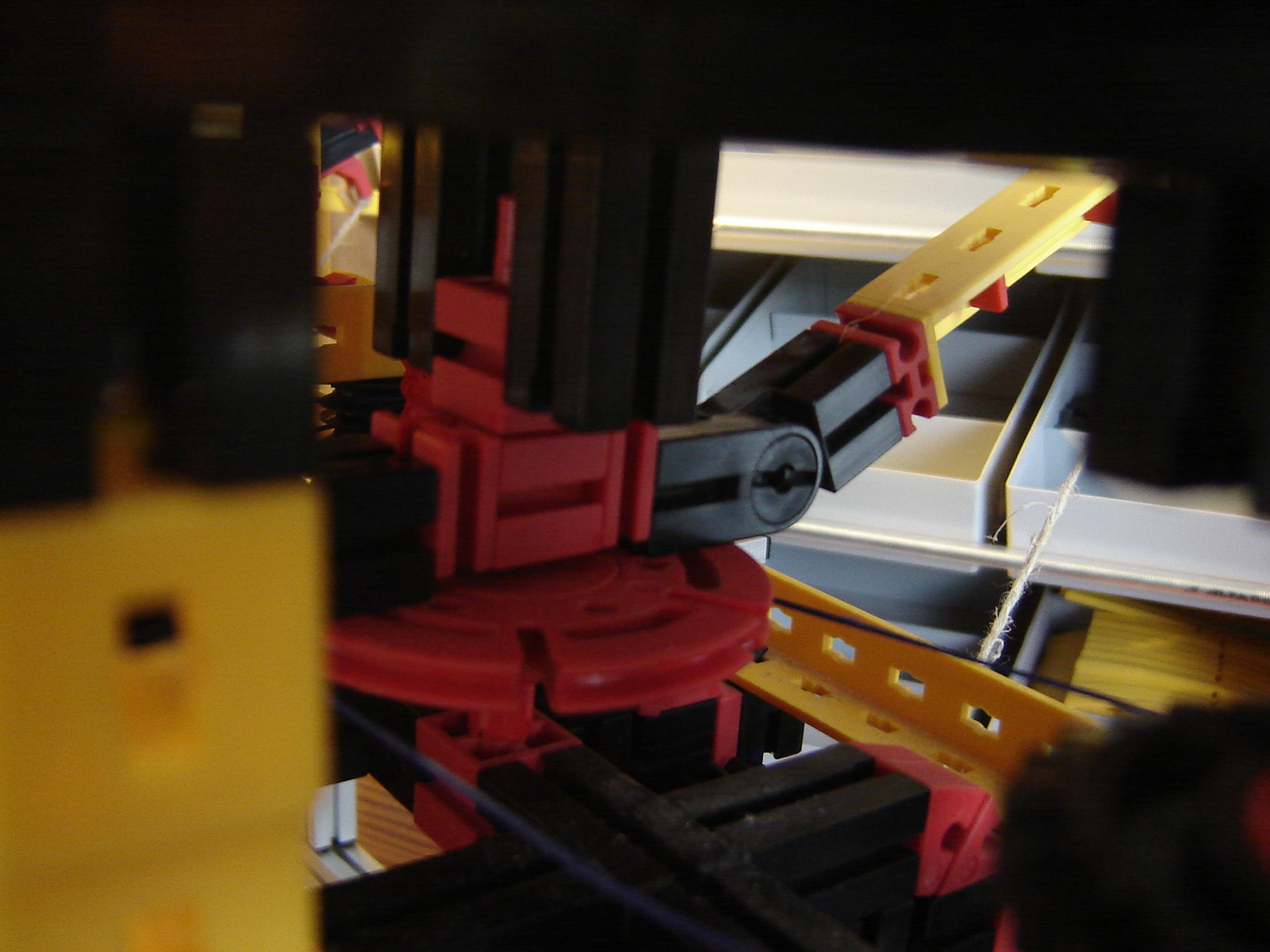
Another stabilization improvement would be to broaden a leg, as
shown in these pictures.
2: Also as expected, the current strings are made of rope and
should maybe replaced by stronger material such as nylon.
3: Not as obvious is the slipping of the vertical winches.
As this
video
shows, putting the weight of the robot on the legs, isn't working
good enough yet.
RPi: After the walking LEDs, I decided to make a
binary counter. Using 3 LEDs, it counts to
binary 111 or decimal 7 as shown in this
video.
Using the RPi camera, it shows the counter as well, but since the
video
is made from the RPi side, the Most Significant Bit is on the
righthand side. Technically, both are valid and their use depend
on the convention you use.
9 October
Videos: I created 3 more compilation videos. This time from
the TeamBuildingDay in 2008:
first,
second,
and
third
challenge.
Discovery: Although the controller is running Linux, I find
that e.g. the
vi editor is not fully implemented:
the
u command (undo last action)
is missing. Apart from that
this,
this and
this
video show some real and continuing experiments with Python. Check
pwm for the use of the light.
Arduino: As an intermezzo, I went back to the Arduino
e-brace I last tried around 30 July and made a
first
and
second
video of a live-experiment with programming with C.
Mirft: When trying to solve the problem of horizontal
movement boundary, an idea would be to use a lense-lamp
vertically. This brings another problem: where to put it so it
doesn't interfere with the string and leg. So in these sketches 2
options are shown. Neither is really good because option 1
interferes with the leg in top position and option 2 with the
string.
1:
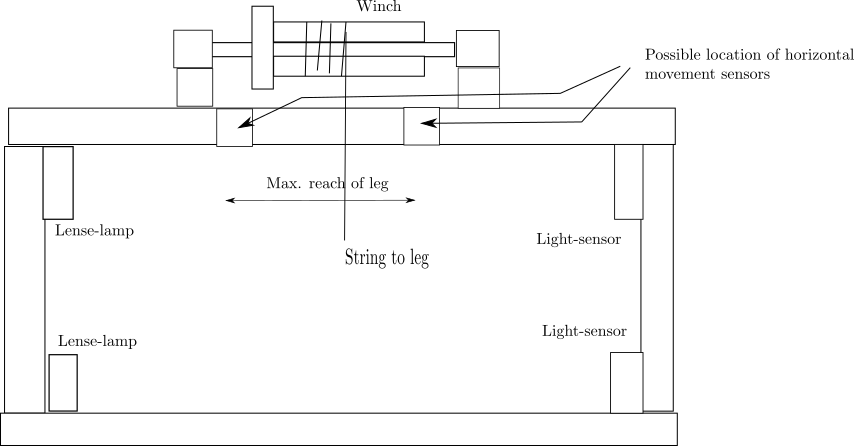
2:
2 October
Videos: I created some compilation videos which can be found
in the playlists on Youtube.
Mirft: At the ft convention in Dreieich, someone gave me a
sonar sensor which is suitable for the ft RoboInterface. I put it
at the front of the robot and connected it to the D2 input of the
controller.
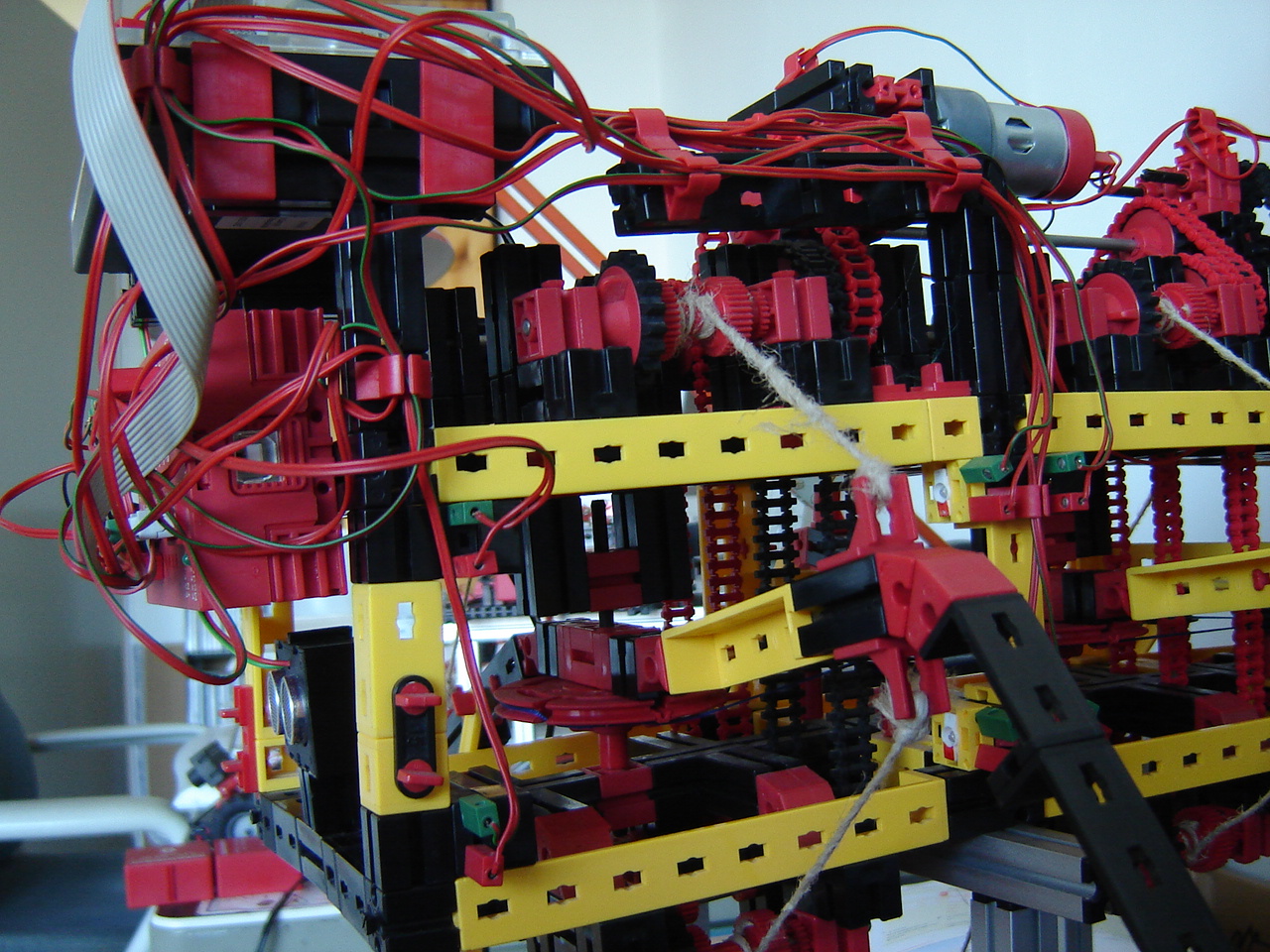
A quick test using the Diagnose software reveals it's working nice
and obviously it will function as an object detector. In my own
software, I will have to enable the sonar by using
bEnableDist=1,
the same way I did for the riding robot. The main code starts now
with
while t.GetD2 > 10 so the object has to be
further away than 10 cm for the robot to keep moving. See also
this
video.
Discovery: After trying to get things working via ROBOPro,
it's time to get back to Linux and make a start with Python: the
ftrobopy library and the Python_for_TXT library which were made
available in this
community thread. After following the
instructions, it shows that the first example works nicely, as
show in this
video.
25 September
Hand: Recently I decided to use the 4th cylinder and connect
it to the same valve as is used for the 3rd. However, because I
lack a 4th t-piece to connect the air-tubes, I tried to use
ordinary adhesive tape to couple them. For a short while it
worked. Time for another solution: using duct-tape
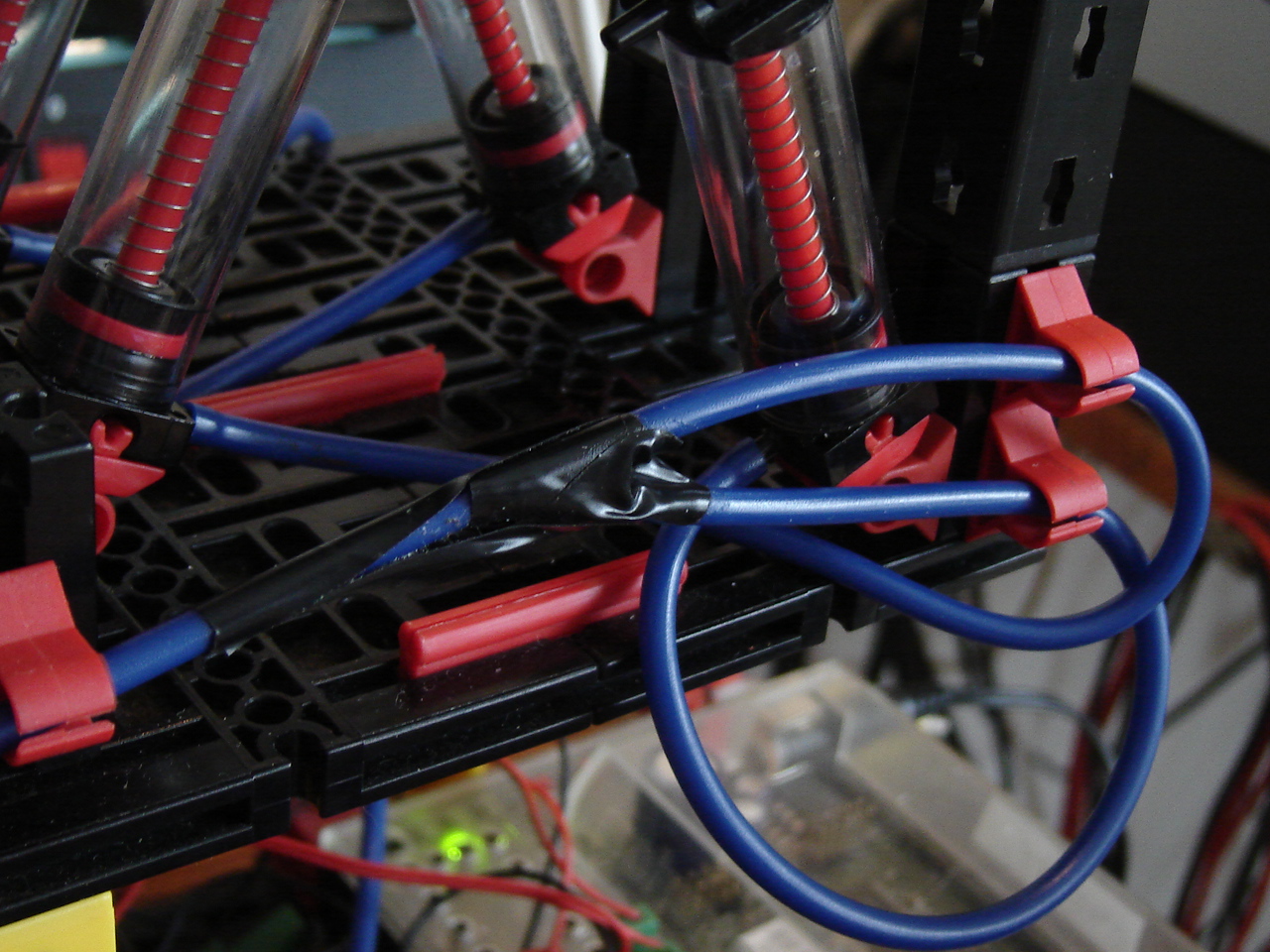
as also shown in this
video.
18 September
BB: After using the BB in combination with the webcam a
couple of times, I realized I had not demonstrated how that
actually works. So I made this
video.
Mirft: I noticed that the 3D model created with Blender was
not up-to-date anymore, so I added the 3rd motor.
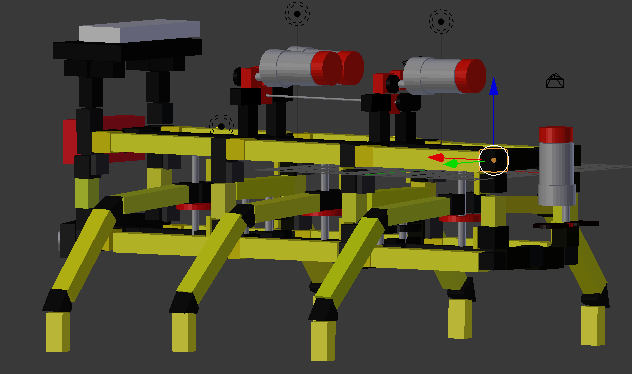
Then, for the real "thing", a way to fix the connection of the
horizontal string to the hop wheel is using a
clove
hitch on a spring cam as shown in this picture.
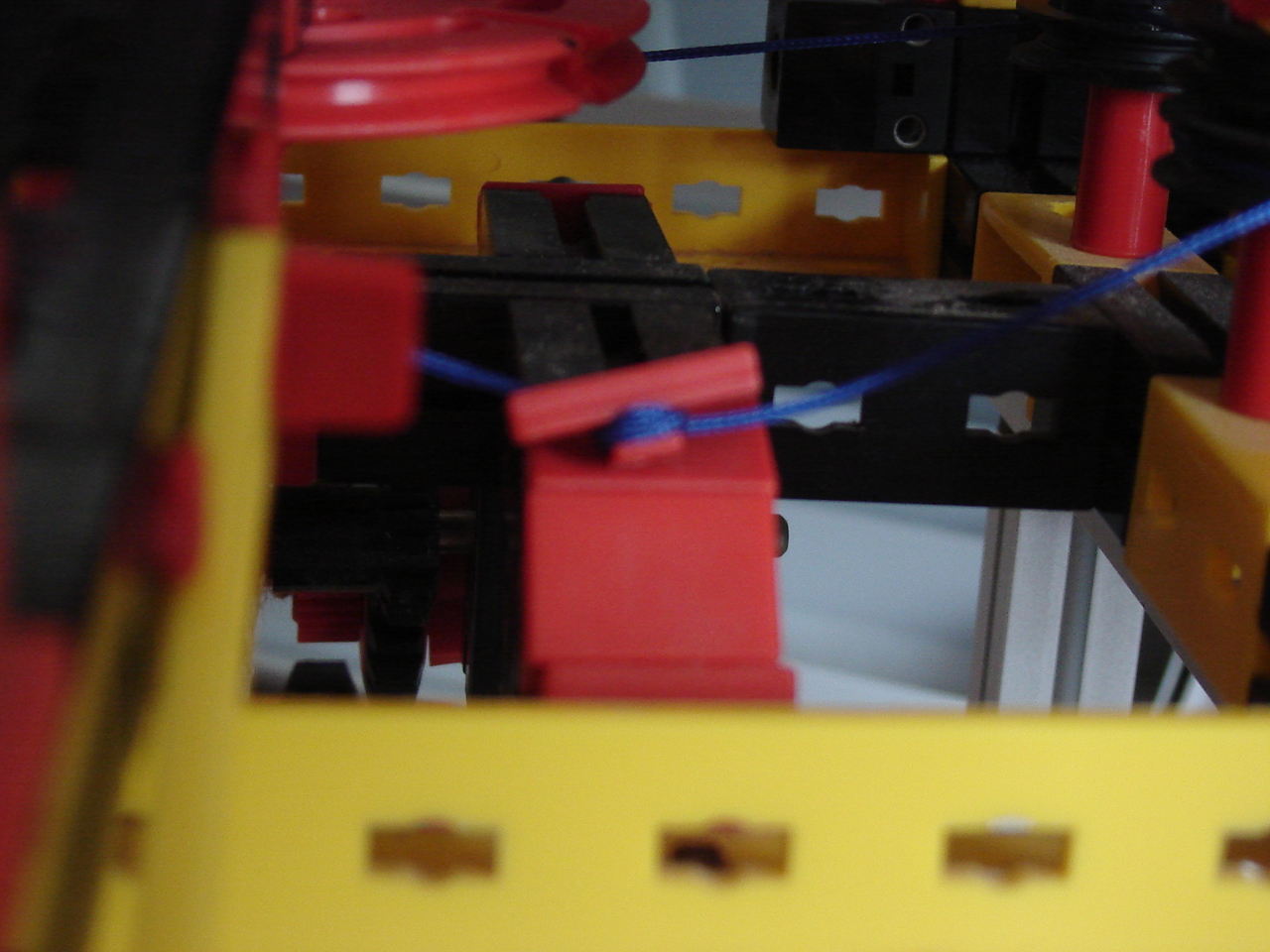
The problem with this is that it is rather hard to place a clover
hitch at the exact positions on the string but with some
perseverance it was done. Another problem is that each one can
only be located at the bottom-side of the hip wheel, so tests will
reveal if this will work with the guide wheels. This
video
shows some first tests.
Hand: After some remarks, I appended some "ends" to the
fingers. I also rerouted a few tubes to the cylinders, so it
doesn't look as wild and unorganised. I also made an overview
video,
but with a partly failed demo because of an airleak.
11 September
RPi: Continuing with the walking
LED, I find 2 causes for the 3rd LED issues. The 1st cause: the
programmed pin and the physical pin don't match: 29 vs. 27. Once
that's corrected, the 3rd LED burns throughout the run of the
program. This is solved by setting pin 29 to "False" before the
actual algorithm begins, so there's no voltage on it. Then when
the LED is supposed to burn, set pin 29 to "True", and the walking
LEDs work. Sigh.
Then it's also nice to have them "walk back" which should just be
a matter of extending the algorithm. Unfortunately, the red LED
goes on and off until the wire to GPIO input pin 32 is connected.
This wire should give the signal for the turn-around. Replacing
the red by a green LED (which burns brighter) doesn't resolve the
issue, but recounting the pins does: the wire was accidentally
connected to pin 34 (ground). So these are pictures of the full
circuit with 3 green LEDs: 1) normal camera 2) webcam
(cropped/edited with Gimp). See also this
video,
RPi video
(HD) and webcam
video (which again looks like speed-up).
1)
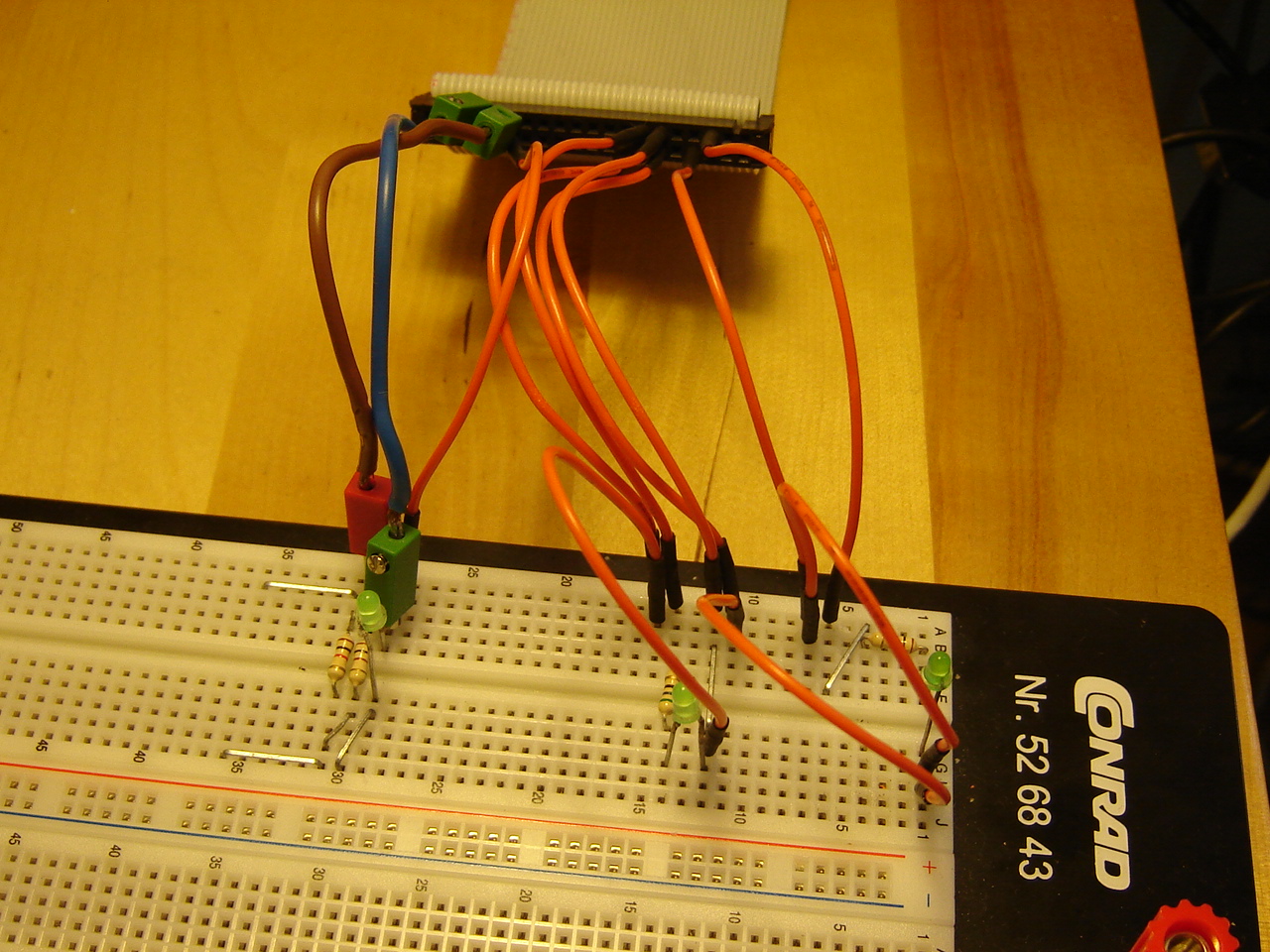
2)
Mirft: Because of the problems caused by the rope for the
horizontal mechanics, I replaced it by the blue nylon string that
is part of a fischertechnik box. See the pictures of both
mechanical ends.
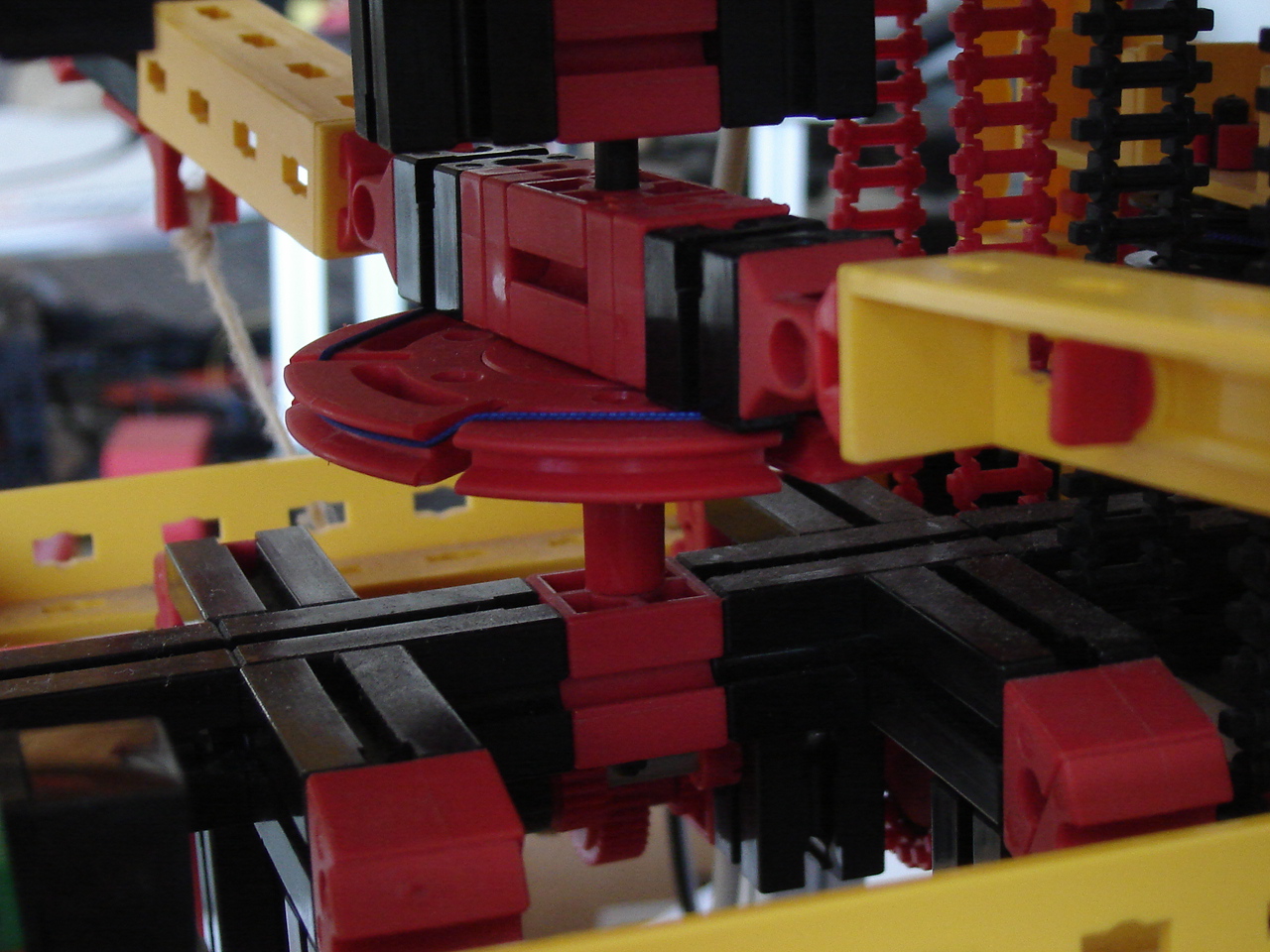
A test shows that it now takes 8 seconds for a leg to move between
its extreme positions. However, since I can't rely on the position
a leg is in, I still have to find an extreme position detection
method. After a small code change by putting the
if
statements a
while loop, I find 2 issues:
- the horizontal mechanics have to be looked after. The winches
slip and loose tension as this
video
shows.
- the vertical mechanics stop too soon. Result is that a leg's
extreme down position isn't reached as this
video
shows.
4 September
Videos: All TeamBuildingDay videos have been put together
now. See the video page.
Youtube: All videos are grouped in playlists now which
makes searching a lot easier.
Picasa: I found that some picture-links on the Video page
were no longer working and corrected them. So all links should
work again.
RPi: A simpler setup of an
experiment is to put a series of LEDs like this: the 1st LED is
put "1", then "0". The "1" makes the 2nd LED going "1" and "0" and
finally the 3rd LED. The schema shows a simplified setup.
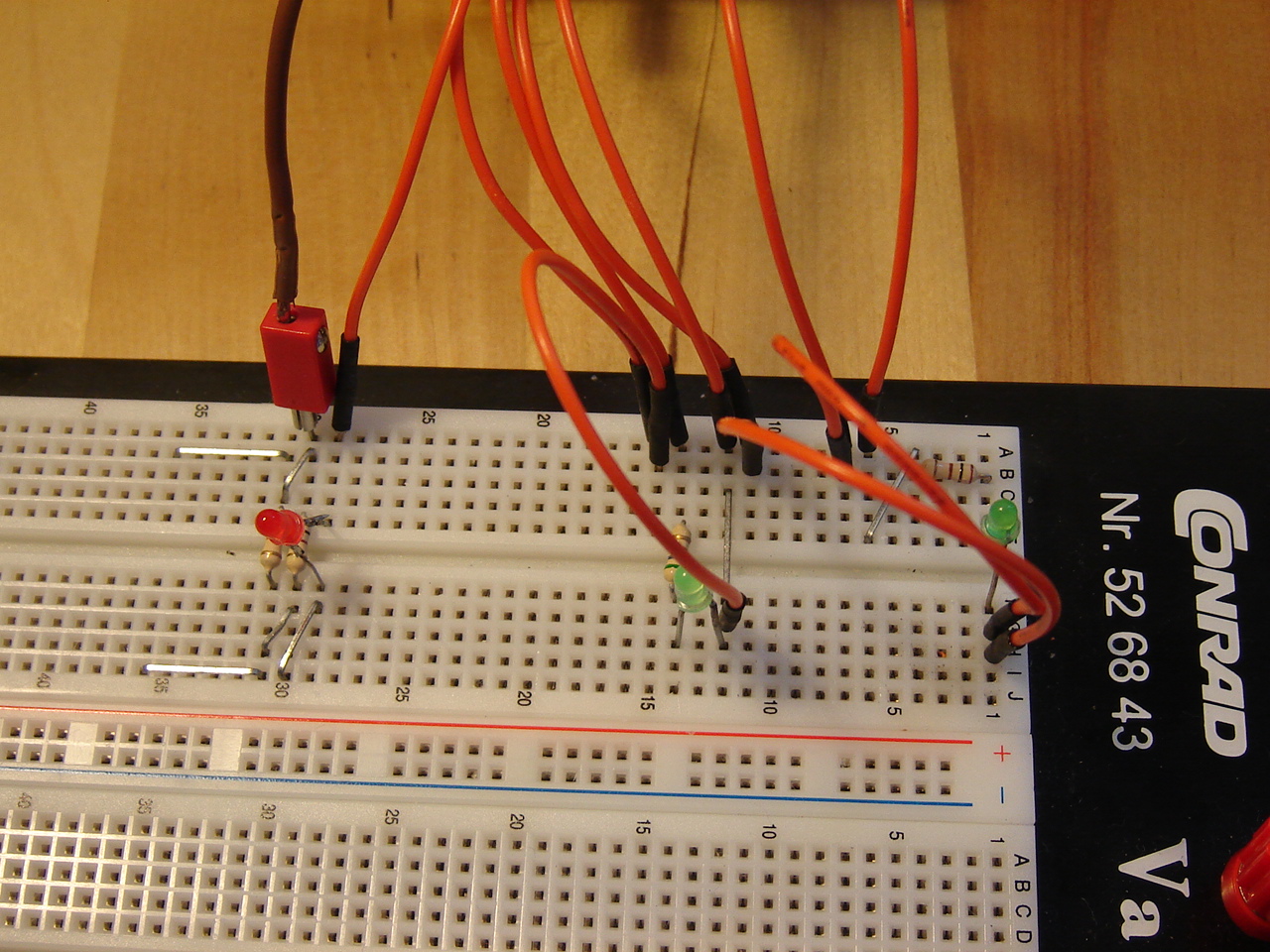
However, during the experiment, GPIO pin 7 goes wrong and starts
giving a constant 1.8 V which leads to a constant low
burning of the 1st LED as shown in this
video.
However, using
gpiotest from
pigpio
shows that only pin 10 (gpio 15:
UART RxD) fails. After reconnecting the
wires up to the 2nd LED, this
video
shows that the program and setup actually do work.
Mirft: The problem with the lights turns out to be both
programming and electric wiring. A few of the remaining problems:
slipping of the mechanical wiring, horizontal detection. This
video
explains (at least a piece of) the way the horizontal movement
should work.
Hand: With 1 spring cylinder remaining, I wanted to add a
4th finger to the hand. Problem is that I only have 3 valves and 2
T-pieces for the air, all of which are already in use. So I
decided to use adhesive tape and put 3 tubes together: 1 from the
valve, 1 to finger 3 and 1 to finger 4.
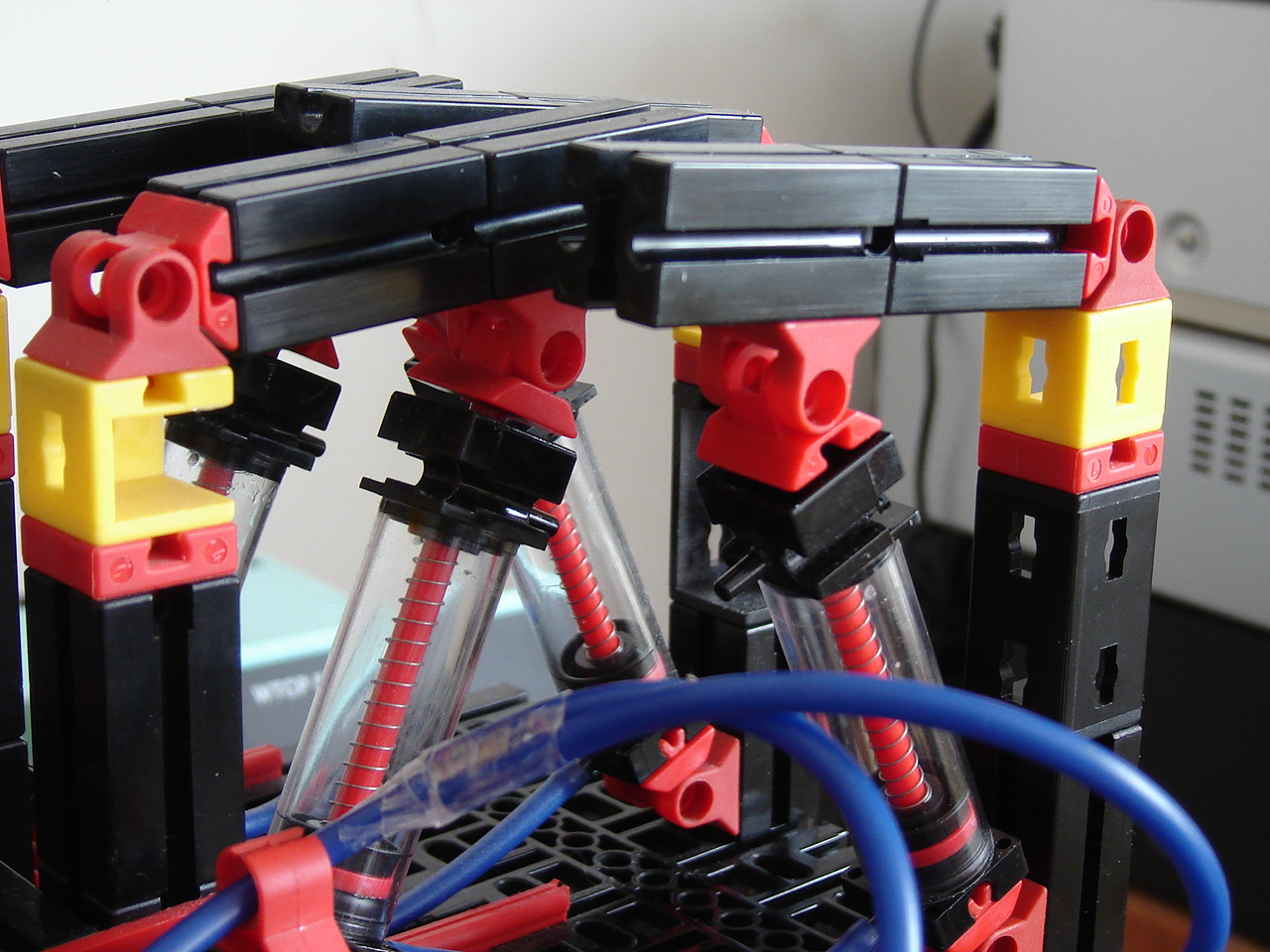
You can see the result in this
video.
28 August:
Videos: All TeamBuildingDay 2008 and 2010 challenge videos
have been combined per challenge and contestant. See the video
page. The rest will be available soon.
YouTube: Created playlists so videos can be found much
easier. More to come.
Discovery: Further testing seem to point at a firewall
problem with an time-window of only 5 seconds.
nmap shows the
needed port 65001 is closed on 192.168.8.100 which is the WiFi
connection to the TXT. With
ufw I
open the firewall for port 65001, and start a test via ssh to
record what actually happens during program execution with this as
start of the output:
-------
01: TxtControl Start
/dev/ttyO2 65000 131 dump.txt
debugflag 1 active: data exchange rates (camera, I/O, transfer)
debugflag 2 active: camera sensor results
debugflag 128 active: enumerate supported camera modes
InitSerialToMot - 1
OpenSerialPortToMot - 1
KeLibTxt: TxtControlLibInit
WLAN-ID: ft-txt_2631
-------
but testing shows no improvement.
RPi: Another option is to use
multiple inductors in series in an RL circuit, thus adding up the
inductance. So to have more inductors, I extend the electrodes of
another one I desoldered earlier and create this circuit and
outputs: screenshot, image from oscilloscope1(upper in schema) and
oscilloscope2 (lower in schema).
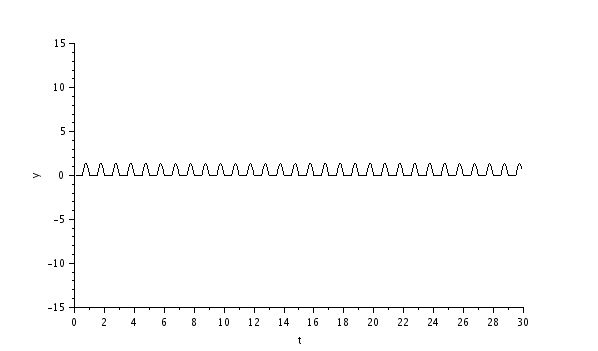
This result shows that although the recorded input to the GPIO
from the inductors isn't alternating the way I expected, the
control LED is constant burning while running the code. Another
result is that the LED behind the inductors doesn't burn. This
appears to be a improper connection, and after reseating the
resistor in the RL circuit, the result is this:
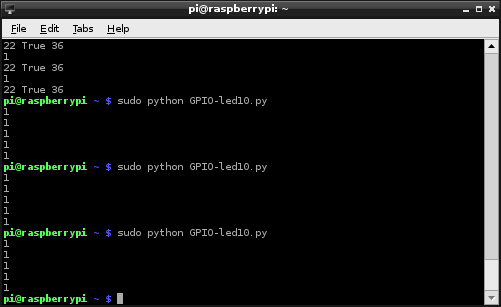
Also, a change of code (adding
time.sleep of 0.5 second)
for the control LED makes it alternating. The change is necessary
since this LED is directly controlled by the GPIO, not by the
transistor. So the end-result of this experiment can be seen in
this
video
and this
video
(RPi camera in HD).
Mirft: Getting back after focusing on the Discovery, there
are some sensor issues such as lamps that don't burn when they
should, receivers that report "on" when the lamps are "off". Since
I'm using the
RF DataLink for remote communication, I
remove it for testing and use a wired USB link. This seems a bit
better, and after checking some wires it improves even more for
the lamps. However, the sensors still report wrong data, and the
motors don't run. Time for troubleshooting.
21 August:
Discovery: The TXT will be left out of any ROS experiment
because, although it runs Linux, it doesn't run a supported Linux
version.
On colour detection: in this
video I'm
using a ROBOPro example program that acts on the colour red which
doesn't work either. This convinces me the problem is not with my
software. Running
wireshark might show if it has something to
do with the firewall or not.
RPi: Experimenting on ROS for
RPi starts with a bit of research that takes me
here. If I want to install ROS, I have to
build it manually.
Continuing with the RLC circuit, I want to have a 3rd LED indicate
that the RPi detects via the GPIO that the circuit works.
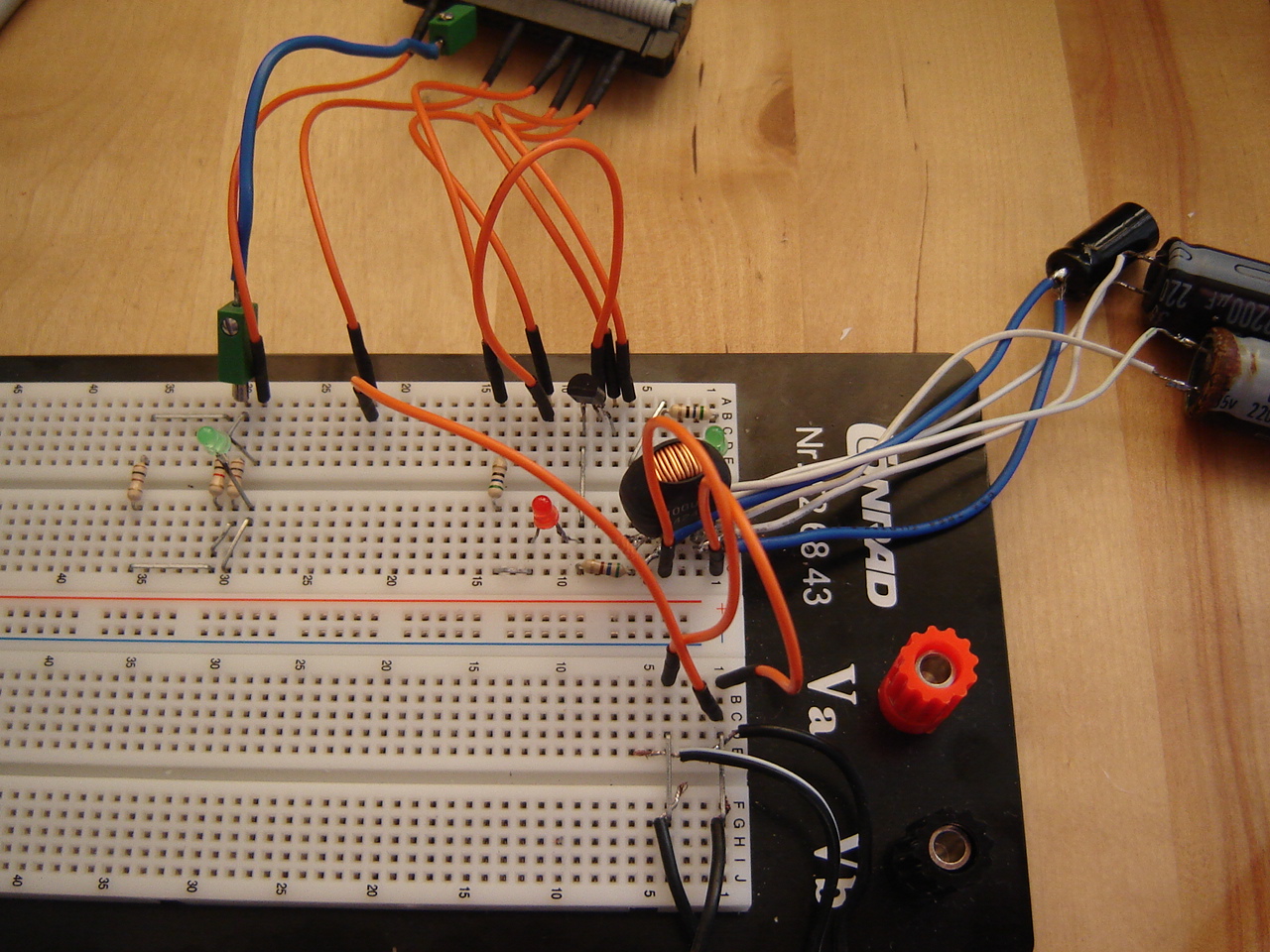
So I place a jumpwire from the green LED at the end of the RLC
circuit to the GPIO input pin and see if it is detected by
---
print GPIO.input(22)
---
it prints 0, so it isn't detected. Simple explanation: the voltage
at that point is quite low. Then I relocate the jumpwire end from
the green LED to the parallel C part (which is the end of the
circuit) and the input on pin 22 shows 1. However, the 3rd LED
doesn't burn. Although this is unlikely, reason can be that the
100 Ohm value of the resistor is too high. This can be solved by
resistance division: put multiple resistors parallel and the
inverse total resistance 1/Rt = 1/R1 + 1/R2 + .... So in case of 2
resistors of 100 Ohm, 1/Rt = 1/100 + 1/100 = 1/50, making Rt = 50
Ohm. Despite this solution, the 3rd LED doesn't burn the way I
expect it to do.
Time to do some tests:
1) Putting the 3rd LED parallel to the red LED proves that the 3rd
LED works fine.
2) Measuring the voltage on GPIO pin 29 (used as source for the
3rd LED) shows a permanent 1.69V, which is wrong.
3) Measuring the voltage over the green LED after the RLC, it
shows faint burning at 1.69V, so the 3rd LED should do the same.
4) In enough darkness, the 3rd LED does show a constant very faint
burning, merely a glow which is easy to miss.
Since pin 36 can be in- and output as well, a solution can be a
change from output pin 29 to 36. After changing the code
accordingly, the 3rd LED burns very brightly as this
video and
this
video
(RPi camera) shows. So what's wrong with pin 29 ?!
BB: Searching for software that can be uninstalled leads to
the discovery that PyAudio actually is installed. However, the
printing of errors on screen
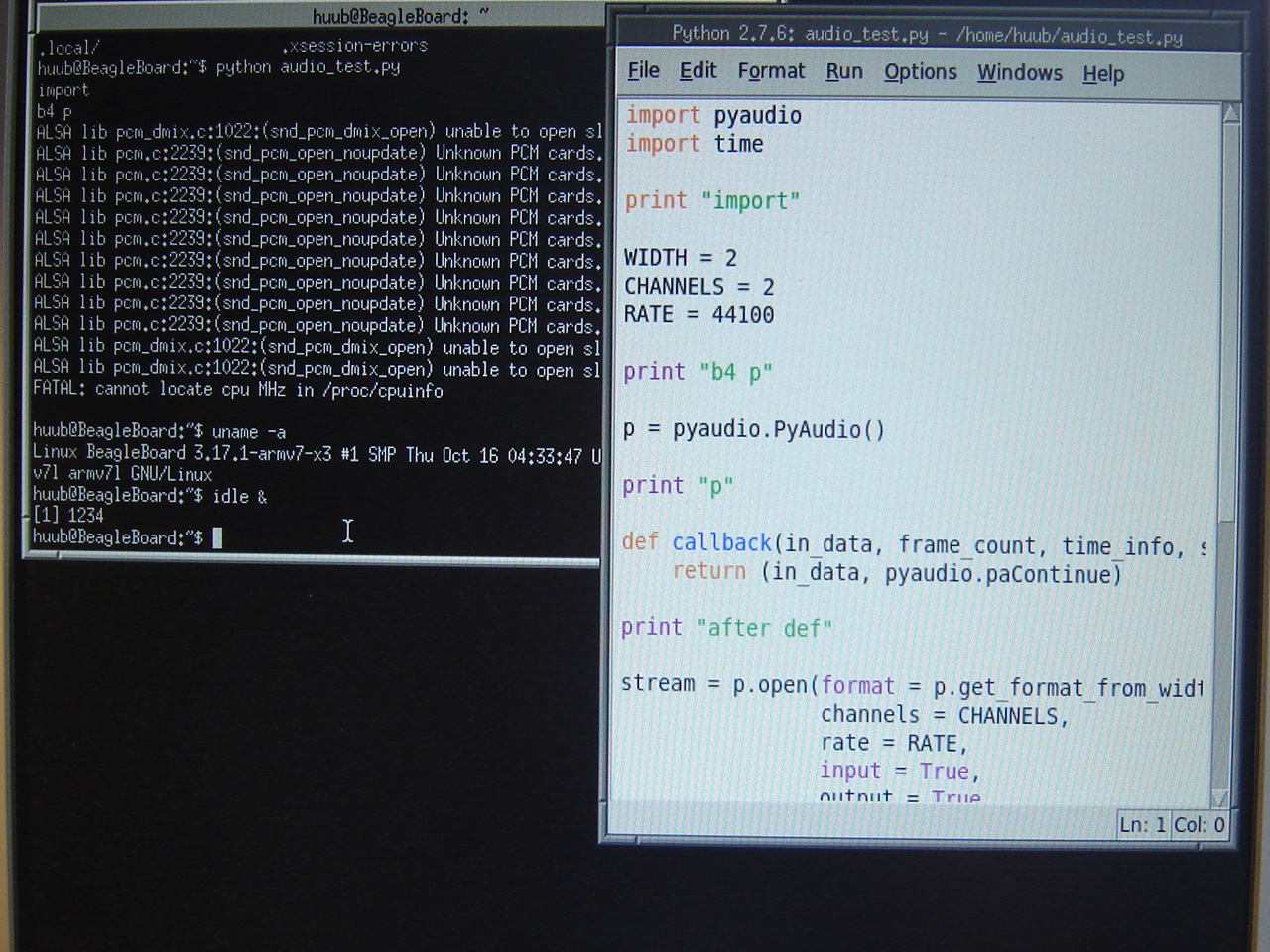
reveals that it probably won't work as easy. The last line returns
"unable to open slave". Another "FATAL" error is "cannot locate
cpu MHz in /proc/cpuinfo", although according to several forums
this is a kernel issue. So I guess audio on the BB won't work for
now. Because Ubuntu runs on the BB, ROS should be installed
easily.
ROS: Apart from the embedded boards, the laptop runs Fedora
Linux, which is unsupported by ROS. So if I want to use ROS on it,
I would have to replace it by Ubuntu and for some weird reason
Ubuntu/
Xubuntu/
Lubuntu 14.04
doesn't even boot my laptop. I decide to install ROS on an
ordinary pc with Lubuntu (which goes smooth) and will see from
there.
14 August:
Early videos: I realized that the videos links I gave in the
beginning of the blog still lead to Picasa. Of course all
these videos are on Youtube now and accessible via the video page.
I will not change the links in the blog to Youtube, unless I'm
asked to.
Discovery: With the camera live-feed on the tablet,
I took these images of the lines that should be followed.
According to the developer, these should be no problem in being
detected. The last 2 image are made with different light
intensity.
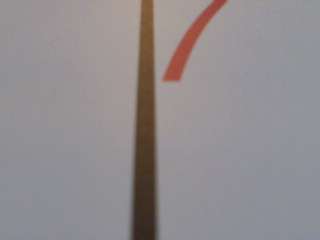
Then another problem starts being quite persistent. Previously
there was no problem using the WiFi connection from ROBOPro.
However, now I keep getting the message that it can't connect to
the TXT. Testing this from a terminal with ssh, there's no problem
getting on the TXT. Also, getting camera live-feed on the tablet
is no problem. Eventually I'm able to make this
video.
In the flowchart you can see where the short 2 seconds pause is
(the lamp burns) and which at times takes a lot longer (without
the lamp burning) probably due to communication issues.
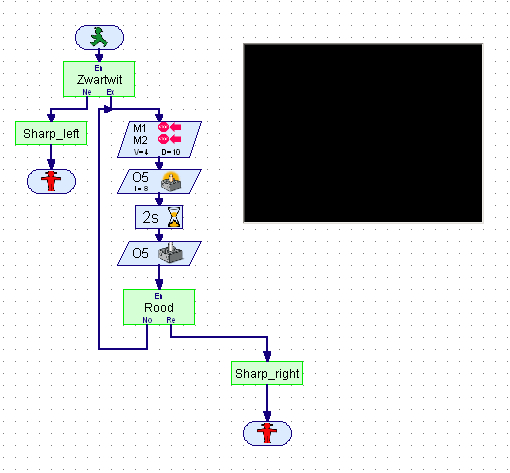
Since Bluetooth is another option to communicate with the TXT, I
use a Bluetooth dongle which finds the TXT nicely and pairs with
it. However, after several attempts trying to set up communication
between ROBOPro and the TXT, there is no result. Probably because
it a USB dongle and wine doesn't know how to handle USB.
The next attempt is to load the test program into the RAM of the
TXT via USB. This at least takes out the flaky WiFi connection
between the TXT and the laptop. Remarkable is that other WiFi
connections with the laptop go fine. Unfortunately, this
video
shows that this doesn't solve the problem either. So if the
problem isn't either software or the camera, it could be the TXT
itself.
BB: Since the use of the webcam has only delivered speed-up
videos, apart from good pictures, a better idea is to experiment
with
ROS,
likely in combination with the RPi and laptop. Since ROS enables
communication between devices via messaging (within ROS also known
as topics), basically all my controllers can be interconnected.
Only issue is that I'm using a 16 GB SD card with 97% used, so I
can't install ROS right now. Maximum SD card capacity for the BB
is 32 GB.
RPi: Another component is the
inductor,
with symbol L. Building on the circuit from 7 August, and looking
at example RLC circuits, this is the most interesting experiment
yet. The letters are in sequence from the voltage source, so the
resistor comes first. This also means I have to redesign the
circuit: a resistor to begin with and one to end with (a
protection between the GPIO and the LED). In between the resistors
will be the inductor and capacitors.
From old PCBs I get inductors of 4.7µH (H = Henry) and 100µH.
Using the 100µH, and simulating an RLC circuit with a resistor of
2200 Ohm, the signal after the capacitors does get stronger as
expected, but the maximum value stays at 0.25V and with 0.25V a
LED will not burn.
Increasing the resistor to 10k Ohm doesn't improve the result, as
the pictures show: actual setup (1),schematics (2), upper
oscilloscope(3), lower oscilloscope (4). With a 56 Ohm resistor,
the 2nd oscilloscope graph (5) which ends in a simulation solving
error after 18 seconds.
The results are as a series RLC circuit: as the resistance is
higher, the end result is over damped. With a low resistance it
should result in under damped (so the green led after the
capacitors should burn at start) but the simulation ends in error.
As you can see in this
video (normal camera) and this
video
(RPi camera), using a 56 Ohm resistor, it does work with the green
LED in the RLC circuit burning rather faintly. This again shows
that a simulation is not always showing the same result as the
real thing.
1
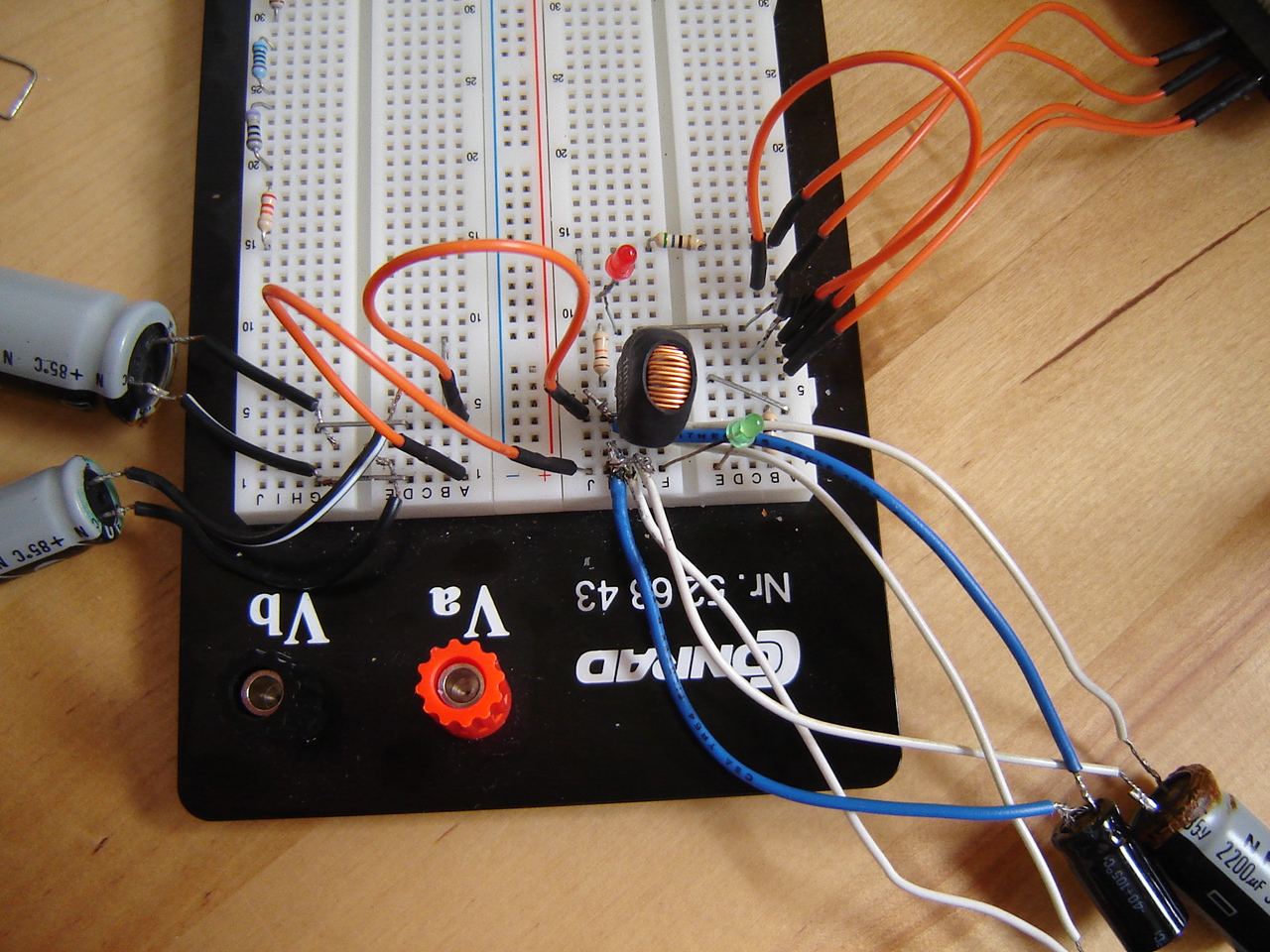
2
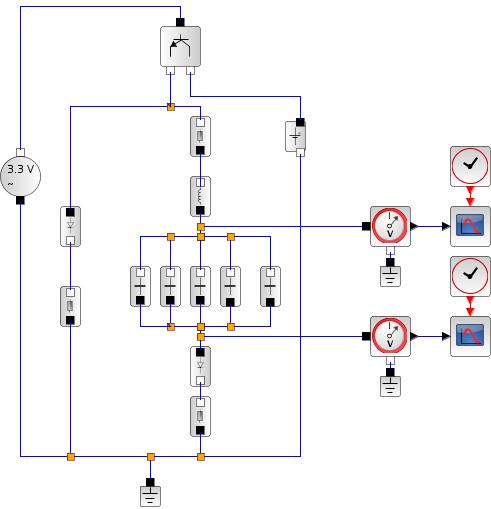
3:
4:
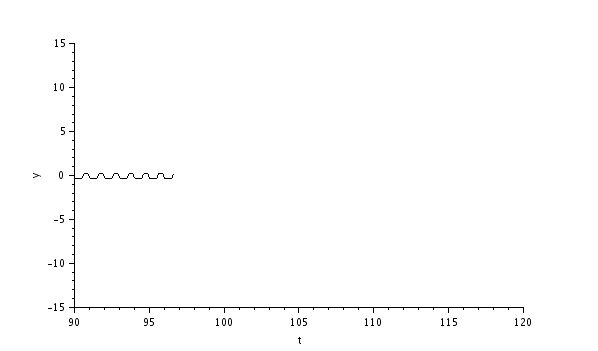
5:
7 August:
Fix to 30 July blog: pictures.
RPi: A component I didn't use
yet, is the
capacitor. So it's time to experiment with
this one. The plan was to have a LED before as well as after the
capacitor. The first simulations showed there was no voltage after
the capacitor, which was just 100pF (picoFarad). To solve this,
the voltage source has to be a multitude of 3.3V. Since this
can't be realized with the RPi, the solution is to increase the
capacity and use
electrolytic capacitors of at least 1000 µF
and put them in parallel. That way it should work according to the
simulation: the LED on the negative side of the capacitors shows a
dimming effect as can be seen in the simulation and
video. At
the first run, the green LED burns quite brightly, and during
subsequent runs the LED quickly dims until it no longer burns.
After that, you will have to wait a while before starting again
because the capacitors need to discharge first, which happens
slowly.
As you can see in the pictures, I had to extend the
electrodes
of the capacitors with wires because they were too short for the
experiment. Also, I had to extend the working space for the
experiment due to the number and volume of the capacitors. To
create the extension I used jumpwires and I used staples as aides
to connect the capacitors in parallel. The staples were necessary
because the extended electrodes would not stick in the breadboard.
The total used capacity = 6800µF + 3x2200µF + 1000µF = 14400µF =
14.4mF.
Discovery: After making contact with the developer of
ROBOPro, it turns out that wine doesn't support USB. So that will
be the prime reason that the camera doesn't work in ROBOPro when
attached via USB. However, I use mainly WiFi, which should work.
It turns out that the camera only responds to a colour when it
doesn't
fill the complete image. Another problem may be that the
lsusb
command on the TXT doesn't list the camera.
After a few small adjustments to the testcode, and testing with
black/red line-colour recognition it first seems to work better
but either colour still isn't recognized. To be continued again..
30 July:
Youtube: I've put the last old convention videos from
Hoofddorp (2011) and Vlissingen (2008) online that were on Picasa
only. Since Picasa still shows the error "invalid parameters" when
playing videos I will remove them. The pictures will remain on
Picasa.
RPi: The next experiment is to
replace the resistor by a
potentiometer or potmeter.
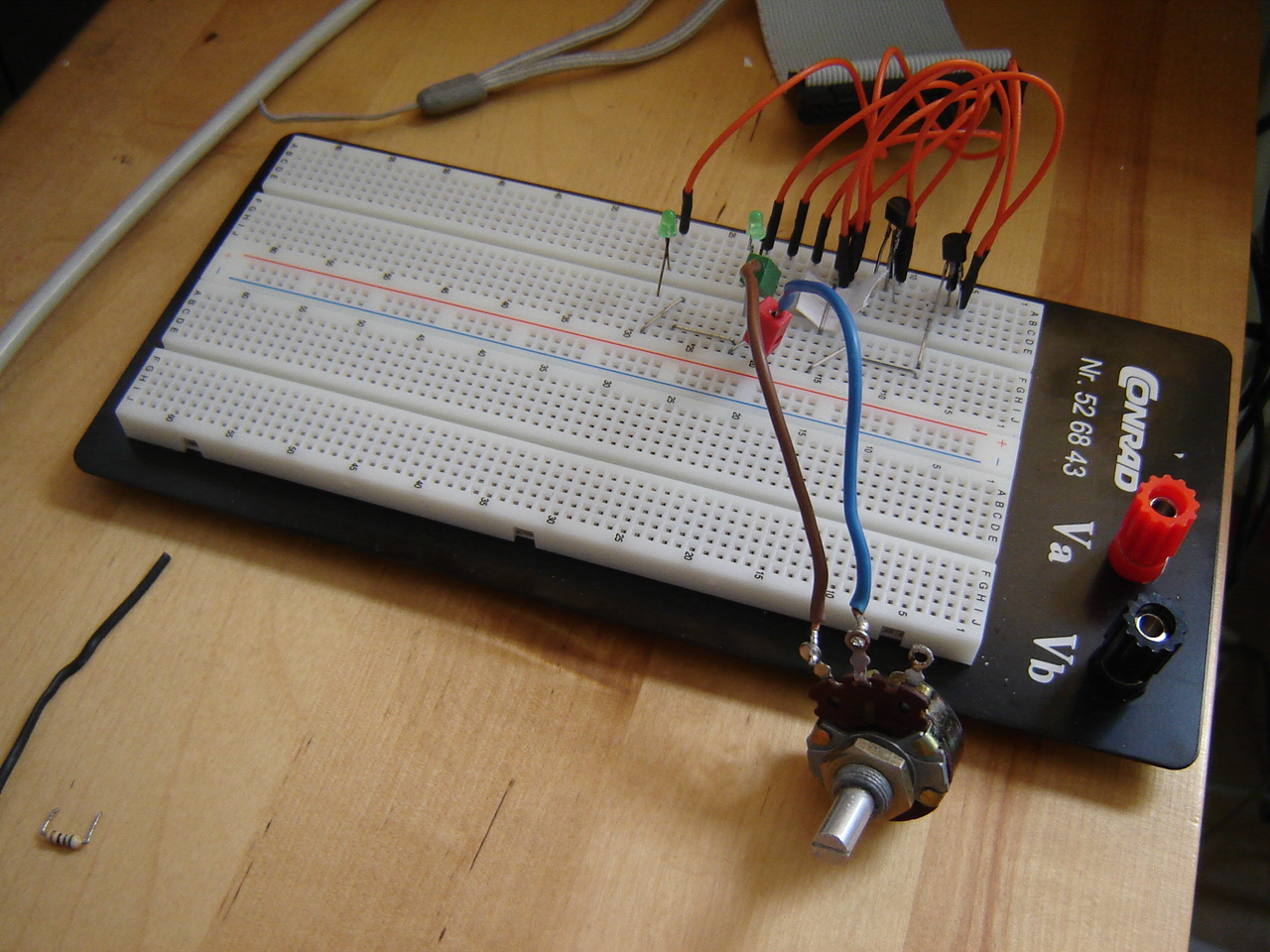
Reason is that the brightness of the LEDs would be dependent on
the resistor value. However, with the used potmeter, there
is no visible difference in brightness. Unfortunately I don't have
another potmeter to continue this experiment right now.
Another experiment is to record the semi-random blinking pattern
in a textfile using
f= ('<file>','w') where
<file>
is the filename to write to and
w is the writing action.
So, when e.g. input 16 and 18 are both
low, 'none' will be
written, otherwise only the
high will be written. After
writing, the file needs to be closed which is done using
filehandle
f, so
f.close(). Then, you can also
have this writing action indicated by a flashing LED, so I added a
red LED that burns for 0.5 second during any write-to-file action
as shown in the picture and in this
video.
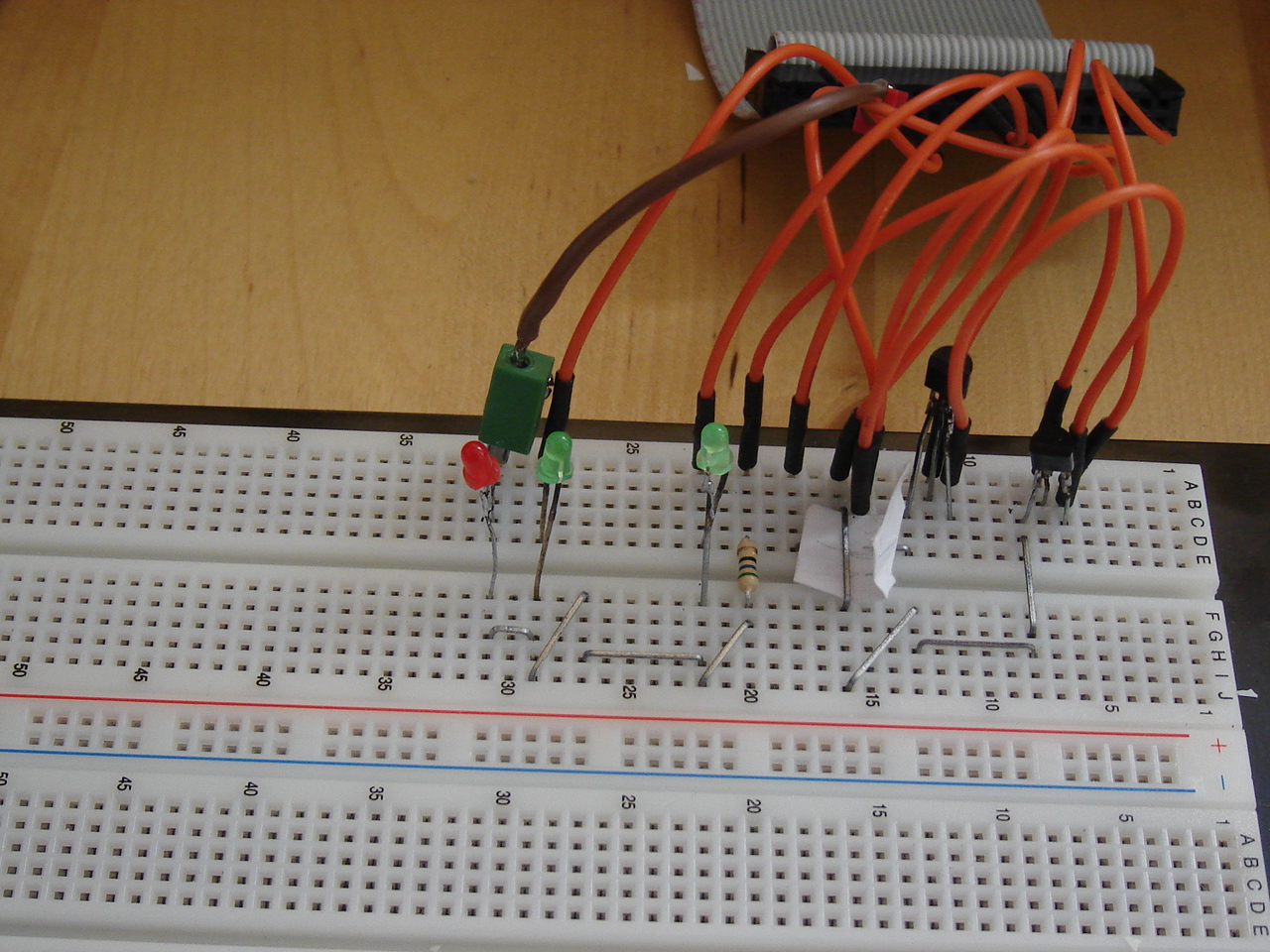
The Python code snippet that writes to the file and burns the red
LED on GPIO output pin 31 when GPIO input pin 16 is high and pin
18 is low:
------------------------------
GPIO.output(31, True)
f.write('16\n')
time.sleep(0.5)
GPIO.output(31, False)
-------------------------------------
In the picture and video you can see I use a brown wire to
connect the red LED to the GPIO. This is just for substitution as
I'm out of orange jumpwires. As shown also in earlier
experiments, the red LED burns less bright than the green.
Discovery: The colour detection is still giving problems.
After the red, the blue and green detection fail as well. Then I
try it after uploading my software to the TXT which means a change
from online-mode to download-mode. Now it shows different
behaviour: it seems to work although I can't verify it the way I
want: with numbers and text displayed. After simplifying the
program and uploading it to the TXT controller, some testing
reveals it still doesn't work as this
video
shows.
BB: In a new attempt to create a non-speedy video with the
webcam, I change the XVID format into MJPG. What happens is that
the video only shows the very first recorded frame and nothing
else. The second attempt shows even less: just a very short
flashing image. Using VLC, the video can be started and as soon as
it starts you have to click pause. If you blink, you might think
it only shows black. So after changing back into recording
.avi,
using the semi-random LED blinking code, I get this 5 seconds
video. After this I try
the DIV4 format with
MPG as well as
mpeg extension
but both result in entirely back recordings. To be continued...
Arduino: After the last successful play with the e-brace, I
found that it fell quiet again. Apart from that, somehow
minicom
(or Linux ?) managed to swap
/dev/ttyUSB0 (to the RPi) and
/dev/ttyUSB1 (to the Arduino) which didn't happen before.
After removing the Arduino connecting, it took several hardware
reconnects to get the RPi connection fixed. To be continued...
23 July:
RPi: After using 1 GPIO pin as input, I start another
experiment and break up the Darlington transistor. I put the
transistors separately as shown in the circuit image and the
picture of the breadboard. The randomness of the result is shown
in the screenshot of the code output where 16 and 18 are
GPIO pins programmed as input lines, the normal
video and
the
video
with RPi camera which is made later than the first video and shows
different patterns because of the randomness.
Discovery: The detection of colours seem to go very
different than with the RoboInterface: using the USB camera. Using
ROBOPro, you first have to select the camera and add colour
indication. After that, write a piece of software that uses the
detected colours to filter out e.g. red and give it as feedback to
the main part of the program. It looks like that a constant
integer used in the example program (containing a subtract and a
comparator with a constant) doesn't work in my code, as if red
isn't red. The next attempt is adding a check for black. Although
this seems to work, replacing the object (and thus colour) from
black to white to red makes no difference once again. Then
simplifying the code, I remove the subtract and the constant, and
connect the comparator to the colour-inputs, but again it doesn't
work as expected. Doubting the camera works correctly, I connect
to the TXT with my tablet, and find it actually does work as can
be seen from these saved live camera images.
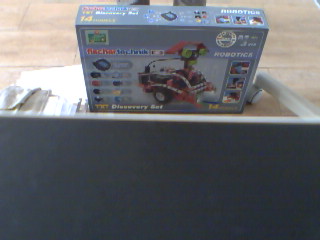
Using example software from the TXT controller, I find that the
red detection for some reason doesn't work. In this
video,
you can see how my code should work and doesn't detect red either.
17 July:
Discovery: In preparation for the real stuff see this
video of
the barrier model I built from the construction manual. The
software is running in online mode for now, which means that it
runs from the computer and is not uploaded to the controller. What
I find is that not all building instructions are as clear as could
be. For me it's no problem, since I can figure it out. But since
it's intended for children, I doubt all children can figure it out
(but I know there are very smart ones out there...).
After this experiment, I built another model with a wheel-base
from the manual and further leave the manual for what it is. The
first tests with the wheelbase show a little defect in 1 of the
backside wheels. After replacing a part of the construction, it
works fine. With this base model working ok, I can figure out what
I can do with it with which sensors.
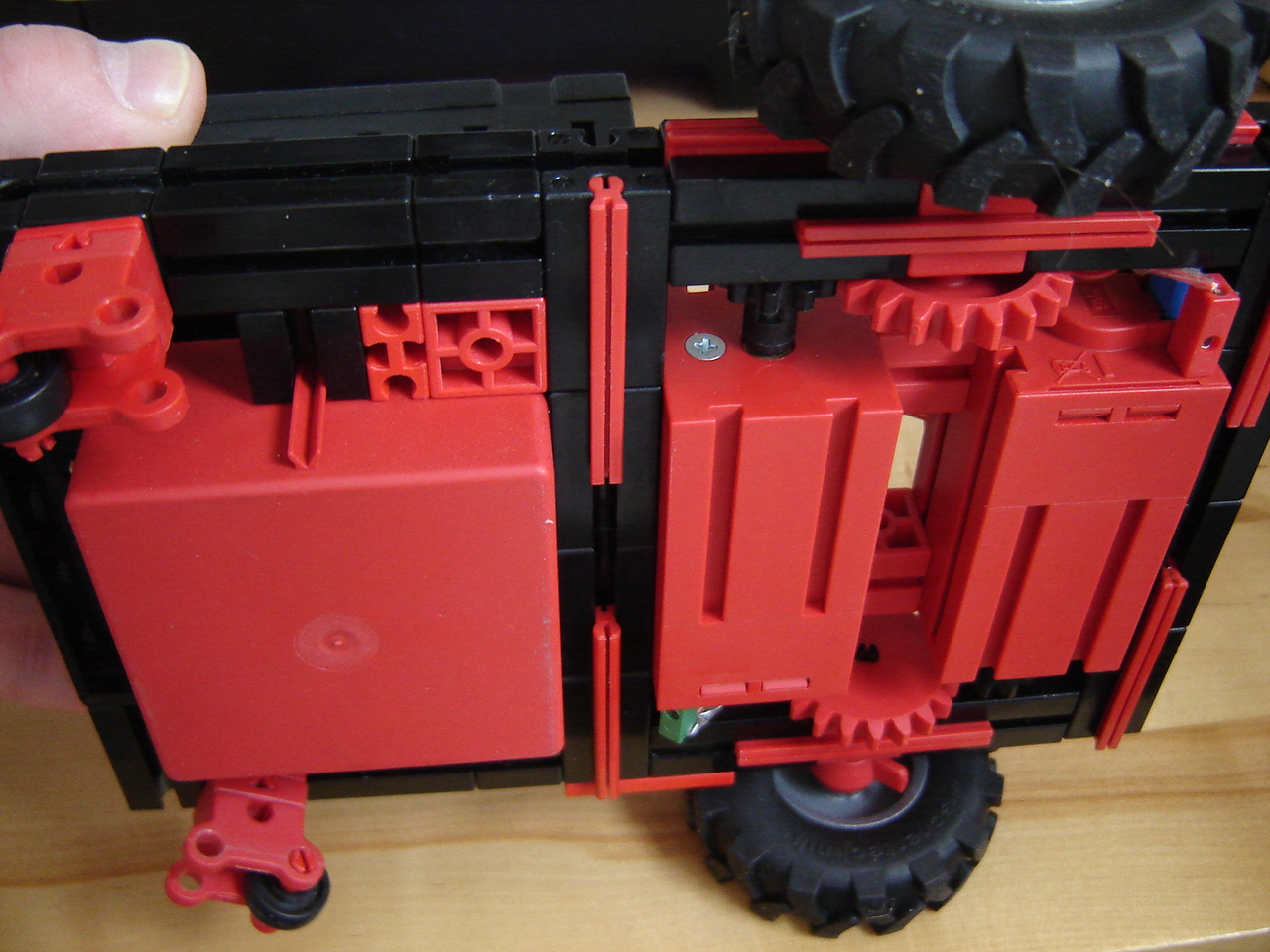
A first addition to the wheelbase is the TXT-USB camera. I can
watch its stream using a special app on my tablet. What I notice
is that either the uploaded program works or the video feed.
Selecting one stops the other.
Then a program I "write" in ROBOPro, Discovery-test.rpp, should
first make the robot drive forward at speed 4 for 3 seconds, then
make a 90 degree turn left, a 90 degree turn right and stop.
However, the drive forward often goes in a curve, so the 2 motors
don't always run equally fast. A small change in the program let
it make use of the pulse-count of one of the pulse-motors. In this
video,
the online-running (via WiFi) program counts 400 pulses from the
motor until it lets the motor stop for the first time. After that
it turns left and right.
RPi: So far, I haven't used the
input function of the GPIO. So I added this to the last circuit
(see 10 July entry). The idea is to let pin 16 detect if the LED
is burning, and if so, have pin 22 burn another LED. The first
setup is to have pin 16 connect to the LED and I find that the LED
to pin 22 doesn't burn. So I measure the voltage to pin 16 and
suspect that it might be too low for its input. A 2nd attempt is
to connect it to the base of transistor 2, and now it does work as
this
video
shows. Conclusion is that the input of GPIO has a minimum
threshold voltage. What I also notice is that the red LED burns
much dimmer than the green LED, despite its higher voltage. So
when I replace red with green, I find it burns a lot brighter, as
this
video
shows. This
video
with the RPi camera gives another view.
10 July:
Arduino: Back to the Arduino. During some experiments (see
14 June), I put it in programming mode. The result is that in
SerialMonitor, it shows ISP now, which stands for In System
Programming, and seemingly can't quit no matter what input I give.
After another full power-off (USB cable and battery disconnected)
another attempt and for some reason it suddenly accepts input
again. A final 'q' results in 'OUT ISP' and the message 'Choose
Action'. So although I'm back where I started, the gain is
experience..
Discovery: I've decided to
let the C++ go for now and see what's possible with ROBOPro, the
graphical programming 'language' for fischertechnik. It seems it
has a lot improved with additions such as floating point which is
common in C/C++ and Python. So in the coming time I will build the
examples models and see where it leads.
For a quick test, I build a small circuit: controller, lamp (O1),
light-sensitive transistor (I1), an encoder motor (M3) and a
buzzer (O7). The flowchart graph actually is the program as it
runs in ROBOPro. As usually, there's a catch: the transistor
doesn't work properly. For some reason it always takes the 1, no
matter if the light is blocked oir not. Measuring the voltage
directly at the transistor always shows 0.1 V which indicates it
doesn't detect light. Replacing it with a transistor which has
proven to work doesn't change the situation. Conclusion should be
that the wiring is the cause, but since the proven transistor
doesn't work either I doubt replacing the wiring is the solution.
RPi: My next experiment is using 2 NPN transistors and 2
LEDs in series
. In Scilab/Xcos simulation this gives that
the 1st LED burns fine, and the 2nd LED burns very weak. Testing
with the real circuit, the multimeter shows 0.40V on the emitter
of the 2nd transistor: too low to let the 2nd LED burn. However,
taking out the 1st LED and connecting the collectors to each
other, creates a
Darlington transistor as shown in the graphs
and this
video. The 1st is the voltage directly after
the 2nd transistor.
3 July:
RPi: I've made another
.avi video of the LED
blinking via the transistor using the webcam. So although it runs
the same length as the other 2 videos (made with the Sony cam and
RPi cam) it looks like it once again is sped up. I'm using
fourcc
=
cv2.cv.CV_FOURCC(*'XVID') to create an
.avi video
and despite examples with other formats like
mjpg, I
haven't found anything else but
avi that delivers a good
video using the webcam.
Using the existing circuit, I wondered how fast the GPIO can be
switched on/off. So I changed the sleeping time in my code
gradually in seconds from 1 to 0.01. It turns out that 0.015 is
the shortest sleeping time that shows actual blinking of the LED
with my naked eye. In this
video the blinking is barely visible (it
goes on/off for 500 times).
After desoldering more parts, I got a hold of a S9014 transistor,
which is an NPN type. So now, the circuit looks likes this in
Scilab with the simulation signals as shown in the blog of 25
June. This
video
doesn't show any difference in LED blinking but the wiring is
definitely different.
Discovery: Apart from the earlier mentioned sources,
fischertechnik also published the
rootbuild software of
the controller. Using this you can work in offline mode:
scp
your own binary and have fun. Just the rootbuild needs to be built
on your local system and uses
git as well. Before
building, it needs to be configured like any other kernel. In this
case, it can be configured as an Eclipse plugin. And here's a
catch, for me. Eclipse is a really nice
IDE but a real memory hog. As such it's not
recommended to use on low-memory systems with only 500 MB. So next
try is to build it on a different system and then copy it to the
TXT. Following a tutorial, I find that I have to use a newer
Eclipse version (Luna) than I have (but not the newest), which
proves hard to download. The fact that it's not the newest (at
time of writing this blog: Mars) is because the buildroot-plugin
supports up to Luna. After that, I need to give the plugin site,
which I have to give different than the tutorial tell. Then, after
copying the modified sources to a newly created C++ project it
seems to build with warnings. To be continued.
25 June:
Mirft: After the stabilization of all 3 hip/legs, it turns
out that the last 2 cause a slightly wider hip. So I decided to
replace the 1st stabilizing construction with the same one as the
last 2. With this stabilizing act, and the lower legs attached
again, a simple lifting experiment shows a weakness of the legs.
When there's an uplifting force, the leg bents uncomfortably right
below the 'knee'. This is (for now) solved with a supporting
piece.
Another problem still present is the detection of the horizontal
extreme position of the legs. To detect this, a mechanical mini
on/off switch is a possible option, as shown below. However, as
wiring and location show, it both placing in the middle and at the
sides give problems.
RPi: An expansion of the LED experiment is to use a
transistor, which is actually an electronic switch. In the shown
schematics, the alternating voltage connects to the
base
of the transistor and causes the output voltage on the
collector
between the LED and the resistor to go on and off. In practice, it
doesn't work like this. The sine voltage of 3.3V actually is a
GPIO pin that will be programmed to go on/off. As a result, the
output voltage looks more like a block wave (on/off) than a
half-sine (slowly on/off) as shown in this
video.
From the RPi side, I created this HD
video.
There is also an oddity. The first simulation was with an NPN
transistor and worked great, showing the output as intended (in
the graphs below). When I found out that the used real transistor
is a
PNP type, the simulation was redesigned (as
shown) and fails to work
19 June:
Videos: I have put older videos from the fischertechnik
Schoonhoven and Veghel conventions on Youtube, which were
previously only on Picasa.
Mirft: For the walking robot Mirft, 2 legs/hips still
needed to be stabilized. Since the part I used for the rear hip
stabilization is out, the solution is shown in the picture
below with a current overview next. I also created a narrated
overview video which is only available via
this blog and the video page. So with the stabilization hopefully
done, some serious software testing can be done.
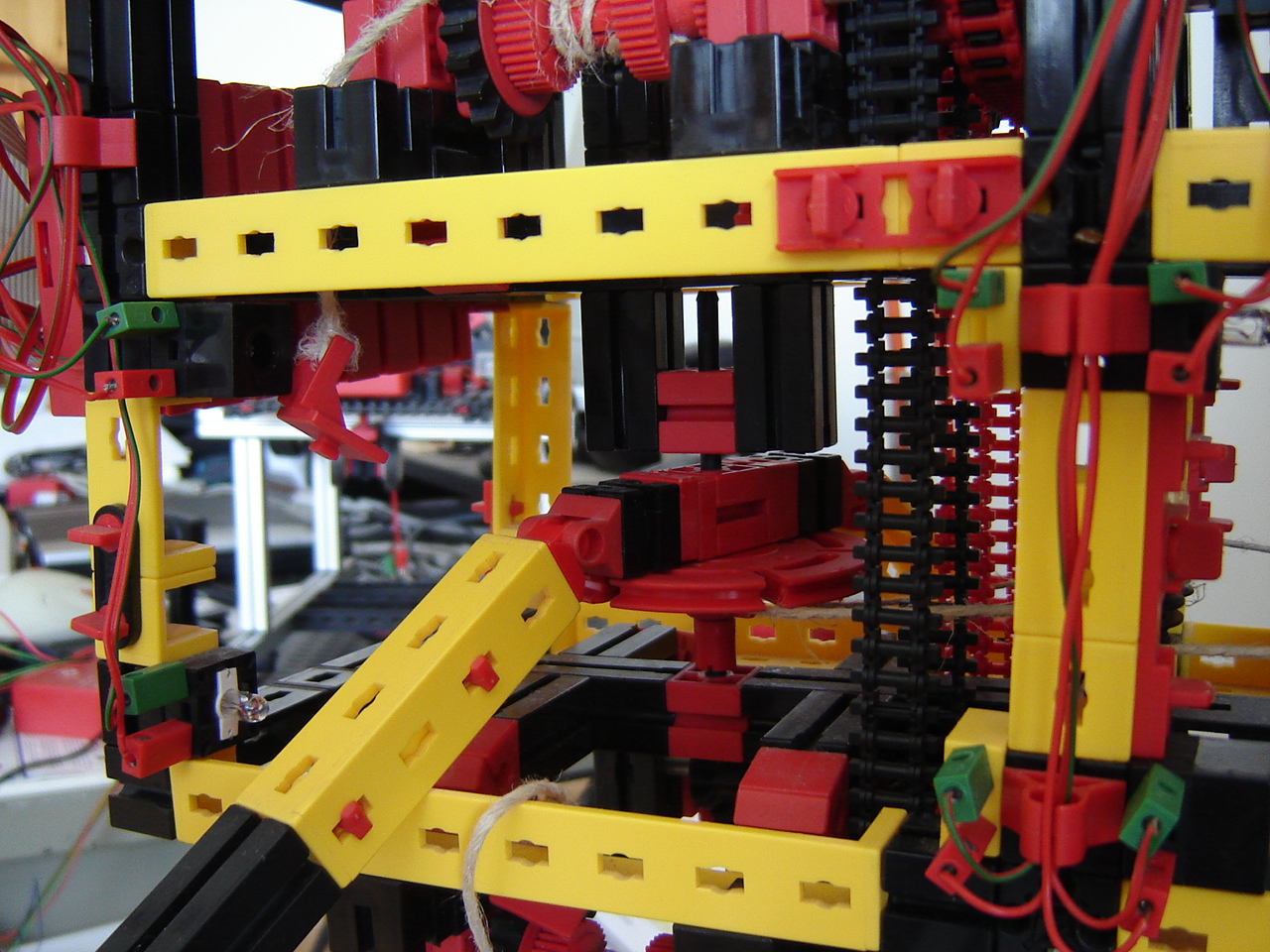
RPi: The next experiment is connecting a fischertechnik
(ft) buzzer parallel to the red LED and a 9V ft motor parallel to
the green LED. The buzzer works nicely, but the motor doesn't work
and causes the green LED to stay out. After disconnecting the
motor, the green LED burns again. Also, when simply replacing the
LED with the motor, the motor does nothing. Although a test shows
that the motor is able to run on 2.5 V, the motor apparently is
too heavy for this low-power circuit which runs at 3.3V. There
exists an RPi motor controller board, that uses part of the GPIO
and allows a motor and an extra batterypack to be attached. The
heart of this board is the SN754410NE chip, which is an
H-Bridge
that can control the speed of a least 1 motor.
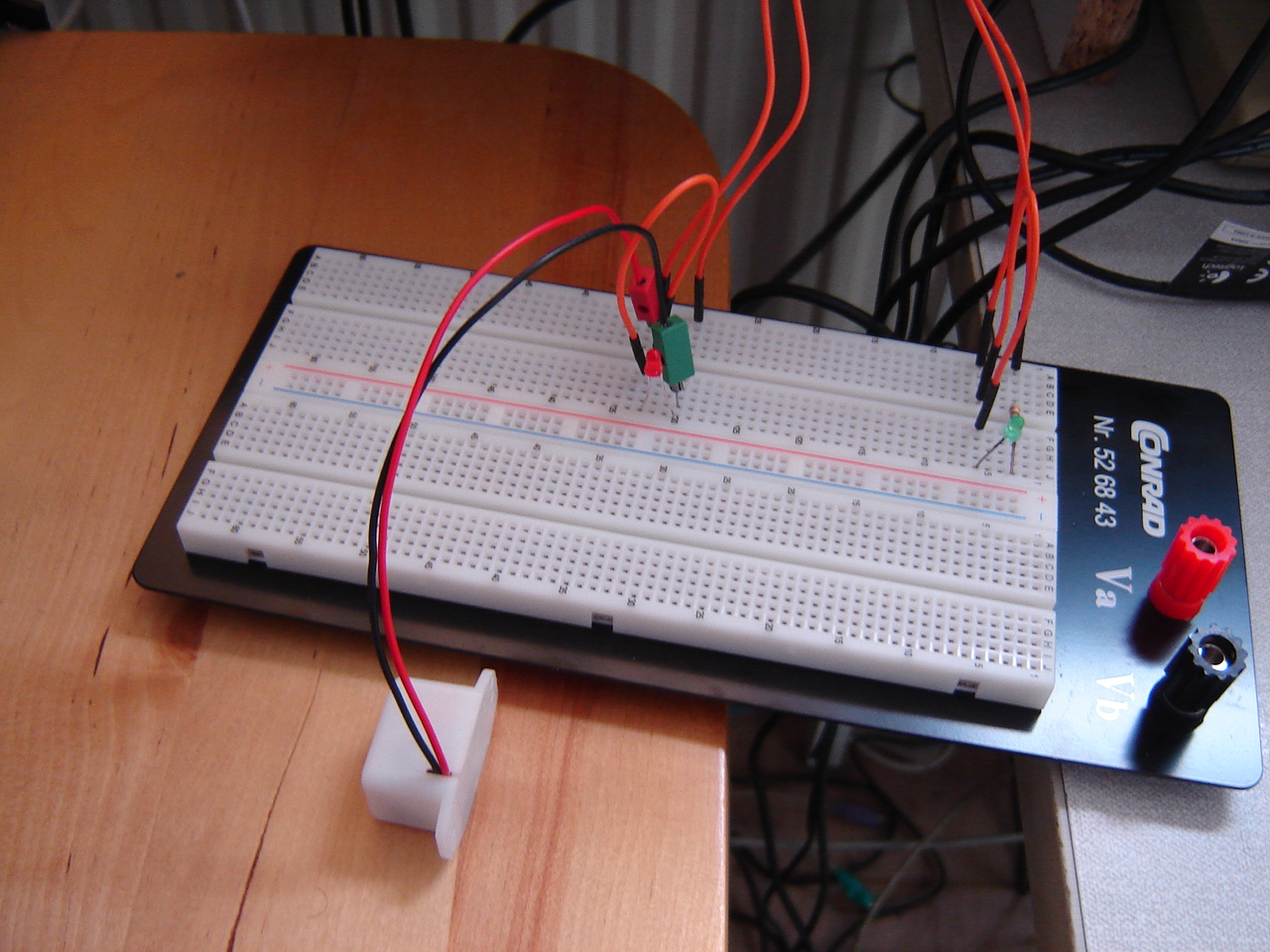
To make sure a circuit can work without using hardware, you can of
course use a simulator, such as Scilab-Xcos. The circuit with the
green LED looks like the screenshot below and the next screenshot
shows the voltage between the resistor and diode during
simulation.
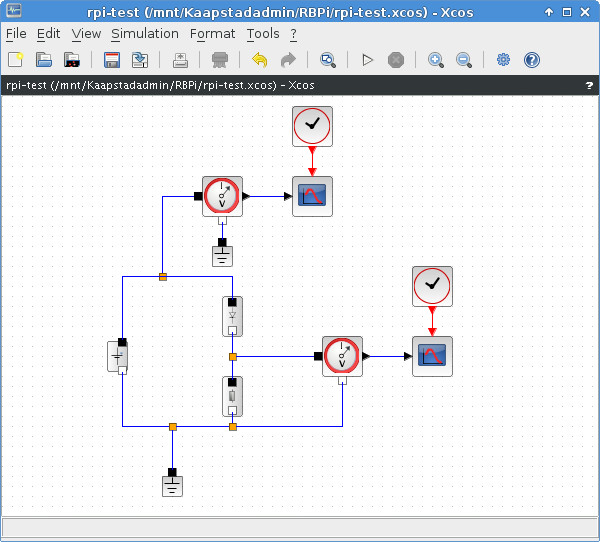
Discovery: fischertechnik (finally) released documents to
enable programming for online mode without using ROBOPro with a
simple trick (replacing a default IP address with either 127.0.0.1
or
localhost) for download mode as well. Of course, when
you intend to use download mode, you also have to cross-compile
the executable for ARM before uploading to the controller. The
example software is written with Windows in mind and uses
winsock2.h.
This needs to be disabled: either with
#ifdef WIN32 or
commented out entirely. Also
SOCKET isn't used and
according to various posts this should be replaced by
int
(i.e. integer). After compilation there are
undefined
references which would indicate library issues. After trying
with the use of
-I (to use headerfiles) and
-l (to
use libraries) switches of
g++, the errors remain.
14 June:
Arduino: Last time I told about the e-brace without giving
real hardware info. So here goes: it uses an
Atmega328 for each of the light, movement
and sound. For the controller the Atmega324 is used.
Using information from the Elektor e-brace forum, I can
successfully use the Serial Monitor and switch on/off the various
modules: 1: light; when active the LED shines red, 2:
movement; when active the LED shines green, 3: sound; when active
the LED shines blue. Since there isn't yet a program loaded,
option 4 doesn't do anything yet. So, using data from the
gadget.h
Linux library (to be used in software) via Serial Monitor you can
read/set the e-brace without real programming. With this info I
give e.g. '8' as input and it shows different X-Y-Z coordinates
after moving the e-brace to a different position.
In this
video
I show the switching on/off of the mentioned modules using the
Arduino Serial Monitor. Then I wanted to make a video that showed
this Serial Monitor on screen and my hand moving the e-brace.
However, in video-mode the camera has auto-focus and when I point
it at the laptop screen the focus changes constantly. So
when I hold the e-brace in front of the camera, it focuses on the
e-brace and the Serial Monitor goes blurry. So much for a video
experiment. Oops.
BB: Recently I succeeded in taking pictures by using video
with my Logitech webcam. Since it is quite cumbersome to copy each
picture to the laptop in order to view it, I decided to install
gpicview
which is also used on RPi. This has a rather small memory
footprint (i.e. uses only little working memory when in use) so it
is started quickly.
For creating a video of the LEDs without taking images and using
the webcam, I find a piece of code on the web at Python OpenCV
tutorials. With a slight change I can create an
avi video
which, to my surprise, lasts only 6 seconds while the full 20
seconds program is run. As if the video goes fast forward and
shows it 3 times faster. Other formats than
avi haven't
yet resulted in usable videos.
RPi: In continuation of the experiment with 2 LEDs, I tried
to make another HD video with the RPi camera. It takes several
attempts to get an acceptable result, for various reasons. In no
particular order: the green LED is out of sight, the red LED is
not visibly burning on camera (it is visible with the naked eye)
and the RPi camera is out of focus.
The "out of sight" is easily solved: just move it in sight. The
"not visibly burning" is because it doesn't burns as bright,
caused by a higher resistor value. I can't change that for now,
since I can't find a resistor with a lower value than that. I
finally "solve" this issue by changing its position upwards, so
the red LED faces the camera. The "out of focus" can't be solved
since from documents it appears that the focus is set to distances
of at least 1m. So 10 - 15 cm is an oops. The HD
video
will be published anyway. After replacing the improvised setup
with a breadboard, it looks much better. And after replacing the
fischertechnik wires from the GPIO with a flatcable it becomes
electrically safer on the GPIO side and gives more flexibility in
the whole setup too.
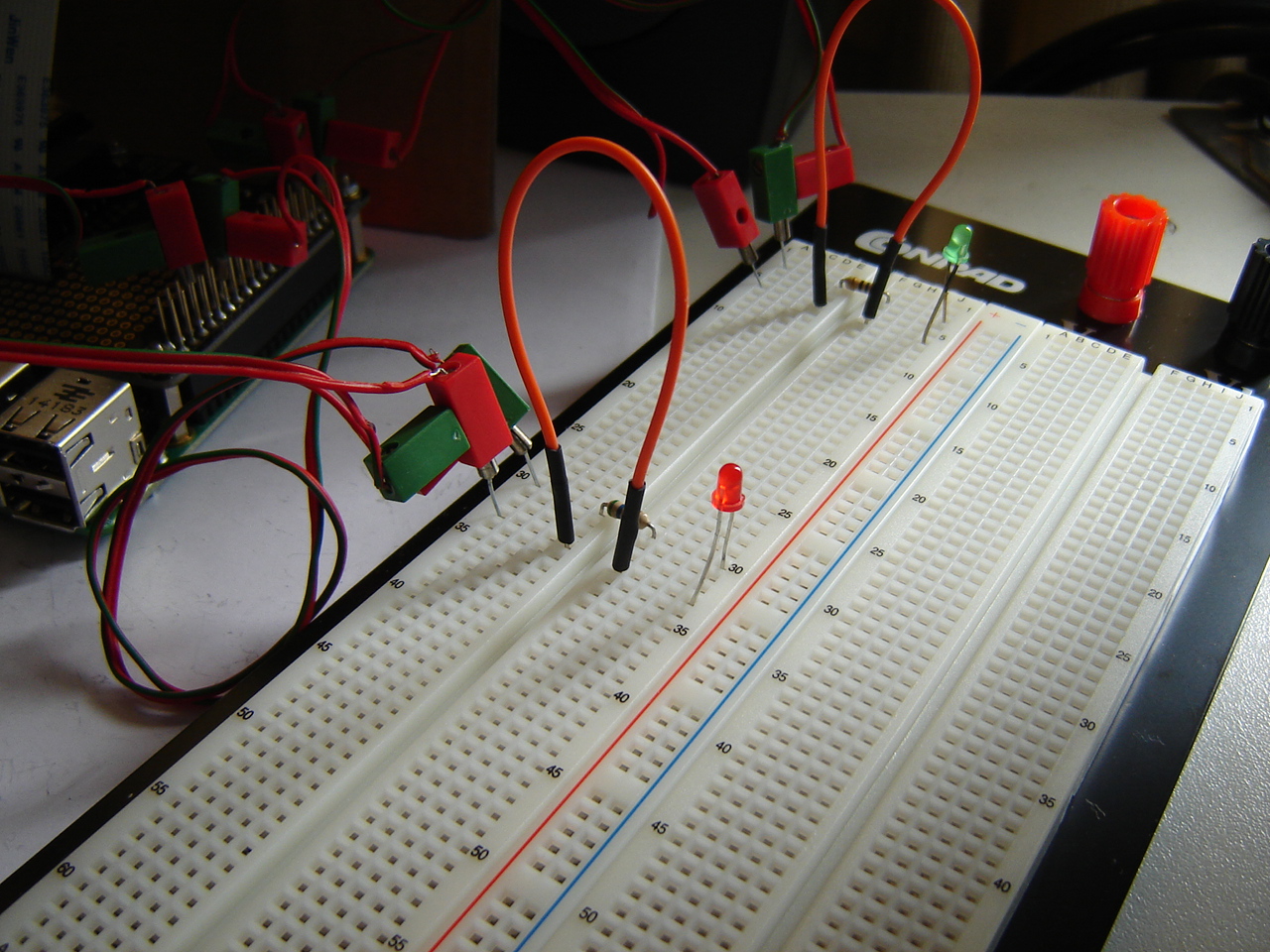
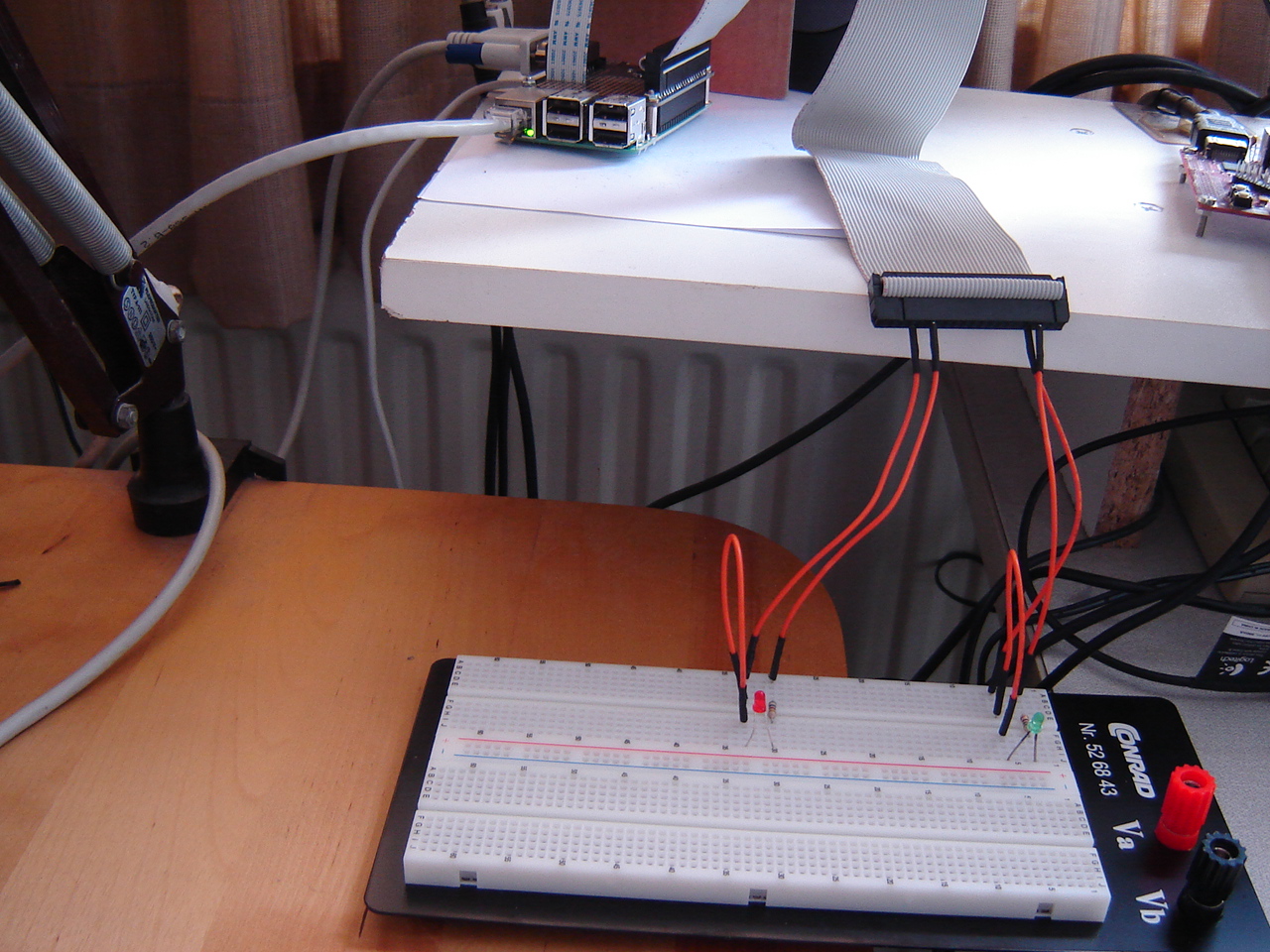
On the resistor values: the one for the green LED is 56 Ohm, the
other is 560 Ohm. Fortunately, I find another resistor 56 Ohm
resistor, so now both LEDs burn equally bright.
9 june:
Mirft: A possible solution to the instability of the hip/leg
construction is shown in the latest pictures on the Mirft page.
Unfortunately, so far I lack 2 items of the same part to stabilize
all 3 hip/leg combinations. After putting the new solution in its
place, it works better although the hip hinge is not really solid,
but it will do for the current set of experiments without putting
much weight on it.
RPi: I found a nice little
project to create a blinking light using a resistor, LED and the
GPIO of which I could make a video with the RPi camera. So now I'm
desoldering LEDs, resistors and such from old PCBs to get a stock.
Too bad I don't have a breadboard i.e. a board for the use of
electronic components in experiments.
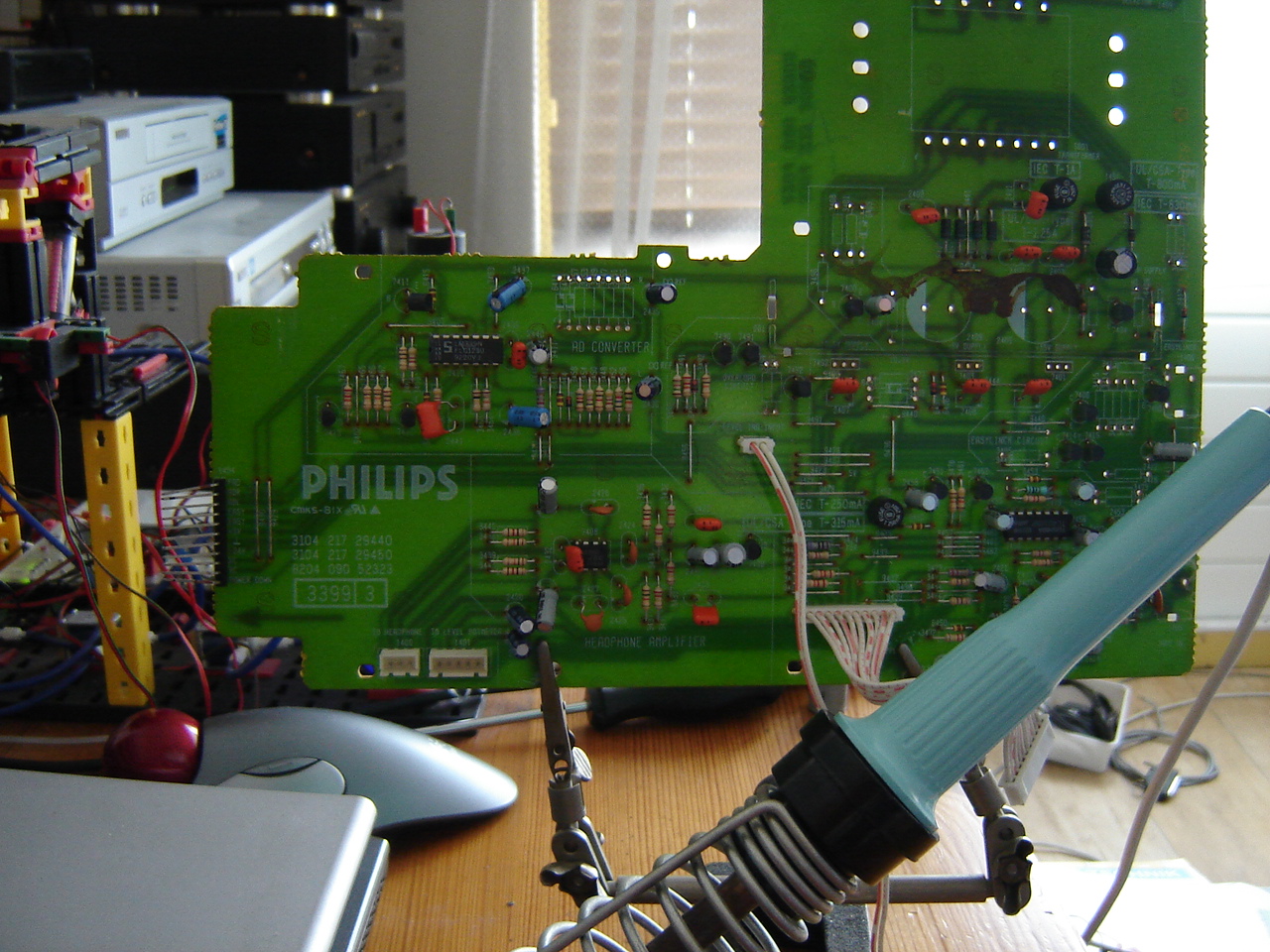
Improvising with a 50 Ohm resistor, a green LED and fischertechnik
wiring, I make a circuit. With the circuit starting at GPIO pin 1
(3.3V), the LED burns bright.
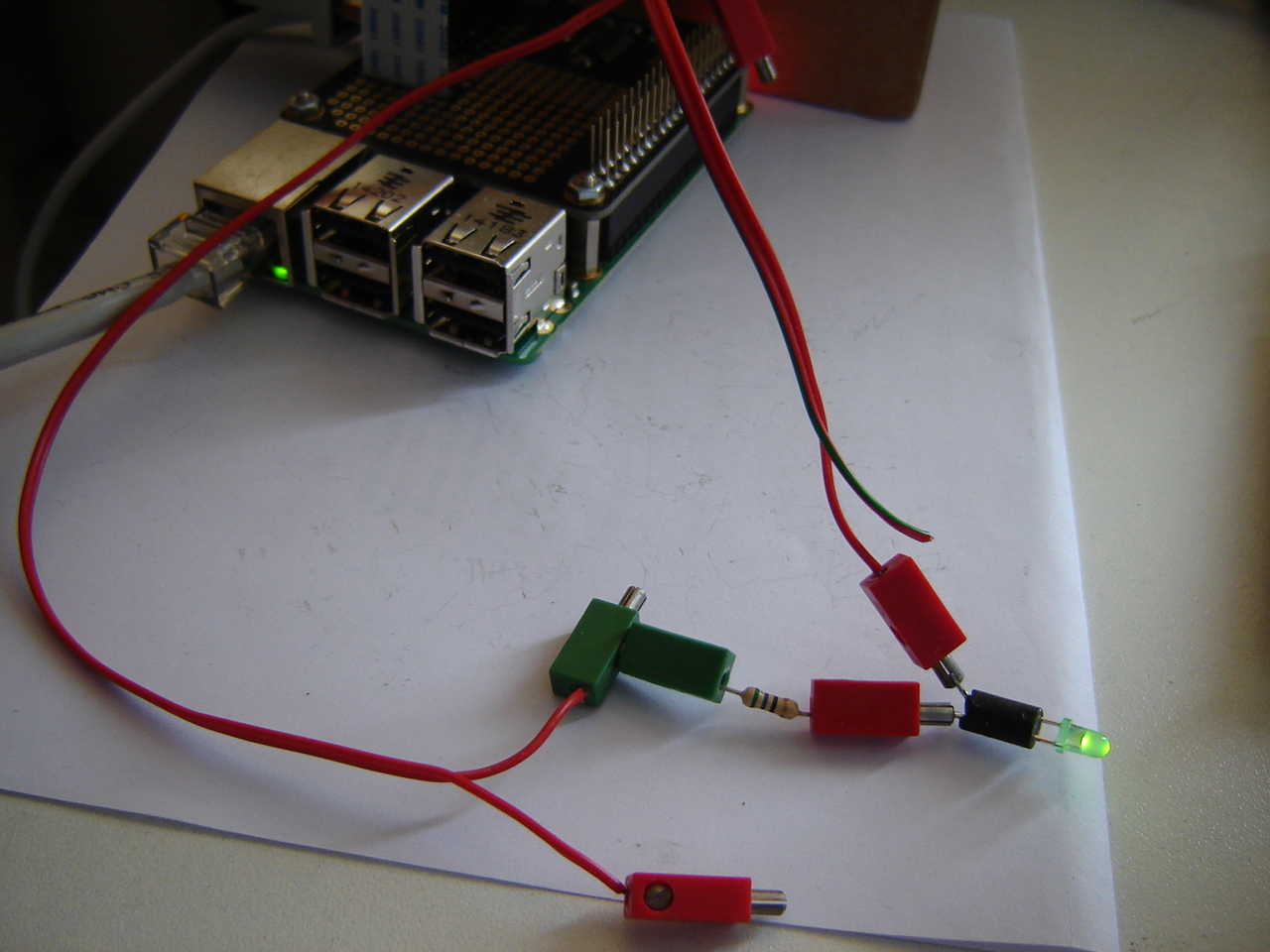
The next experiment, is to connect the circuit to GPIO pin 7,
which is a controllable pin. However, after setting the burning
time to 3 seconds nothing happens. It turns out that this is
because the GPIO is only accessible as root. So,
sudo python
GPIO-led.py works fine and filming it gives a nice 5 seconds
video. Since this is rather short, I extend the program and
another
video
is made with the LED multiple times blinking. After this, since
the RPi has a camera of its own, a 20 seconds high resolution
video is
made with the blinking LED. Both videos are public on Youtube and
on the video page. The third experiment is connecting a red LED to
pin 30 (GND) and pin 33. With a slight adaptation to the program,
there are 2 LEDs blinking. The only downside with the improvising
is that the wires quickly get messy.
Video: I got the good suggestion to combine the short
videos into a larger one and put that on Youtube. Although a first
result using
Openshot
is nice, the question is in which format and resolution it has to
be saved: there are a LOT of choices. Another option is the use
the online Youtube video editor and the first one from 2008 using
this editor is online via the video page. All takes time though,
so I will decide how to go on after getting feedback. Without
feedback, it stays with this 1 video.
Arduino: on the Electronics & Automation trade show at
4 June, I walked 7 "steps" to collect an e-brace: get the PCB,
have the firmware flashed, get the USB cable, get the battery,
provide it with an ID, get a wristband and do a handshake. The
actual final step is to install an app on your smartphone or
tablet to see the IDs of those you did an handshake with. And this
was the downside for me, because the app required the phone/tablet
to have Bluetooth 4, and my tablet has 3.
This device is an Arduino, so actually another embedded system. To
work with this, I installed the Arduino IDE and when starting up
got an
headless error. It turns out that it uses
openjdk
rather than
Oracle/Sun java and I had only installed the
headless version of it. There is this command
update-alternatives
--config
java that shows which java is standard on the computer, and
it only showed
openjdk, while for Eclipse I use Sun java.
So I decided to install the non-headless version of
openjdk
after which the Arduino IDE starts nicely. The device connects
with the FT230X USB cable, which is
/dev/ttyUSB1.
Following the documents, it turns out that although it can be
selected, it can't be opened:
permission denied. This is
because I'm using the IDE as a normal user. After changing the
start into
su root -c "/opt/arduino-1.6.4/arduino", the
serial monitor can be accessed.
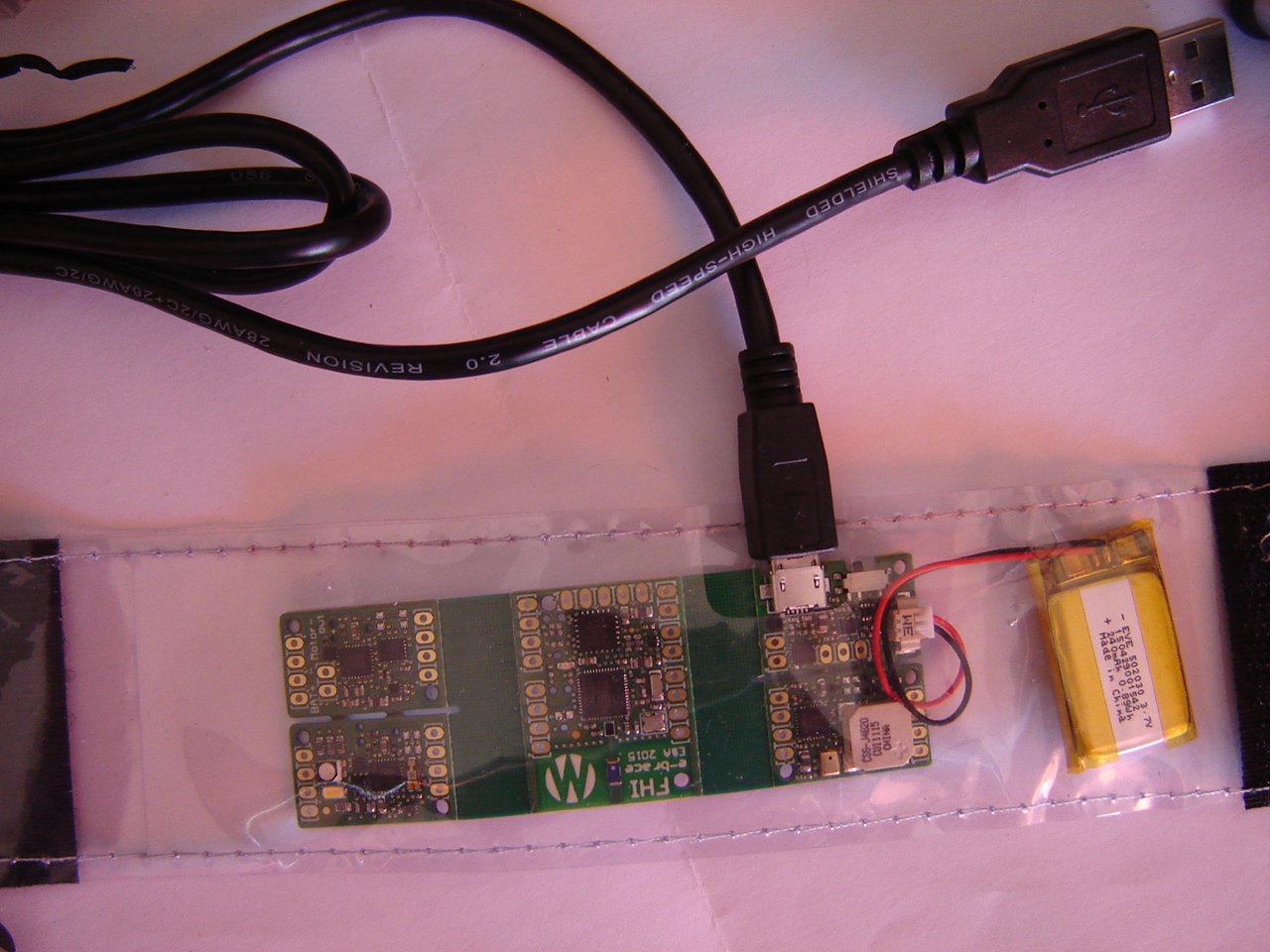
A difference with the RPi and BB that I found so far, is that you
can't login to the device. You can only upload or download
software, so it's a new experience. I will see how much I can do
with it this Arduino.
5 june:
Discovery: At the fischertechnik forum, a member gives an
example of making a screenhot. This starts with copying the
contents of
/dev/fb0 to a
screenshot.raw file and
finisches using
avconv for converting
raw to
png.
It gives a nice screenshot (or better: screencapture) of the
touchscreen. The first results I got with the copy of the contents
/dev/fb0 were distorted and I thought it was from the USB
camera, but in hindsight it looked indeed like the touchscreen.
Mirft: The fixation of the string to the hip-wheel is again
tried, this time with a small part where the string is stuck more
firmly. A picture is shown on the Mirft page. A hand-driven test
forced 1 of the fixations out of its location because of the
tension on the string.
Another problem is that the legs come away from the hip way too
easily: a bit of tension from the string is enough. So the
mounting of the legs probably have to be redesigned.
Youtube: The Youtube videos on the videopage can't be shown
embedded since this is a simple website without javascript. So you
have to use either Google+ or go with the "blind" numbers. For the
videos from TeamBuildingDay 2008, each contestant's first attempt
is made public and they're all uploaded now.
29 May:
Videos: The large series of videos from the Robotmc
TeamBuildingDay is being uploaded to Youtube (and video #1 is
public). Because of the large number of videos, this series will
be on Youtube step by step.
Picasa: I tried to watch videos via Picasa again after
updating flash, but it still doesn't work. Via Google+ it does
work, but by far not everyone uses that.
RPi: Until now, I first used the
raspistill command
to take a picture, and then using my code to read and process it.
Next step is using the command from inside Python so all of it can
be done using Python. After trying and some help from the net, the
correct command is
subprocess.call("raspistill","-o","image.jpg").
The difference it size after resizing to 20%: 2958186 against
73603 bytes. The pictures can be found at the RPi page.
BB: The resizing results in a clear difference. The
original size is 358672, while the 20% resize is 20222 bytes:
460x480 vs. 128x96 resolution. The pictures can be found on the BB
page. Obviously, the RPi cam works standard in much higher
resolution than the Logitech webcam. An interesting fact is that
cv2.imread
on the BB only seems to work with
png, not with
jpg.
I tested with
jpg images, and they didn't load correctly.
The example-code I used to write my code works with
png as
well.
Discovery: I'm still waiting for the documents to be made
available by fischertechnik, so I can continue.
Mirft: In order to keep a leg moving correctly up-down and
forward-backward, the lenselights and the foto-transistors have to
work properly. Since I've connected those to the slave-controller,
the upper foto-transistor for the first leg is
t.Digital(9).
For now it seems to be working. I hope I can make/publish a video
soon.
25 May:
Website: Because the material on both RPi and BB grows, I
decided to give them both their own page.
RPi: Using the earlier taken high-res image, it turns out
to be rather easy in Python with OpenCV to display the image in a
much smaller size:
cv2.resize(image, (0,0), fx=0.2, fy=0.2)
which reduces the size of the image to 20% of its original size.
Next comes saving it using
cv2.imwrite(name, image).
BB: Taking code from a Python example on codeplasma.com, I
can now use my webcam to take an image and display it on screen. A
note on using a webcam on the BB: there are cameras such as the
LI-5M03 that can use the Digital Signal
Processor (part of the BB's OMAP CPU). However, using this DSP
requires the BB to run an old 2.6 kernel and the DSP driver is
obsolete, as I found out during my MSc thesis. So my USB webcam
works pretty fine with this code. This also leads to a new schema
for the BB setup, as shown on the BB page.
Videos: I've uploaded more convention videos to Youtube and
made the first of each year publicly accessible. So now you can
subscribe to my channel, if you like. The other videos I still
keep private, so only accessible from the blog or the video page.
22 May:
RPi: I'm using only VNC to have a desktop and after a short
online search it turns out that the
raspistill and
raspivid
commands give no preview because this is a superimposed videolayer
on top of the desktop and as such not available on VNC. The Pi
camera mounted on a piece of carton using parts of a paperclip.
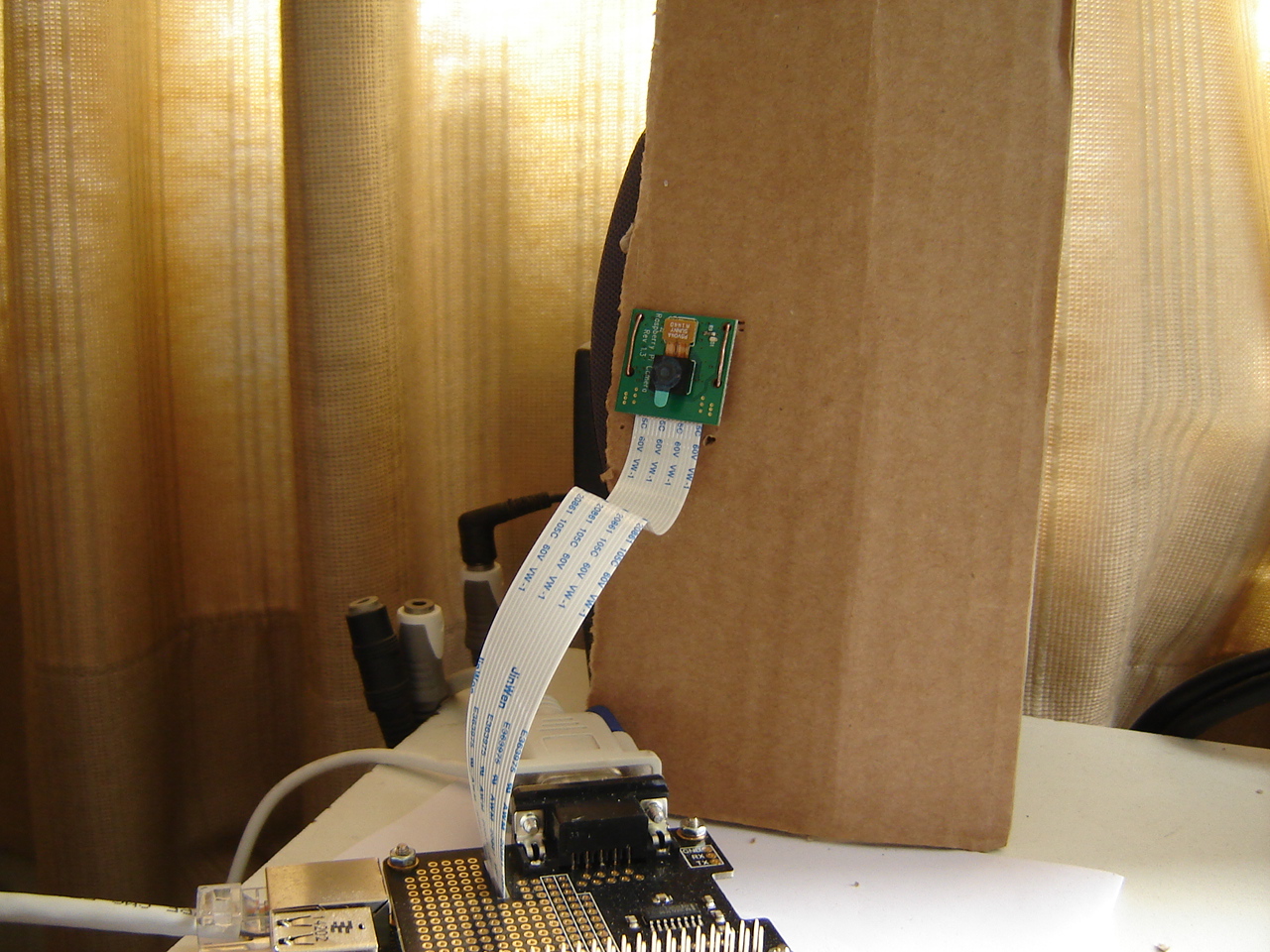
Using
raspivid I create a 5 seconds video, again in h264
format. The video is recorded in 1920x1080 resolution. So far, the
only way I find to replay the video is using
VLC. I
installed this on the RPi, but since the replay-area on screen is
larger than the VNC screen, this is unusable. Solution is to copy
it to the laptop and replay it. An attempt to upload it to Picasa
ends with the message about unrecognized video format: h264 cannot
be converted. Youtube gives a warning but successfully takes the
video.
Using
OpenCV2 on RPi turns out to be recommended for
Python. C/C++ is advised not to use, because RPi is focused on
Python. However, processing and showing a testpicture using
OpenCV2 does not show anything at first but an empty window and
ending up with the message that the window "may not be
responding". After removing some code and only reading and showing
an image it works, although the image goes offscreen due to its
resolution. I wonder if this happens on BB as well. A test on the
laptop shows the earlier taken picture in huge resolution which
goes wide off screen as well.
Mirft: To see if adding a motor on the opposite end of the
rod can be a solution to the problem I described yesterday, see
the pictures and
video. A first test seems to be successful.
BB: Using OpenCV turns out to be a problem. After the
installation of OpenCV, the OpenCV2 instruction imread() is not
available, so the suspicion is that OpenCV1 is installed instead
of 2. To install v.2 I'll have to download the source and
cross-compile. Edit: I made a mistake, so my suspicion was wrong.
OpenCV works great on BB as well.
Mydfir: I realized that these videos were not on the video
page yet. So I added them and put them on Youtube (unlisted) as
well.
Videos: the ft 2009 convention videos are published
publicly on Youtube.
20 May
Discovery: Via the ft community forum I received an answer
on how to make snapshots with the ft USB camera using an
imagestream on the TXT. This works nicely and I put it into a
script. These jpg snapshots show the driving robot and TXT
controller at a resolution of 320x240. The reason of the double
image is uncIear; I suspect the stream is slow and needs some time
to grab.
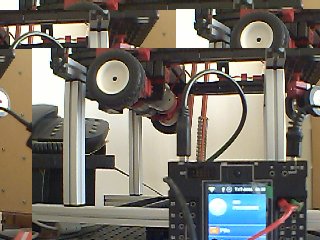
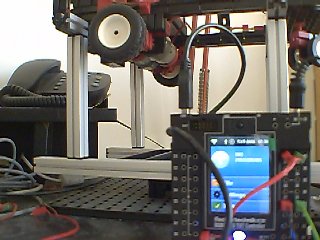
Working with ROBOPro via wine on the TXT works fine except for the
camera; this gives a black image in preview. I'm not the only one,
according to the forum. Since it works via wine, I'm more than
happy to remove VirtualBox/Win7 from my laptop. 45 updates in a
few days ("do not shutdown"/"configuring updates") is too much for
a proprietary operating system.
RPi: I now also have the Pi-camera, so I can start
experimenting with
OpenCV
on Python and possibly C or C++ again.

A first test using
raspistill resulted in a nice
picture. However, although the video
raspivid delivered an
.h264 video, I can't replay it yet because players don't recognize
it. Also streaming video using
nc and
mplayer has
no results yet.
Mirft: apart from the software, the mechanics are naturally
very important. The idea was to have the upper leg move in an
ellipse. However, an easier way to go seems to lift the leg
completely, then go maximal horizontal and go down again. While
testing this idea a mechanical problem with the chains surfaces,
as shown in this short
video (Picasa) or this
video
(Youtube). A first solution is to loosen up the tension in the 2nd
and 3rd chain (oppositie the motors), but this gives no real
solution. Then it seems that the rod at the end of the first chain
(so at the motors side) is not sufficiently inside the gear, but
putting it fully in gives no solution either.
18 May
Discovery: Because the steppermotor doesn't run, I look at
a few sample programs and find that those are quite similar to
mine. So I try again, and this time it works: the steppermotor
runs. No clue about the difference. What I notice, is that the
batterypack is emptied within 10 minutes. The TXT controller is
power hungry and with a motor attached it goes fast.
What I forgot is that on Linux, a .bin file usually has to be
changed into an executable by
chmod +w <file>.
However, after doing so with
Test3.bin, this error popped
up:
line 1: syntax error: unterminated quoted string.
Doing the same with
Test.bin results in even more errors.
As an aside: I also managed to install ROBOPro via wine, which
seems to work. Next comes testing it with the TXT.
RPi: When programming in Python, obviously there are 2
versions. Via the desktop they're indicated by IDLE (2.7.3) and
IDLE3 (3.2.3). For minicom (and thus in any terminal session) I
have to start
python3 to get this version.
A small programming example shows a remarkable difference between
the 2 versions.
name = input('what is your name') gives an
error in 2.7.3 while it runs fine in 3.2.3.
Programming the serial port:
RPi: After installing
py-serial on the RPi side and
pyserial on the laptop side, a short program is written to
see what the results of serial communication are using Python
instead of C. Some quick tests: using
sudo python serialtest.py
on RPi towards the laptop it shows no delay nor missing characters
on the laptop. Then a similar test from the laptop towards the RPi
shows there's no delay nor missing characters on the RPi either.
BB: After installing
python-serial, I can test the
same Python code on BB. There is immediate response on screen and
there are no characters missing. Hence I have to assume for now
that my C code is not working as it should. The Python code was
written in version 2.7.6.
15 May
Discovery: Since I still can't figure out which /dev/
corresponds to which in/output, I've decided to create a program
using RoboPro, and then see what happens. Unfortunately, nothing
happens. In test mode all in- and output works, but nothing
happens when a test program with steppermotor (runs the motor for
5 seconds) is run.
The test program using a simple motor does work. The sourcecode is
named
Test.rpp and its content shows as an XML file. After
compilation/uploading to the TXT, it turns out via ssh that the
binary is named
Test.bin and is located in the
ROBOProFiles directory. On the file-list via the TXT menu only the
names
Test shows. An attempt to run
Test.bin from
the ssh-terminal commandline shows it won't work that way: with
644 permission it's not executable. Running it from the TXT
display works fine. So more stuff to figure out.
12 May
Movies: Because of site-statistics I realized that my
announcement of movies make visitors to go straight to the movies
page, while the BB and Discovery movies were not made available
there. This error is now corrected.
RPi: A short video is available via both the movie and the
embedded systems page.
Using Python-Idle shows an unexpected difference. When I start the
Python shell via minicom, v. 2.7.3 is started, but when I start
Idle, it uses v. 3.2.3. And since I can't logout from the pi-user,
seemingly due to a frame buffer issue, I will have to deal with
this for now.
Picasa-videos: right now, they're only watchable on
Picasa+/Google+. From the Picasa forum I read that things at
Google are changing and maybe are fixed by the end of May. Until
then please watch my new videos on Youtube. IF this whole video
stuff gets fixed, I will remove the videos from Youtube. If NOT, I
will see then.
11 May
Mirft: I received the 1:125 motor and after a short test I'm
happy. This is indeed the motor I need for horizontal movement of
the legs. After replacing the 1:50 motor, as expected other
problems surface. So there's a task list.
- improving the connection of the string to the hip.
- the motor keeps pulling when the utmost position is reached so
either the running time of the motor must have a limit or sensors
have to be added.
- reprogramming is badly needed. Using Python for this again.
To show the new motor and make things clear, I've posted some
pictures.
Discovery: Because of the Picasa issues ("invalid
parameters") that make my videos unwatchable, I've put the video
on Youtube. Check for the video link on the
Discovery page.
7 May
Discovery: I spent some time trying to find out which
/dev/xxx files could belong to the interfaces I1-I8, M1-M4 and
C1-C4. After all, when I want to read out a sensor, count pulses
from a motor or control the speed of a motor I need to address the
correct device file. I have asked fishertechnik for more
information on this, so hopefully I can start the actual
programming.
In the meantime, I created a short video to show more, which you
can access from the
Discovery
page.
4 May
Discovery: After the first exploration of the TXT
controller, I found it cumbersome to have to switch the WiFi
connection from the TXT to my own WiFi. It already went wrong
twice with
nfs mount errors as a result. Then I
realized the solution was easy: use the wired socket for the
internet connection and nfs mount and use the WiFi for the TXT
connection. Fortunately I had a spare network cable and a network
switch close at hand, so the connection problems are solved.
Another thing is that the TXT is not just a controller. Having an
ARMv7 CPU makes it an embedded system as well. Onboard compilation
like I do with the BB and RBPi is a no-go because the TXT safety
document clearly states that a C/C++ compiler is not delivered
with it. This is simply solved by installing the Linaro
cross-compiler on the laptop with is standard available in the
Ubuntu repositories. So now I will do cross-compilation on the
laptop and copy the binary to the TXT using scp (secure copy). A
simple test program HelloWorld as expected confirms this idea
works.
Another topic is how to get an image from the camera without using
Windows. I tested it shortly using Windows and the hardware is ok.
In the documentation is stated that the camera uses /dev/fb0 as
framebuffer to store an image. Then it is simple to copy that
image into another file: e.g.
cp /dev/fb0 video.
However, the format is probably RAW and there are multiple RAW
formats. So the next task is to figure out how to get a usable
image.
1 May
RaspberryPi: During this week I conducted the serial
communication test on the RBPi several times and oddly enough, the
behaviour of minicom on RBPi changed: this time into rather
inconsistent behaviour. It either did not show anything, or it
showed partly, or completely. It also occurs that minicom reports
"Cannot open /dev/ttyAMA0!" after receiving and displaying a
string.
On
Mirft: After looking at the webshop
http://www.fischerfriendswoman.de/
I found a powermotor with ratio 125:1 which would result in a much
lower speed of the horizontal legs movement. So I ordered it...
Then the
pneumatic hand. After an hiatus of some months, I
tried to upload the Basic-language version of the original Python
code again in order to have the hand work in offline-node.
Unfortunately, nothing has changed and I still get (among
others) this error:
Error uploading Program: Return
value for 0xC0, 0x20 is 0xef. Since the Basic expert has no
clue and the (seemingly) only other Linux user on the forum has no
clue either, I've asked the manufacturer but no answer as yet.
And on 30 May I received the
TXT
Discovery
set. After unpacking, there are 2 white plastic (why
plastic ?!) crates with parts, a manual and a cd with ROBOPro
4.1.5. Using Linux, I won't use it for programming but it is
needed for some tests and firmware updates and before doing
anything with the controller, the firmware needs to be updated
from 4.1.0.0 to 4.1.6.
Since I don't plan to use Windows often, I will install it
virtualized. I tried to install it under
wine but
instead of a setup.exe, it comes with a setup.msi and
wine
msiexec /i <installer> fails to run. So I had to
install Windows7 in
VirtualBox. After installation of Windows7,
ROBOPro 4.1.5 is installed from cd/dvd, and this leads to a
complete nightmare because it installs by default in
Users\..\.AppData\. And any directoryname or filename starting
with a dot is hidden and in Windows
not indexed. So while
the software starts, any file it searches won't be found such as
any pdf file ROBOPro looks for. Of course there's a work-around
like using
TotalCommander
and then search for pdf file and then automatically open it in a
pdf reader but for the average computeruser this won't work.
My first solution to is to remove ROBOPro and install it into the
normally accessible directory C:\ROBOPro using advanced
installation. But even then it won't find pdf files or firmware to
update. It turns out it is looking for the files in the old
.AppData location. Ugh. As I don't find a way to change the
directory it looks for, I reinstall it in the users directory
again and this time the firmware is upgraded successfully to
4.1.6. Yay.
After this rather slow start, of course some experiments. It turns
out that the TXT is a WLAN dhcp server. This means I can't access
it from my own LAN but instead have to disconnect the laptop from
the LAN and connect to the TXT. There is a document with security
advices and explanation on how to change settings such as
passwords. However, there is no information on how to proceed and
program from a Linux based environment although the TXT itself is
Linux based: I can make a good ssh connection to the TXT.
Besides that, at the fischertechnik 2014 convention, I had a talk
with the Knobloch boss who assured me that there would be drivers
for Ubuntu. Since I know there are more people waiting for these
Linux drivers, I hope I don't have to wait very long.
24 April
Further tests on the laptop to RBPi communication show that
minicom on the RBPi doesn't have to be restarted after each test.
Each received string is written over the last one. However, the
received characters are not the fully sent string. Examples:
23456789098765432 is displayed as 98765432 and
abcdefghijklmnonmlkjihgfedcba is displayed as jklmnomlkjihgf. So
not just the beginning is missing, the end is missing as well.
Although on both the BB and the RBPi apparently characters are
lost when receiving, they are not the same chipsets: BB has
omap-serial (hence /dev/ttyO2 with capital letter O) while RBPi
has AMA which according to
this post seems to be
AMBA.
For now, the question remains: why do they loose characters ?
23 April
Today I received the Serial Pi Plus and mounted it.
Starting a connection with minicom was easy using the null-modem
cable. See the
pictures. Just too
bad I don't have another null-modem cable, because now I can only
have 1 serial connection at a time: either the BB or the RBPi. A
kind of XOR situation. My serial communication code has of course
to be changed. The serial port on the Serial Pi Plus is called
/dev/ttyAMA0. After that, writing to minicom goes well.
Interestingly, writing from both BB and RBPi to minicom on the
laptop keeps working without a restart of minicom while in the
other direction it requires a restart of minicom after each write.
22 April
So far I've been reporting about the BB, but I thought it was
time to spend some time with the Raspberry Pi B+. I ordered the
Serial Pi Plus, which is an add-on with an RS232 connector. Using
this, I can do exactly the same as with the BB: using a minicom
session for debugging. Another option would have been to use a
PL2303-based cable, which uses 4 GPIO (General Purpose Input
Output) pins for serial connection and plugs into a USB port of a
computer. However, the website says it's EndOfLife, Besides that,
it also delivers power to the RPi, which it already gets.
Also, the RPi should do fine with imaging. This leads to some
experimenting with 2 programs:
guvcview
and
xsane.
The first is a nice tool with which you can in detail adjust the
cam settings and record both images and video's. However: apart
from clearly recording sound, all images and video's are black, no
matter which settings. To see if my webcam (Logitech
QuickCam Fusion) actually works I use xsane
(which I frequently use to scan images with an ordinary flatbed
scanner) and with great result. So the question is why guvcview
shows only black. During my MSc thesis, the combination of this
same webcam and the
BB-xM
worked fine on guvcview.
19 April
I created a short
video explaning how the BB is connected.
More video's probably to come.
17 April
On the serial communication from and to the BB, I've found an
interesting fact. After searching the net, I noticed a remark that
you actually can read from /dev/ttyO2 but that the first
characters are ignored. To test this, I changed my usual
test-string length from 6 to 20. When then happens, shows that the
port is read but that the number of read characters varies. With
the character string "1234567890987654321" sent several times, the
received (or more accurate: displayed) strings are: 7654321,
890987654321, 4567890987654321, 7890987654321, 34567890987654321,
7890987654321.
- After the sending of a character string, I have to restart both
my own program on the laptop and minicom on the BB.
- Now that I know this receiving behaviour, I have to change my
code a bit on the BB side in such a way that it can receive a
longer string.
Of course, the question is: why does it show this receiving
behaviour in the first place.
9 April
This past week I've been busy with the BB communication as
well as the Mirft simulation.
On the BB, I decided to do a different test by installing Minicom
and see I characters sent from the laptop would appear in Minicom
on the BB. The result was that it doesn't. Even worse: despite the
correct settings, Minicom shows after a lengthy delay the message
that it "cannot open /dev/ttyO2". So the question is why can it
write, but not read ? Some suggestions are it may have to do with
uboot settings or even kernel issues. I'm not convinced about
either.
The Mirft simulation has not made progress in that it shows the
intended movement. Somehow, there's a discrepancy between my model
and the inverse kinematics possibilities: location can't be
reached. Which I seriously doubt. In the mean time I've drawn a
sketch using
Inkscape
to illustrate how the legs should be able to move. So if you
combine vertical and horizontal, you also can have an elliptic
move. The text is inserted by using
textext.
To be continued.
2 April
After some attempts to become familiar with git, I finally
managed to add my robotics Python code in 3 separate repo's. The
code won't be of much use for anyone, since it's for the
combination of Linux-ft RoboInterface-ft DataLink but it gives an
nice inside look (I think). My GitHub handle is hvn52.
27 march
The serial communication is still not working the way I want.
Using minicom, I can see that the text from the BB is received.
However, when I use my own code, there's no prove that anything is
read from /dev/ttyUSB0. I've added some code that writes to a text
file whether anything is being read or not, and the text being
written is telling me nothing is being read. Maybe my reading code
is wrong...
Also some more action on the simulation. The new robotics toolbox
is installed and while the demo shows how it's done...my own
manipulator (i.e. robot) is not moving. The code shows 2 errors: a
point is unreachable and some submatrix error. Somehow I hope this
is a kinematics bug, and not my fault. Will see.
18 march
After some online consult on strings and character arrays and
re-reading K&R ("The C-programming language" by
Kernighan and Richie) about it, I managed to send keyboard input
over the serial port and read it in minicom terminal. Odd is
though, that now suddenly I have to run the program using sudo.
Although this is quite logical (after all, writing to/reading from
the serial port uses system calls), earlier it just worked without
sudo.
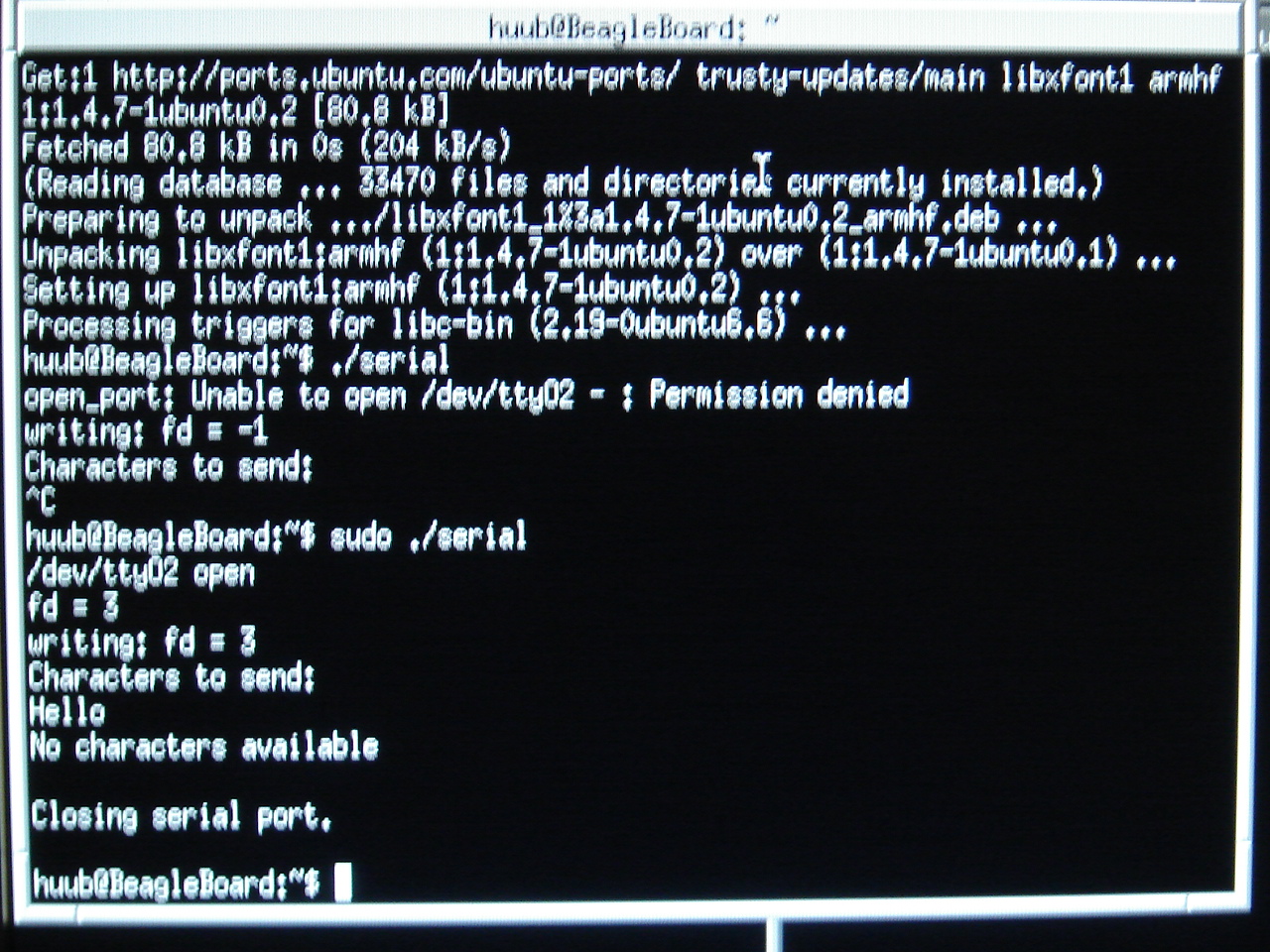
17 march
I resumed serial programming on the BeagleBoard and found that
I made 2 typos: /dev/tty02 instead of /dev/ttyO2 and an
if-statement comparing to 1 instead of -1. Oops. The result is
that I can now send characters ("Hello") over the serial line and
actually see them in on the commandline in the terminal on the
laptop. Yay.
A few more (incubation/check) days to wait until the improved
robotics toolbox is ready to install in Scilab. Can hardly wait to
get on with that.
Last for now is an updated graphic of Mirft.
14 march 2015
It took some time but it comes to the point where the graphical
model starts looking like the actual one. Screenshot of the
current status:
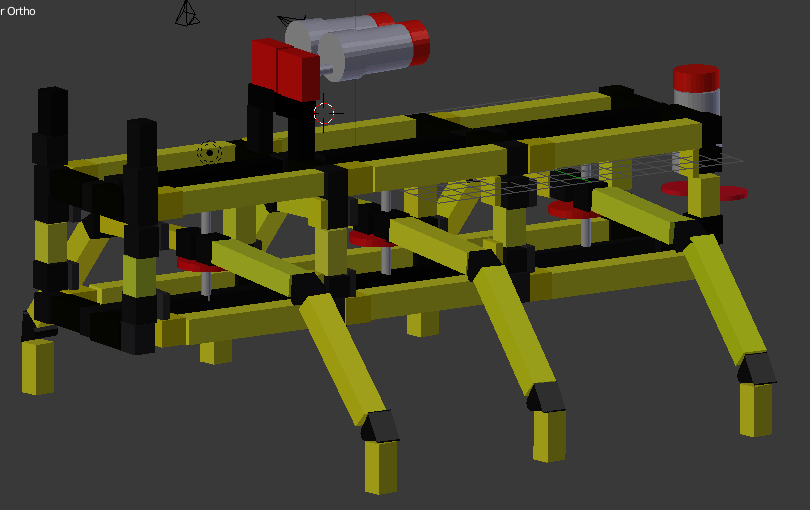
In Blender this is in 3D and can be rotated and zoomed in/out at
will. In the process, I'm getting a bit more familiar with Blender
(which has way too many options for me atm).
11 march 2015
It turns out that the original Robotics Toolbox as used in Matlab
has a flaw in (at least) 1 inverse kinematics function: ikine3.
The Scilab version is an next-to-identical port of it and so it
contains the flaw as well and doesn't work. And guess what? I need
it. To be continued (I hope).
10 march 2015
Today I managed to create the Mirft simulation in
Scilab: 6 legs in the starting position. Next task is to get it
animated using inverse kinematics.
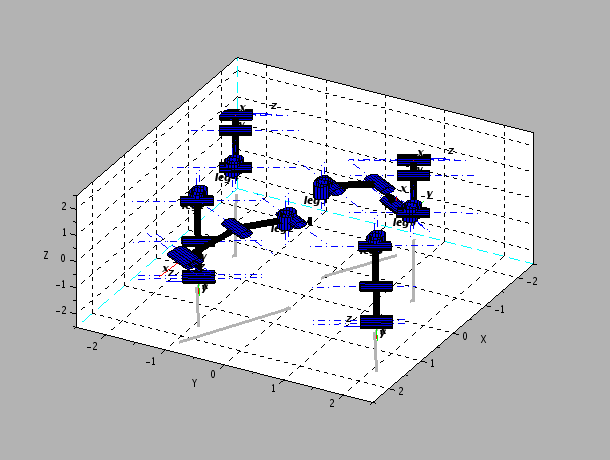
5 march 2015
Today I added an
embedded systems
page to show (and write about) my experiments with a classical
BeagleBoard
Rev C4 in more detail, just like I do with the robots.
25 february 2015
I've started modelling my walking robot Mirft both graphically
and mathematically. For the graphical model I use
Blender3D and
for the mathematical model I use
Scilab. Of course the graphical model is to
see how it looks like while the mathematical model is to see if it
works. Scilab Atoms offers a nice Robotics Toolkit (free and
actually a port from a toolbox for Matlab) which I use. The
problem I'm facing now is that the examples as shown in the Help
don't work for me when I want to display 2 legs in the same
simulation. As long as this doesn't work, it's no use to try the
full Mirft with 6 legs in it.
12 February 2015
So, I was advised to start blogging....about my projects and
me. Very short about me: I have a MSc Embedded Systems with
combined specialization in Systems&Control and Robotics from
Delft University of Technology, But what are my projects ? Again
rather short: my robots. Those are Mirft (
My
insectoid
robot of
fiscer
technik), Mydfir (
My driving
fischertechnik
interface
robot) and the
robot hand.).
Mirft
I started developing Mirft back 2006 because I wanted to build a
better walking robot than the model shown in the examples from
fischertechnik. As you can see from the many pictures, this has
been quite a project and it's not finished by a long shot. Why ?
Because of available time, ideas and material (= money). It is
supposed to walk some time in the future, but before that happens
quite a few problems need to be solved.
There is the horizontal movement of the legs: currently they move
way too fast and I don't have a motor that is about 150:1 or
slower. And before I buy, I want to be sure I buy the right
motor....
Then there is the sensoring: how do I detect that the legs are at
the utmost vertical position so that the motors stop ? Odometry is
hard to realize with cable/rope, so light sensors are more
suitable. The idea is to use a light -sensitive transistor which
captures the light beam and gives a signal upon interruption when
the leg is either pulled up or down. Problem with this is that I
don't have enough lamps and transistors yet. Again, money can
buy...
Next problem is the material to pull the legs up and down. Right
now, for testing purposes, I use sisal. By far not strong enough
to let it stand on its legs, but for the testing of movement it
suffices. In the end it needs to be replaced by nylon.
Another issue is power. So far, its power is delivered by a
standard ft-power adapter. This works as long as it remains on its
scaffold. When it walks, it needs strong batteries.
Finally, for now, the material of its legs. Being made of several
pieces, it remains to be seen if its strong enough to carry the
weight of the robot.
To be continued....(Mirft)
Mydfir
This robot is much simpler. Directly derived from an example by
ft, I just added a few ideas of my own: coloured lamps and active
sonar. It works pretty well so little has to be done, or I should
come up with a bright new addition :)
Last change I made was to the software: some data aquisition by
writing the colour and distances returned by the robot into a
file.
To be continued....(Mydfir)
The hand
This started out of curiosity: can I make a finger move,
either electrically or otherwise ? Electrically proved to be hard:
a small motor (no problem), some gears (no problem), chain (no
problem). The problem proved to be the guidance of the chain since
it got stuck continuously. So I built another finger, and used the
pneumatic ft set: that works much quicker. Writing the program was
easy enough, and with some mini-switches I can let each 1 of the 3
fingers move on each own or run a routine with all 3.